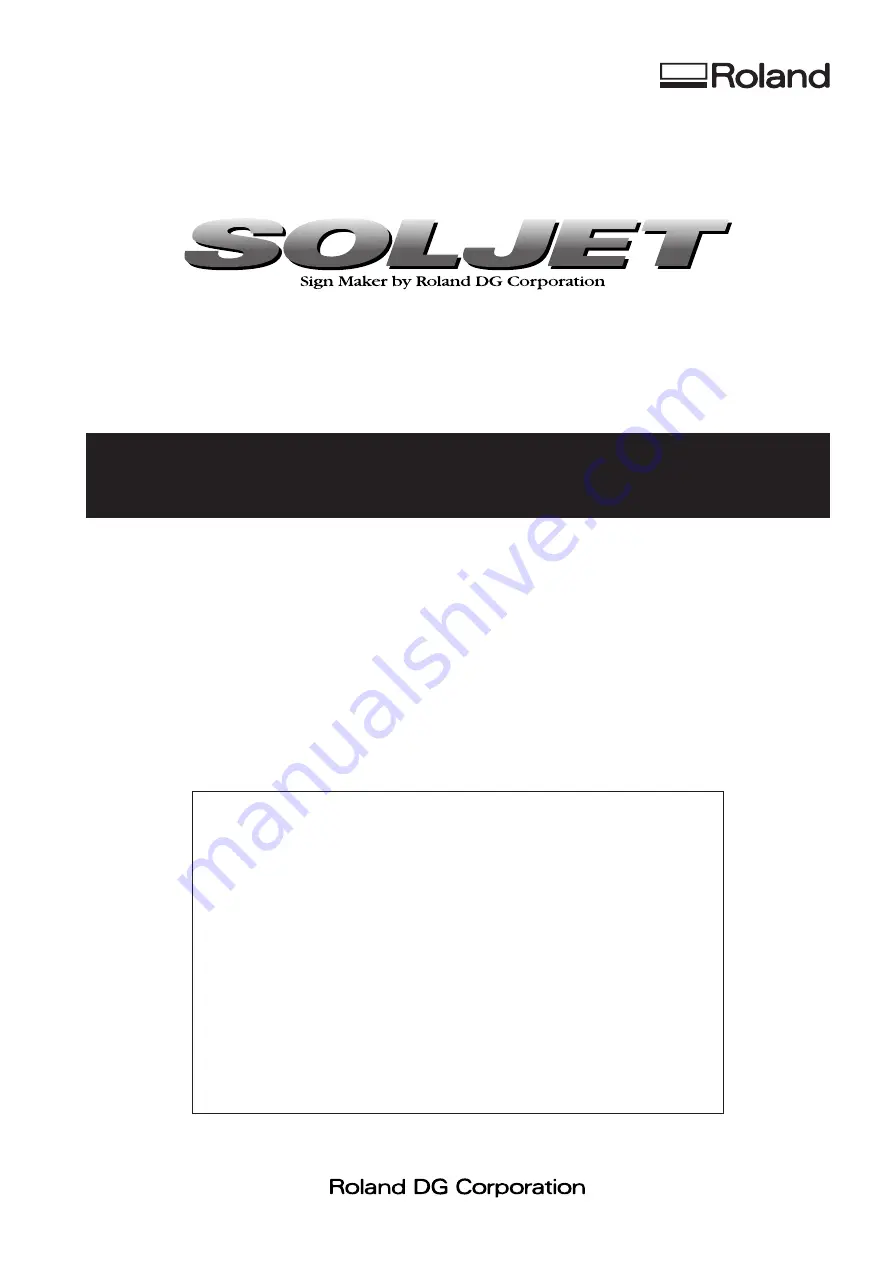
Thank you very much for purchasing this machine.
•
To ensure correct and safe usage with a full understanding of this product's perfor-
mance, please be sure to read through this manual completely and store it in a safe
location.
•
Unauthorized copying or transferral, in whole or in part, of this manual is prohibited.
•
The contents of this operation manual and the specifications of this product are
subject to change without notice.
•
The operation manual and the product have been prepared and tested as much as
possible. If you find any misprint or error, please inform us.
•
Roland DG Corp. assumes no responsibility for any direct or indirect loss or damage
which may occur through use of this product, regardless of any failure to perform on
the part of this product.
•
Roland DG Corp. assumes no responsibility for any direct or indirect loss or damage
which may occur with respect to any article made using this product.
USER'S MANUAL
SC-500
Summary of Contents for SOLJET SC-500
Page 14: ...12 MEMO...
Page 56: ...54 Maintenance MEMO...
Page 78: ...76 User s Reference MEMO...
Page 99: ...R1 011011...