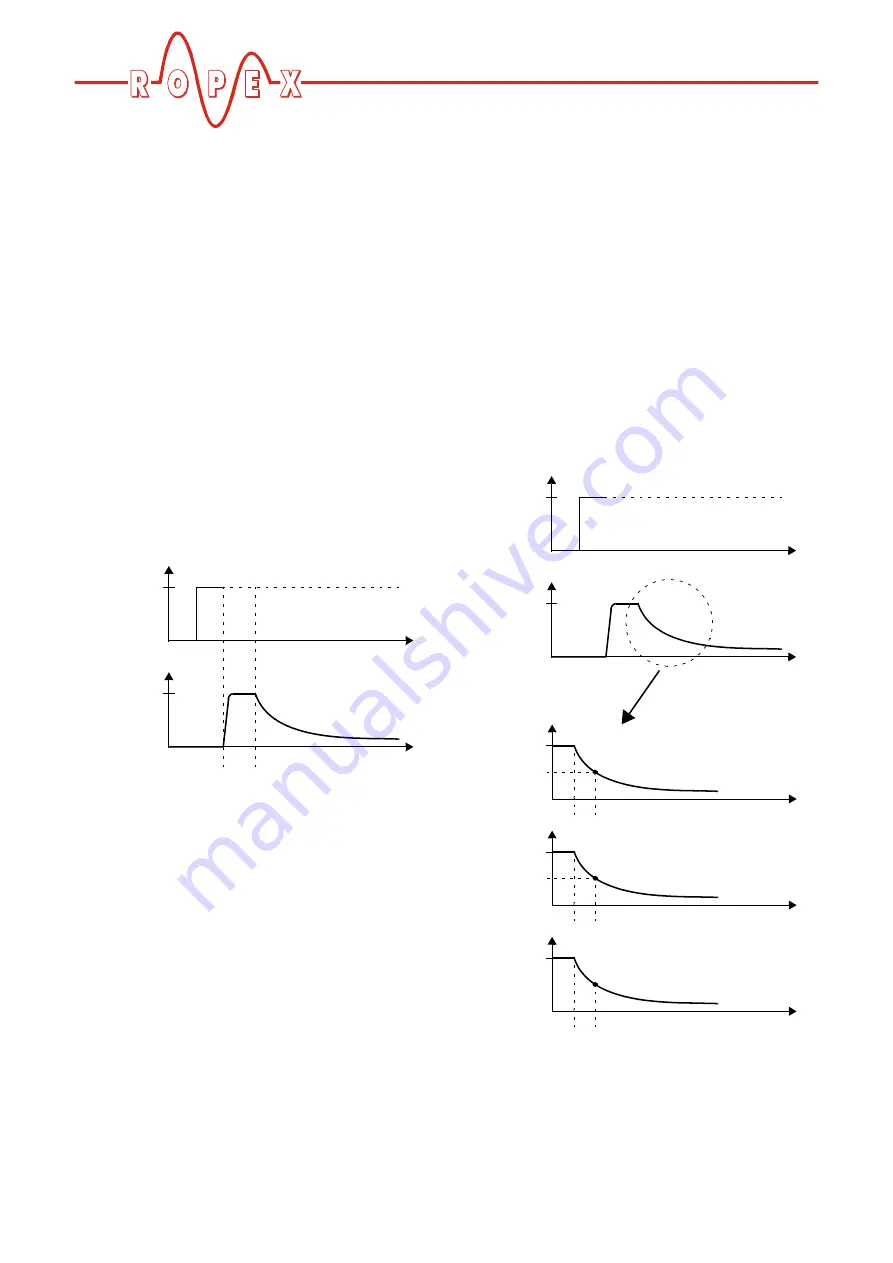
Controller functions
40
UPT-640 (as of SW 100)
The starting delay can be set in the range from 0 to
9.99s. A delay of 0s is defined as the factory setting. In
this case, the heating process begins as soon as the
"START" signal is activated.
9.23.3 Setting the heatsealing time
This menu step is used to enter the heatsealing time.
There are two possible ways to set the heatsealing
time:
1.
"0…5.00s"
The heatsealing time can be set in the range from 0
to 99.9s. The factory setting is 0.1s.
2.
"EXT"
(This setting is possible as of software revision 013)
The heatsealing time is controlled by the "START"
signal (24VDC signal applied to terminals 3+4 or
contact applied to terminals 2+7). The duration of
the heatsealing time is equal to the active time of the
"START" signal.
9.23.4 Setting the cooling mode
Various criteria for the end of the cooling phase can be
specified with step 210 in the Configuration menu of the
UPT-640 (as of SW 100) controller. The possible set-
tings are as follows:
1.
"Absolute" (Factory setting)
The cooling phase ends when the ACTUAL tempe-
rature of the heatsealing band falls below a speci-
fied temperature value. This cooling temperature
can be set with step 105 in the Settings menu.
2.
"Relative"
The cooling phase ends when the ACTUAL tempe-
rature falls to a value corresponding to X% of the
SET temperature. This percentage cooling value
can be set with step 105 in the Settings menu.
Example:
SET temperature = 180°C, cooling value = 60%
Cooling phase ends when ACTUAL
temperature
≤
108°C
3.
"Time"
The cooling phase ends after a specified time in
seconds and is independent of the ACTUAL tempe-
rature. This cooling time can be set with step 105 in
the Settings menu.
The various cooling modes are shown below:
ACTUAL
temp.
START
signal
24VDC
T
t
t
0
0
t
2
= Heating phase
t
2
ACTUAL
temp.
START
signal
24VDC
T
t
t
0
0
Cooling mode
T
t
0
T
t
0
T
t
0
Absolute
Relative
Time
T
2
X%
t
3
t
3
t
3
t
3
= Cooling phase in °C
t
3
= Cooling phase as
% of set point
t
3
= Cooling phase in s.