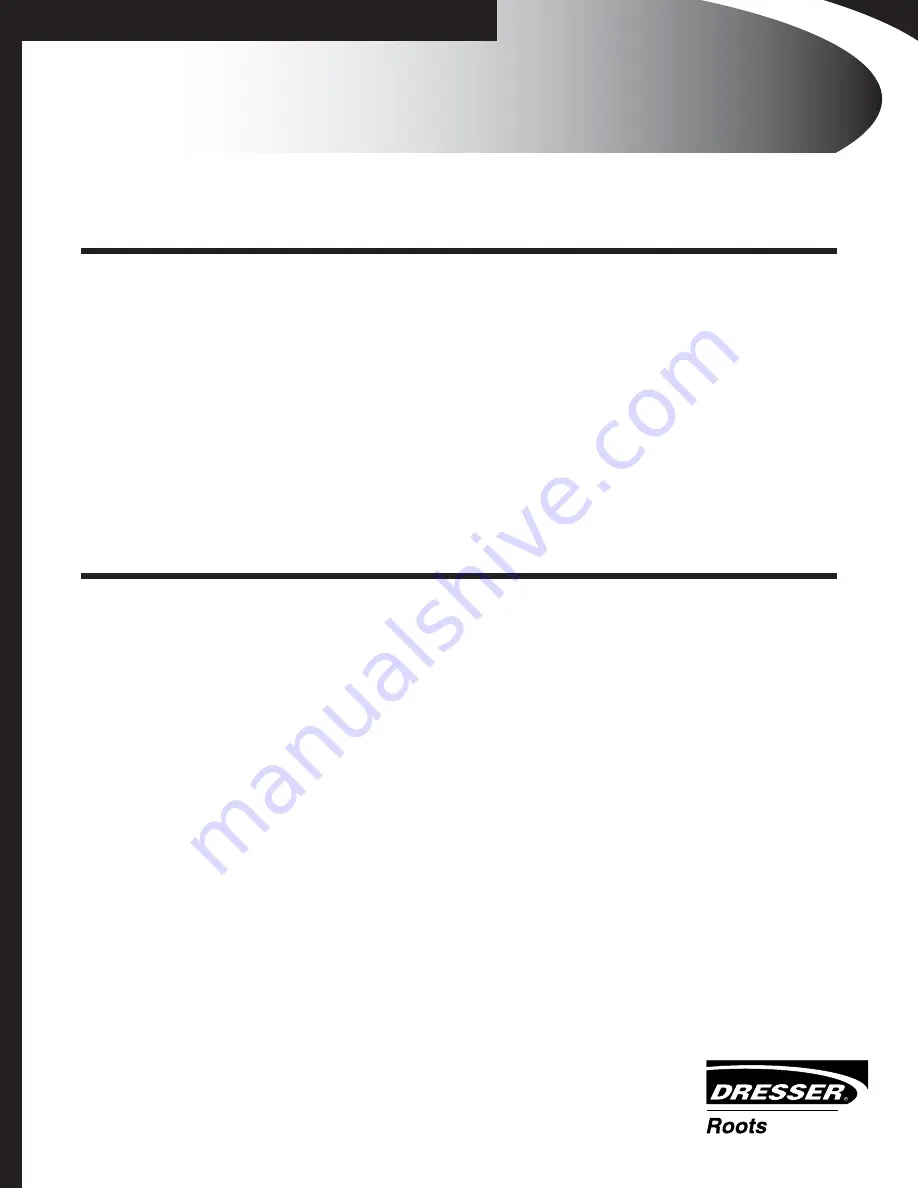
ROOTS
ROOTS
ROOTS
BLOWERS EXHAUSTERS COMPRESSORS
™
™
INSTALLATION OPERATION MAINTENANCE
❏
In event of trouble during installation or operation,
do not attempt repairs of ROOTS furnished
equipment. Notify ROOTS, giving all nameplate
information plus an outline of operating conditions
and a description of the trouble. Unauthorized
attempts at equipment repair may void ROOTS
warranty.
❏
Units out of warranty may be repaired or adjusted
by the owner. It is recommended that such work be
limited to the operations described in this manual,
using ROOTS
™
parts. Good inspection and
maintenance practices should reduce the need
for repairs.
NOTE: Information in this manual is correct as of the
date of publication. ROOTS reserves the right to make
design or material changes without notice, and without
obligation to make similar changes on equipment of
prior manufacture.
For your nearest ROOTS Office, dial our Customer
Service Hot Line toll free; 1 877 363 ROOT(S) (7668)
or direct 281-966-4700.
D
O
T
HESE
T
HINGS
T
O
G
ET
T
HE
M
OST
F
ROM
Y
OUR
ROOTS
™
BLOWER
CONTENTS
I
NFORMATION
S
UMMARY
. . . . . . . . . . . 1
S
AFETY
P
RECAUTIONS
. . . . . . . . . . . . 2
O
PERATING
L
IMITATIONS
. . . . . . . . . . . 2
I
NSTALLATION
. . . . . . . . . . . . . . . . . . . 3
L
UBRICATION
. . . . . . . . . . . . . . . . . . . 6
O
PERATION
. . . . . . . . . . . . . . . . . . . . 7
O
PERATING
C
HARACTERISTICS
..............8
❏
Check shipment for damage. If found, file claim
with carrier and notify ROOTS.
❏
Unpack shipment carefully, and check contents
against Packing List. Notify ROOTS if a
shortage appears.
❏
Store in a clean, dry location until ready for
installation. Lift by methods discussed under
INSTALLATION to avoid straining or distorting the
equipment. Keep covers on all openings. Protect
against weather and corrosion if outdoor storage
is necessary.
❏
Read OPERATING LIMITATIONS and
INSTALLATION sections in this manual and plan
the complete installation.
❏
Provide for adequate safeguards against accidents
to persons working on or near the equipment during
both installation and operation. See SAFETY
PRECAUTIONS.
❏
Install all equipment correctly. Foundation design
must be adequate and piping carefully done. Use
recommended accessories for operating protection.
❏
Make sure both driving and driven equipment is
correctly lubricated before start-up.
See LUBRICATION.
❏
Read starting check points under OPERATION. Run
equipment briefly to check for installation errors and
make corrections. Follow with a trial run under
normal operating conditions.
T
ROUBLESHOOTING
. . . . . . . . . . . . . . 9
M
AINTENANCE
/R
EPLACEMENTS
UNIVERSAL RAI
®
SERIES BLOWERS
...........10
RAM
™
SERIES BLOWERS
.........................14
F
IGURES
...........................................18
T
ABLES
.............................................22
A
SSEMBLY DRAWINGS
.........................26
P
ARTS
L
IST
.......................................31
US $3.00, Canada $4.50
IRB-180-102
Rev. 12/02
U
NIVERSAL
RAI
®
& RAM
™
SERIES
Summary of Contents for UNIVERSAL RAI Series
Page 34: ...NOTES...
Page 35: ......