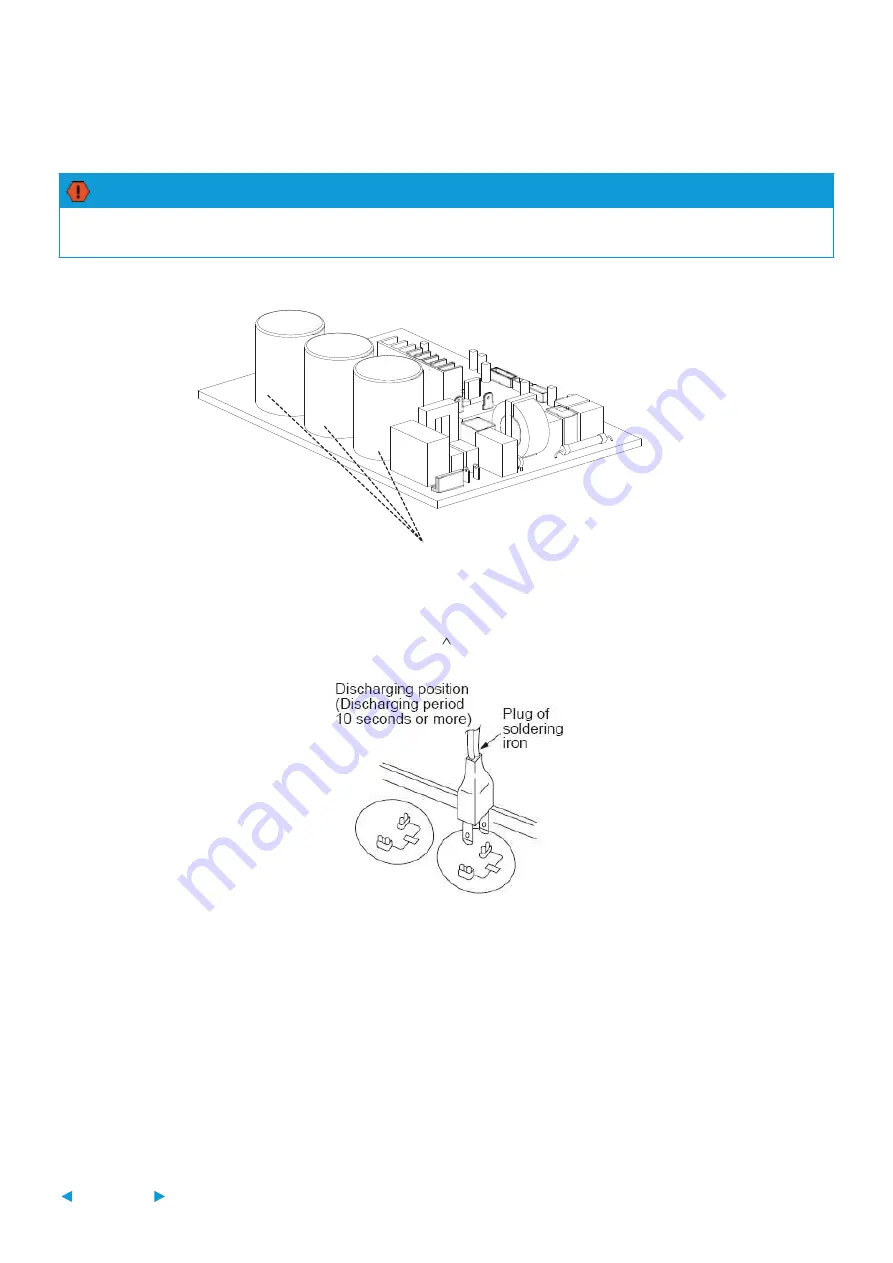
Page 58
1. Safety Cau
�
on
Electroly
�
c Capacitors
For other models, connect discharge resistance (approx.100
40W) or a soldering iron plug between the posi
�
ve a
n
d
nega
�
ve
terminals of the electroly
�
c capacitor. The terminals are located on the bo
�
om surface of the outdoor PCB.
Note: This picture is for reference only. Actual appearances may vary.
WARNING
Electricity remains in capacitors even when the power supply is o
ff
.
Ensure the capacitors are fully discharged before troubleshoo
�
ng.
Tr
o
ub
le
s
h
oo
ti
ng