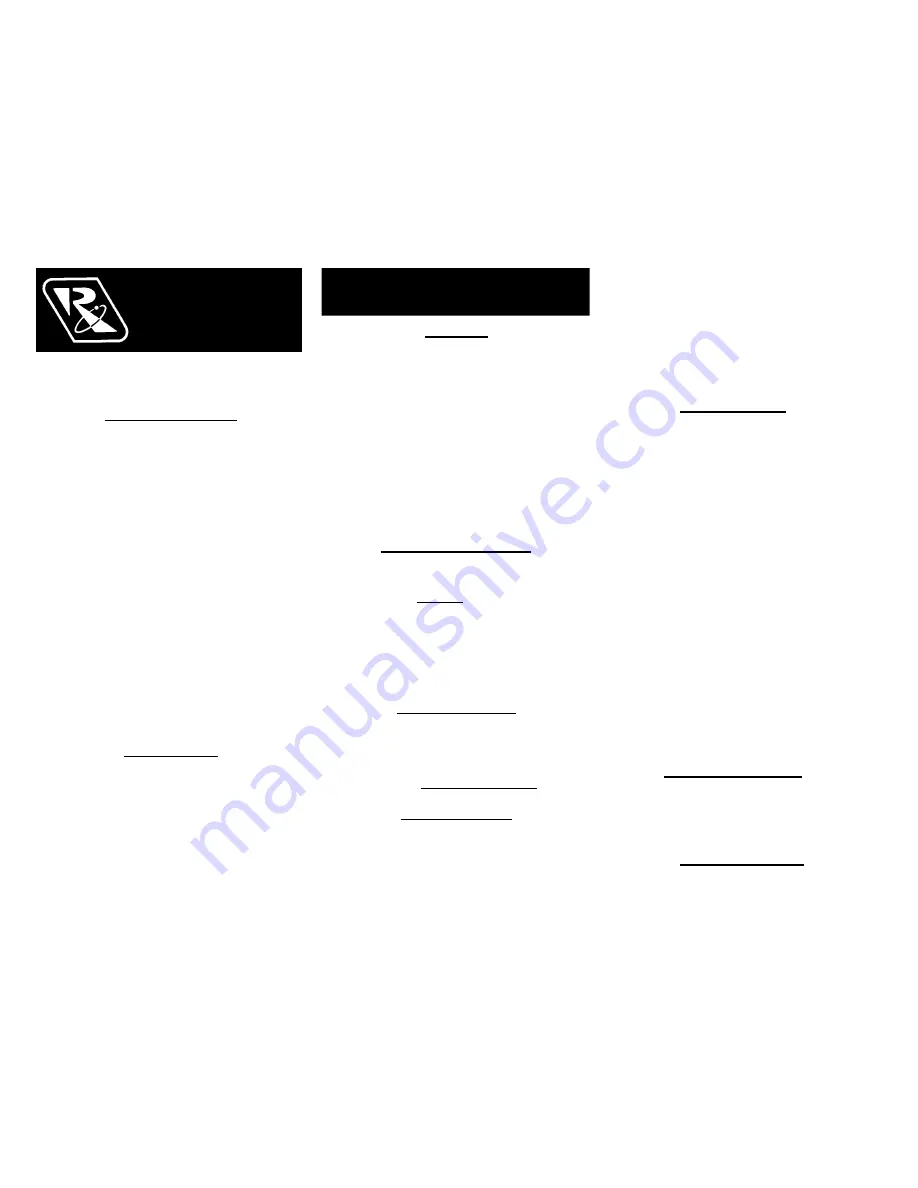
Auto Tune
Series of
Variable Frequency controls
General Description
The Auto Tune
Series of variable frequency feeder
controls are ideal for vibratory bowls, storage
hoppers and linear inline feeders. The VF Series
output frequency can be adjusted to match the
natural frequency of the vibratory feeder. The
amplitude sets the amount of vibration. The CFR
vibration sensor allows the control to Auto Tune
to
the optimum feeding frequency. The CFR sensor
also regulates the vibration level. A feeder operating
at its resonant frequency will perform efficiently using
less power and provide better feeding performance.
Standard features include an easy to read backlit
display, easy to understand status messages and
simple to navigate set-up menu. Resonant
frequency can be found manually using the keypad
or automatically by mounting the optional vibration
sensor, P/N 123-215, letting the controller scan the
frequency range. The vibration sensor also provides
feedback to help maintain a constant parts feed rate.
Other features include a parts sensor input, an
interlock output, enable input, soft-start adjustment,
line voltage compensation, 4-20mA amplitude
control, and lockable menu.
Control Sizing
A VF control should be sized according to the
amperage needed to operate a full vibratory feeder.
If the amps is unknown, use the following guidelines.
Most hoppers and linear inline feeders can be
powered by a VF-3 control. Typical two coil feeder
bowls can be driven by a VF-9 control. Two coil
bowls with outside tooling that require a high feed
rate should be connected to a VF-12 control. Three
coil bowls should use a VF-12 control. Four coil
bowls should use a VF-18 control.
©
2005, 2017 RODIX
INC
.
Mounting
The VF-3, VF-9 and VF-18 controls may be mounted
vertically or horizontally, but the VF-3 and VF-9
controls stay cooler when mounted vertically. Mount
the control to a metal plate or mount it so that the
back of the heat sink is fully exposed to the air.
Important: The heat sink fins of the VF-12 power
control must be mounted vertically with three
inches of space above and below the heat sink
for proper cooling.
The VF-18 control and heat sink are cooled by a fan.
Mount the heat sink of the VF-18 control flat against
a metal plate in order to ensure the fan’s air flow
through the heat sink.
Electrical Connections
Make the electrical connections prior to turning the
control on. Once connections are made, any desired
changes to the software settings can be made with
the cover closed.
Warning
:
Shock Hazard! Do not
operate control with cover open.
Safety codes require single phase 120 or 240 VAC
installations to bypass the phase 2 fuse, L2.
To
bypass, remove the wire connecting TB1-L2 to the L2
fuse holder. Remove the terminal end of the wire
connecting the L2 fuse to the power switch and
connect it to TB1-L2.
1. Parts Sensor Input
(Photo-sensor or Proximity Switch)
Connect a three wire, current-sourcing (PNP) or
current-sinking (NPN) sensor to TB2 as shown on the
enclosed wiring diagram. The sensor must be able
to operate on 12VDC and be capable of switching at
least 3.0 mA. See Parts Sensor Settings section for
more operation information.
2. Run Input Enable
A Run Jumper comes installed from the factory as
shown on the enclosed wiring diagram.
If the run input is to be controlled by a relay contact,
switch, or other device, replace the factory-installed
jumper (see TB2 of the wiring diagram) with the
contact device. The contact must be able to switch
12VDC at 3.0 mA. The control will then run only
when the contact is closed and the part sensor is
calling for parts. The right column of the display
shows the run status with “R= 1” or “R= 0.”
If the run input will be controlled by a current sourcing
PLC output, use the “Sig” and “-“ terminals (see TB2
on the wiring diagram).
For the High/Low parts sensing mode, a second parts
sensor (PNP type only) connects to the run input in
place of the run jumper.
3. Auxiliary Output
The right column of the display shows the status of
the Aux output, “A=1” or “A=0.” The Feeder
Bowl/Hopper Interlock “+” and “sig” (see TB2 on the
wiring diagram) can be connected to a Rodix FC-40
Plus
All-Purpose Series control (TB2-11 & 12) when
control of a bulk material hopper is needed. The
control interlock will prevent the hopper from
operating anytime the bowl is turned “OFF” or in
"STAND BY" mode. The Interlock output is capable
of switching 12 VDC at 85 mA. The Interlock output
can also be used to drive a solid state relay that can
operate auxiliary equipment such as air valves. See
Figure 2 on the wiring diagram. One VF series
control can be interlocked to another. The aux output
of the master control connects to the run input of the
subordinate. To monitor the AUX output with a PLC,
see Figure 3.
A 1 Watt (or less) 12VDC air solenoid or a relay can
be driven by the Aux output. Note: a diode (1N4006)
must be placed across the solenoid in the reverse
polarity to adsorb the energy when the solenoid is de-
energized. The “bar” side of the diode connects to
TB2 “+” and the “solid colored” side connects to TB2
“SIG.” Failure to use a diode in reverse polarity voids
the warranty.
4. Internal Power Supply
At the rated line voltage, the line isolated power
supply is capable of providing a combined total
current of 150 mA at 12 VDC. The total current
includes the parts sensor, auxiliary output
accessories, and CFR sensor.
5. Power Connections
The control can operate on a power line from 85 to
264VAC. The plug can be connected to a standard
North American receptacle (NEMA 5-15R).
6/6/2017 Page 3
ADJUSTMENTS & SET UP
RODIX INC.
AUTO TUNE
FEEDER CUBE
VF Series