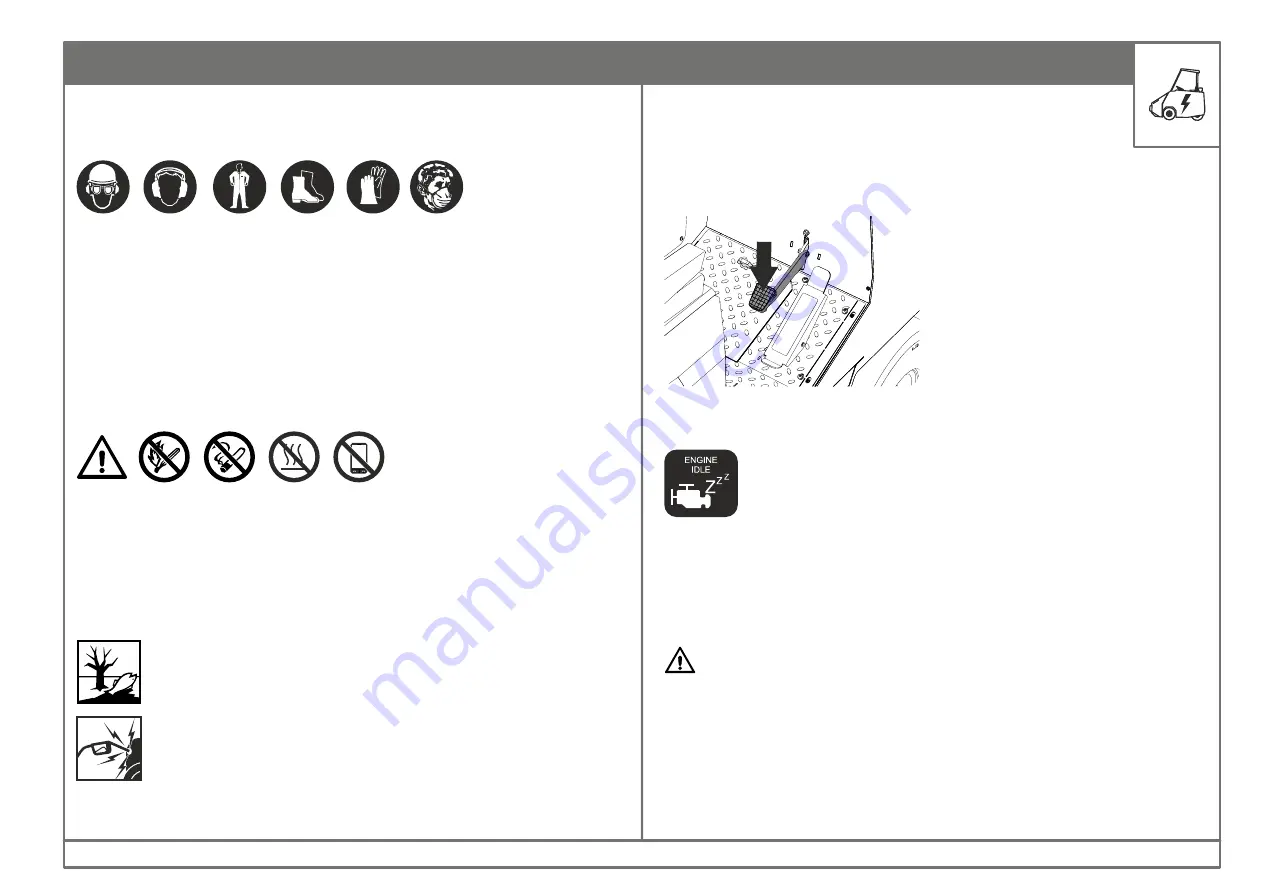
48
Rhino RD180
MACHINE OPERATION
STARTING THE MACHINE
Before star ng the machine:
WARNING:
û
DO NOT SMOKE WHILE REFUELING OR TOPPING UP FLUIDS.
û
DO NOT REFUEL OR TOP UP NEAR OPEN FLAMES/FIRE.
û
DO NOT REFUEL OR TOP UP NEAR A HOT SURFACE.
û
DO NOT USE MOBILE PHONE REFUELING OR TOPPING UP FLUIDS.
WARNING:
DO NOT LET FUEL OR OIL TO LEAK INTO THE ENVIRONMENT.
THERE IS A RISK OF CONTAMINATION!
If applicable use the above safety devices:
1. Safety Eyewear
2. Earmuff
3. Safety Reflec ng Jacket/Overalls
4. Safety Shoes
5. Safety Gloves
6. Dust Mask
1. Sit in operator seat, adjust seat posi on (if required) press parking brake,
check if the direc on control pedal is in neutral posi on.
2. Thro le should be in
idle
posi on.
3. Turn the igni on key to start posi on to start the engine.
DRIVING THE MACHINE
NOTE:
If the engine does not start after 10 seconds, release key, wait for 1
minute and repeat the procedure again.
After starting the engine wait for two minutes with engine speed set to idle
for the pneumatic system to pressurize.
WARNING: This machine emits toxic gases. Severe respiratory
damage can be caused. Provide sufficient ventilation.
Idle engine speed
Star ng:
AVOID STATIC ELECTRICITY WHEN FUELING. AVOID DEATH OR
SERIOUS INJURY FROM FIRE OR EXPLOSION.
Summary of Contents for Rhino RD180
Page 2: ...2 Rhino RD180...
Page 4: ...4 Rhino RD180 INTRODUCTION...
Page 7: ...7 Rhino RD180 TECHNICAL SPECIFICATION...
Page 10: ...10 Rhino RD180 SAFETY INSTRUCTIONS...
Page 17: ...17 Rhino RD180 KNOW YOUR MACHINE...
Page 24: ...24 Rhino RD180 WORKING PRINCIPLE...
Page 26: ...26 Rhino RD180 INITIAL SET UP...
Page 29: ...29 Rhino RD180 CONTROLS...
Page 45: ...45 Rhino RD180 MACHINE OPERATION...
Page 58: ...58 Rhino RD180 MAINTENANCE...
Page 80: ...80 Rhino RD180 TROUBLESHOOTING...
Page 84: ...84 Rhino RD180 DO S DON TS...
Page 86: ...86 Rhino RD180 OPERATOR NOTES...
Page 87: ...87 Rhino RD180...