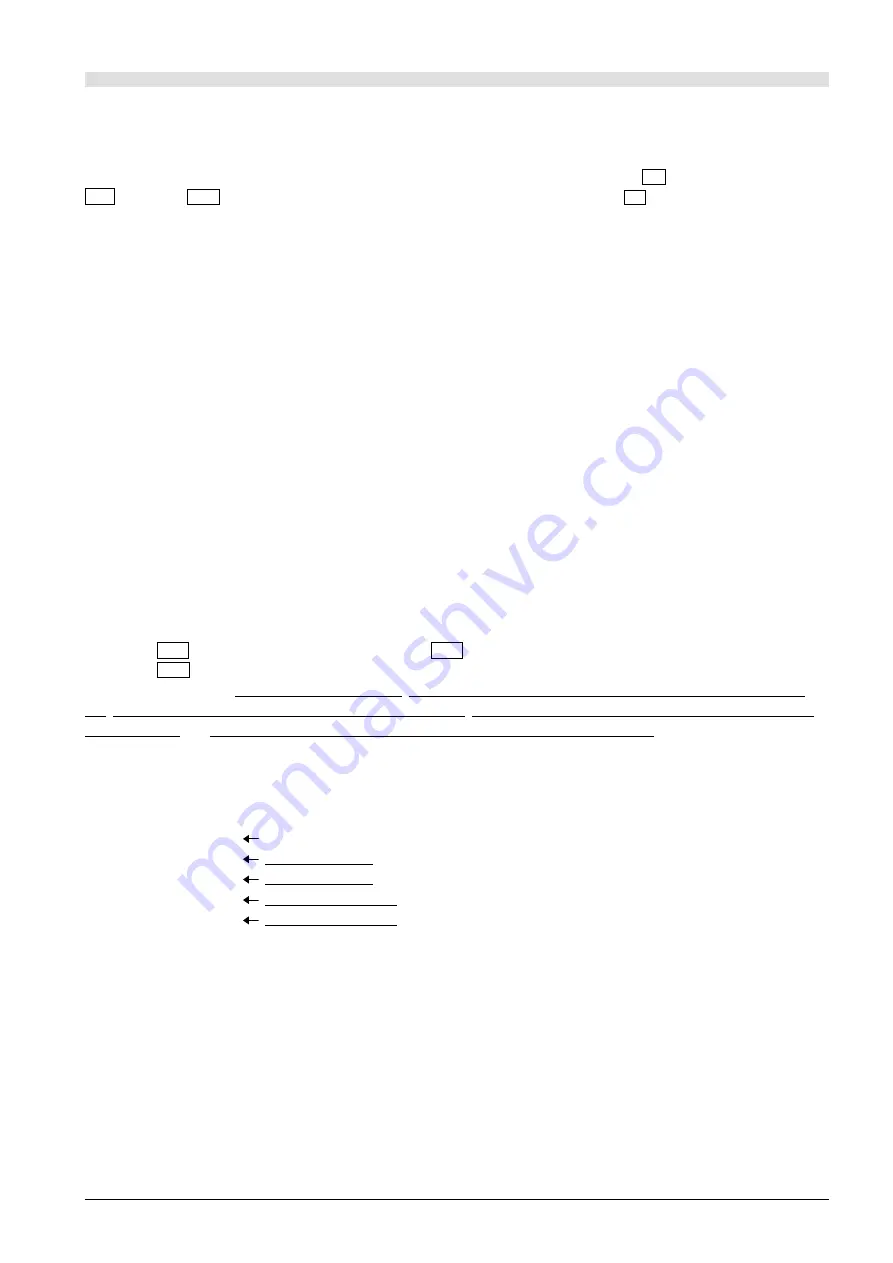
5
: A block containing only a “%” must appear at the start of the data. This notifies the machine of the start (or end) of
the data. Such a block may optionally be present at the end of the data. When it appears at the end of the data, the
data is specified automatically.
The character indicating the program start is “%” in the case of ISO or ASCII code, or “ ER ” in the case of EIA.
: The EOB (end of block) indicates the conclusion of the block. In ASCII, this is the LF (line feed) code.
: This inputs the program number. A program starts with a program number, and ends with either M02, M30, or M99.
M02 or M30 signifies the end of a main program, and M99 signals the end of a subprogram.
An integer from 0001 to 9999 can be input as the program number. Care should be taken to ensure that multiple
program numbers do not appear in a single program.
Program numbers are used to call up subprograms.
: Sequence numbers are reference numbers for the program. They have absolutely no effect on the program (machine
operation).
: This is the preparatory function. The special functions are specified by the two-digit code following the “G.”
: This indicates a coordinate value or movement distance. I, J, and K are used to specify the center coordinate of a
circle (or arc).
:For positive coordinates or movement directions, it is not necessary to prefix a “+” to the value.
: This determines the feed rate.
: This determines the speed of the spindle motor.
: This is a miscellaneous function. It is used for such operations as starting and stopping the spindle motor.
: This signals the end of the program. The spindle stops.
%
EOB
O
N
G
X(I)
Y(J)
Z(K)
F
S
M
M02
About Blocks
A program is a series of instructions (written commands) for the machine, expressed as symbols and numbers. The instructions are
separated by EOB markers, with the information between two EOB markers making up one instruction. This single instruction
between two EOB markers is called a “block.” Each block, in turn, is composed of “words.”
The types of words include those valid only within a block, those also valid outside of blocks until a word of the same group is speci-
fied, those which activate a function immediately after being specified, those which activate a function at the end of the block in which
they are specified, and those which activate a function at the start of the block in which they are specified. Programming requires
knowledge of the characteristics of each word. See "APPENDICES-Words Table" or a chart of word characteristics.
<Examples of “words also valid outside of blocks until a word of the same group is specified”>
Indicates that the specified coordinate value is absolute (G90)
Linear interpolation from the current tool position to X = 100, Y = 100
(G01)
Linear interpolation from the tool position moved to by N02 to Z = -20
Movement (positioning) from the tool position moved to by N03 to Z = 20 (G00)
Movement (positioning) from the tool position moved to by N03 to X = 0, Y = 0.
%
N01 G90
N02 G01X100Y100
N03 Z-20
N04 G00Z20
N05 X0Y0