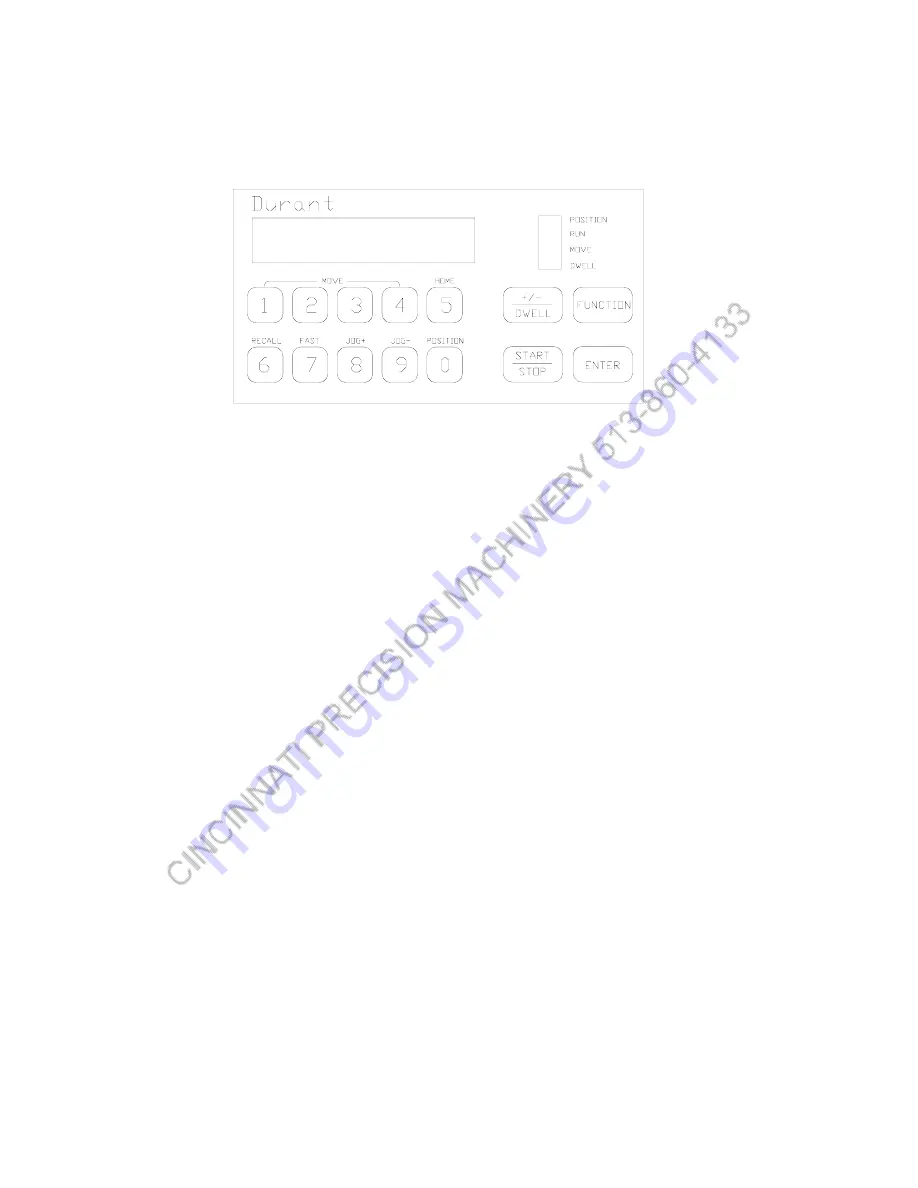
TO CHANGE CURRENT DISPLAYED POSITION
Since there is no “home” or “zero” position, we use the following
procedure to tell the backgauge where it is and it begins to count
from that position.
1. Hit
FUNCTION
ENTER
.
Note that all four (4) LED's are flashing.
2. Hit
FUNCTION 65 ENTER.
Input new current position.
3. Hit
ENTER
again.
4. Hit
START/STOP
to exit programming mode.
27
Summary of Contents for 10M14-H
Page 5: ...3 ...
Page 13: ...11 ...
Page 14: ...Figure 2 12 ...
Page 17: ...5 4 2 1 3 Figure 3a ADJUSTMENT NUT Figure 3b 15 ...
Page 30: ...APPENDIX 10M14 H PHYSICAL DIMENSIONS FIGURE 1 ...
Page 32: ...230V STD ELECTRICAL WIRING DIAGRAM FIGURE 3A ...
Page 33: ...230V STD ELECTRICAL PANEL LAYOUT FIGURE 3B ...
Page 34: ...230V DRO ELECTRICAL WIRING DIAGRAM FIGURE 4A ...
Page 35: ...230V DRO ELECTRICAL PANEL LAYOUT FIGURE 4B ...
Page 36: ......
Page 38: ......
Page 60: ...6M14 10M14 Air Operated Front Material Return Page 21 Electrical Diagram ...
Page 61: ...6M14 10M14 Air Operated Front Material Return Page 22 Air Circuit Diagram ...
Page 62: ...NOTES Copyright 1999 Roper Whitney of Rockford Inc 2833 Huffman Blvd Rockford Illinois 61103 ...
Page 65: ...SECTION 1 BASIC MECHANICAL ...
Page 66: ...1 3 4 5 6 7 8 9 10 11 12 13 11 10 9 1 1 8 7 4 5 15 6 14 3 2 FIG 1 BASIC MECHANICAL 10M14 16 ...
Page 68: ...1 2 7 6 8 5 4 3 FIG 2 BASIC MECHANICAL 10M14 ...
Page 70: ...1 5 1 2 8 11 10 9 3 4 3 6 7 2 FIG 3 BASIC MECHANICAL 10M14 ...
Page 76: ...3 1 2 4 9 5 6 8 7 10 14 11 12 13 6 FIG 6 BASIC MECHANICAL 10M14 ...
Page 78: ...11 2 10 1 2 9 1 5 4 3 7 1 2 2 8 1 1 6 2 FIG 7 BASIC MECHANICAL 10M14 ...
Page 82: ......
Page 83: ...SECTION 2 ELECTRICAL AND CONTROLS ...
Page 84: ...FIG 1 ELECTRICAL AND CONTROLS 10M14 ...
Page 86: ...FIG 2 ELECTRICAL AND CONTROLS 10M14 ...
Page 88: ...FIG 3 ELECTRICAL AND CONTROLS 10M14 ...
Page 90: ...1 2 3 4 5 13 7 12 11 10 9 6a 6 7 6a 8 FIG 4 ELECTRICAL AND CONTROLS 10M14 ...
Page 92: ......
Page 93: ...SECTION 3 BACKGAUGE AND MATERIAL RETURN ...
Page 98: ...FIG 3 BACKGAUGE AND RETURN 10M14 ...
Page 102: ...FIG 5 BACKGAUGE AND RETURN 10M14 ...