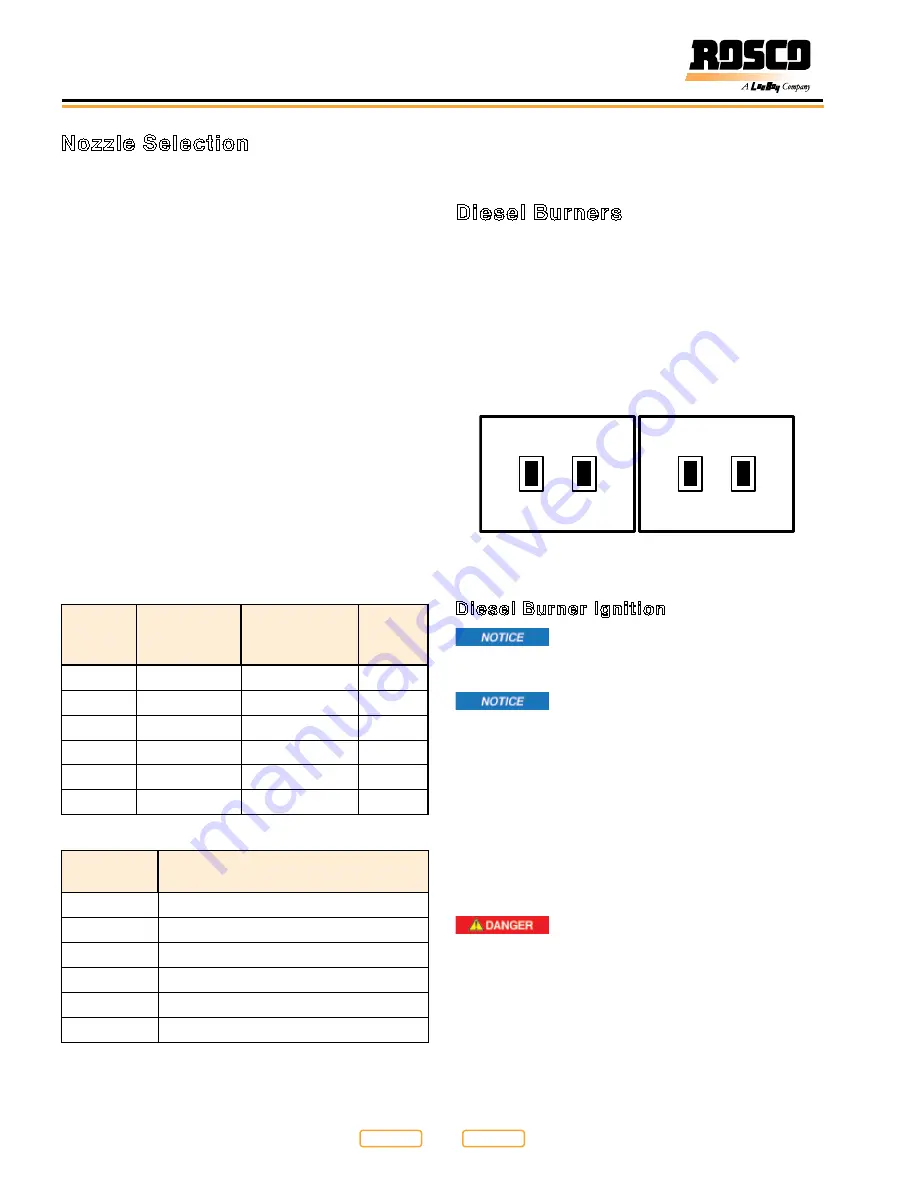
6-10
Rosco Maximizer 3B Asphalt Distributor
Operation
Burners & Torch
Operation
Diesel Burners
Control switches for the electronic ignited diesel
burners are mounted on the left rear fender, (
1. Fuel Switch: Activates burner fuel solenoid and
ignites burner. Turn off to extinguish burner.
2. Blower Switch: Activates blower and fuel pump.
Burner will ignite if fuel switch is on.
UPPER BURNER
FUEL
BLOWER
READ SAFETY INSTRUCTIONS
PRIOR TO USE
READ SAFETY INSTRUCTIONS
PRIOR TO USE
FUEL
BLOWER
LOWER BURNER
Fender Diesel Burner Switches
Figure 6-7
Diesel Burner Ignition
Before heating asphalt material, refer
to Systems Overview, Burner System, earlier in this
section for further information and precautions.
Run the burners for short periods
of time (15 minutes ON, 15 minutes OFF) to allow
the heat to dissipate through the material. This will
prevent damage to the flue liner.
NOTE: If your unit is equipped with dual diesel burners
you will have separate controls for each burner,
(
). This allows the operator to run one
or both of the burners to heat the material. Light
the upper burner using the same steps as with
the lower burner.
1. Be sure the unit is sitting on a level area.
Do not put your head in the tank.
Serious injury or death could result from breathing
poisonous fumes.
2.
With a flash light, look into the tank from the top and
check that there is no visible water or condensation
in the tank. If there is, drain the tank to an approved
container before lighting the burner. Dispose of
material and water according to local, state and
federal regulations.
Nozzle Selection
The correct nozzle selection depends on:
1. the application rate setting
2. the truck speed
3. the type of material being sprayed.
The standard Rosco nozzle size is a NO. 1. However,
other factors will determine efficiency and the quality
of the spray pattern. Exceeding nozzle maximum flow
rate may cause fogging and inconsistent application
rates. Using a nozzle that is too large will cause a poor
spray pattern, (
Table 6-1. Nozzle Size to Flow Rate
and
Table 6-2. Nozzle Size to Application Rate
).
The recommended nozzle angle is 20° and is set to
that specification at the factory. After changing nozzles,
or when adjustments need to be made, use the Nozzle
Alignment Wrench and the Valve Alignment Wrench for
accurate positioning. Tools are provided with each unit,
(
NOTE: For additional information about nozzle selection
and adjustment, see applicable troubleshooting
topics (see
Table 6-1. Nozzle Size to Flow Rate
NOZZLE
SIZE
RECOMM-
ENDED
FLOW - GPM
APPLICATION
RATE - GAL /
SQ. YD.
ROSCO
PN
00
1.2
.03 - .08
35565
0
3.0
.05 - .20
32917
1
4.0
.10 - .30
32918
1.5
6.0
.15 - .40
36299
2
8.5
.25 - .55
32919
3
13.5
.35 - 1.00
32920
Table 6-2. Nozzle Size to Application Rate
NOZZLE
SIZE
APPLICATION RATE (GPM)
00
Extremely Light (1.5)
0
Light (4.0)
1
General (5.0)
1.5
Intermediate w/ certain emulsions (6.0)
2
Heavy (10.0)
3
Extra Heavy (15.0)
Return to
Last Viewed