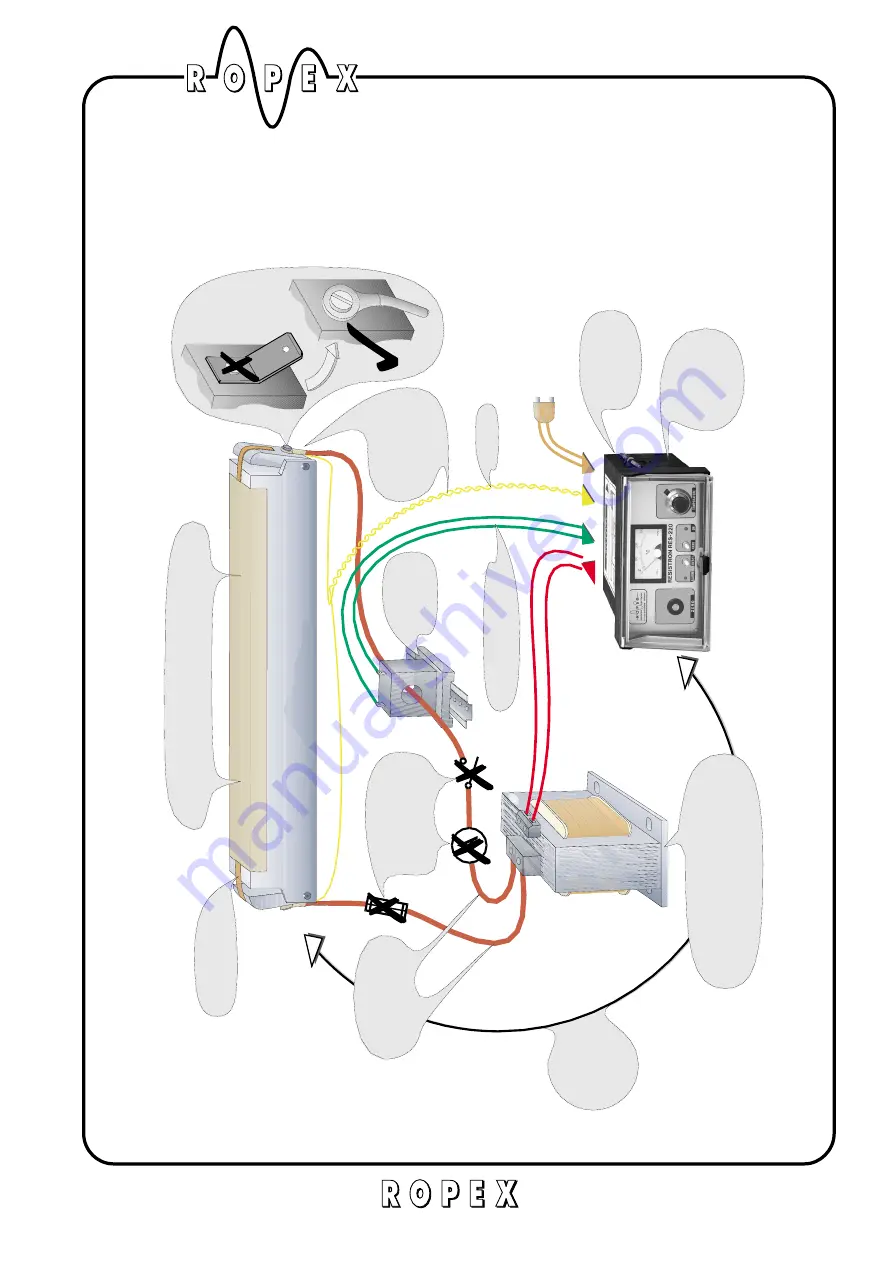
INSTALLATION - INSTRUCTIONS
Line
Transformer
Curr
ent
transformer
U1 Prim.
Heatseal
band
R=
f(
T)
U2 Sec.
A
F
Avoid
long
cable
length
Suf
ficient
wire
cross
section
Heatseal
element
with
coppered
ends
Use
heatseal
bands
with
appropiate
temperature
coef
ficient
No
additional
resistances
in
the
secondary
circuit
Observe
the
number
of
passes
twisted
No
push on
connectors
Current
measuring
wires
I
R
Correct
dimensions
of
transformer
-secondary
voltage
-power -duty
cycle
Contr
oller
Set
DIP-Switch
into
correct
position
Set
jumper
for
line
frequency
into
proper
position
Voltage
measuring
wire
U
connected
directly
to
the
ends
of
heatseal
elements
R
INDUSTRIE - ELEKTRONIK GmbH