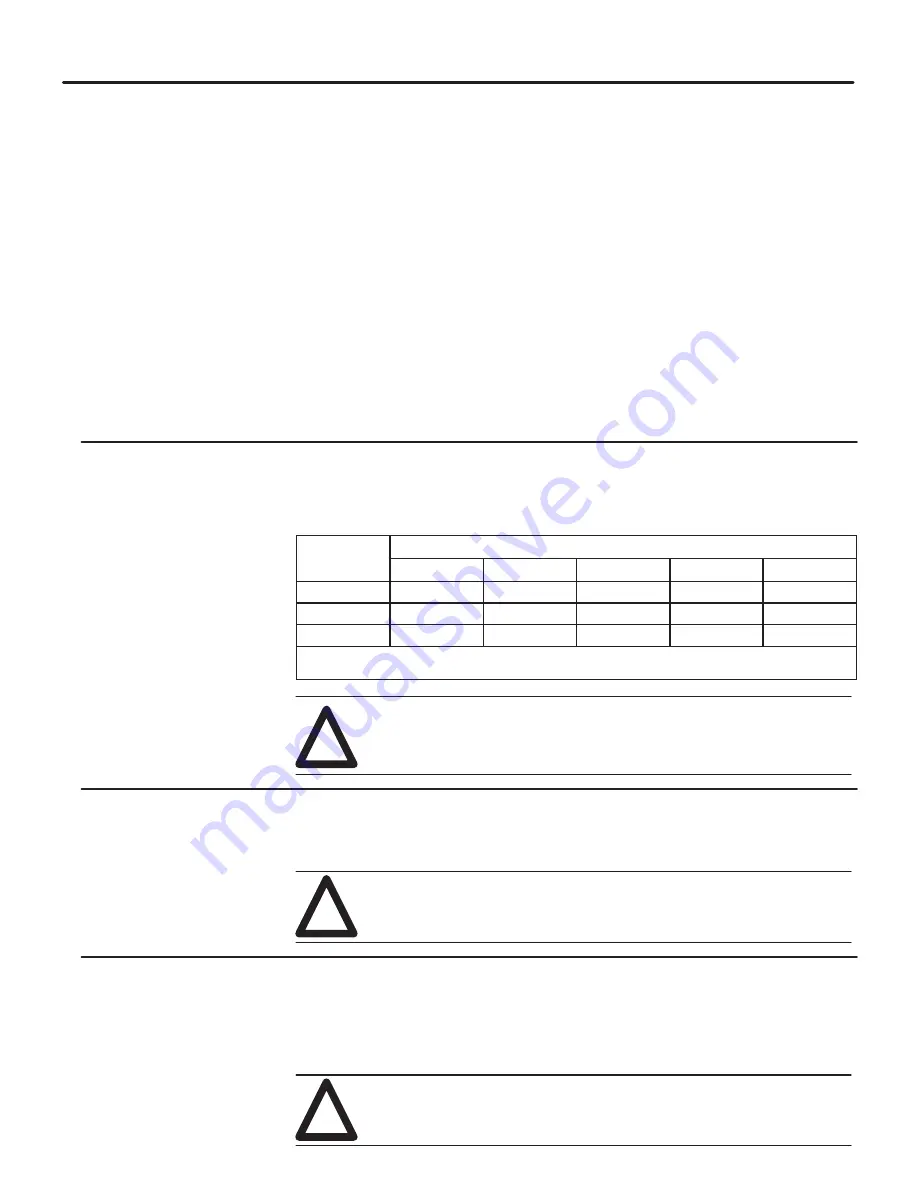
Chapter
Installation & Wiring
2
2-7
The controller can be installed on a system with power factor correction capacitors.
The capacitors must be located on the line side of the controller. This must be done
to prevent damage to the SCRs in the SMC PLUS controller.
When discharged, a capacitor has essentially zero impedance. For switching
sufficient impedance should be connected in series with the capacitor bank to limit
the inrush current. A method of limiting the surge current is to add inductance in
the capacitance conductors. This can be accomplished by putting turns or coils in
the power connections to the capacitors.
480 – 600 volts – 6 inch diameter coil, 8 loops
250 volts – 6
inch diameter coil, 6 loops
Care should be used in mounting the coils so that they are not stacked directly on
top of each other or they will have a canceling effect. Also, the coils should be
mounted on insulated supports away from metal parts so they will not act like
induction heaters.
If an isolation contactor is used, put capacitors in front of contactor.
Fast acting current-limiting fuses are coordinated with the SCRs for protection of
the SCRs in the event of short circuits in the load. Refer to Figure 2.13 below for
recommended fuses.
Figure 2.13 - Fast Acting Current-limiting Fuses
Fuse
SMC PLUS Rating
Fuse
Manufacturer
150-A24
150-A35
150-A54
150-A97
150-A135
Shawmut
A70P70
A70P100
A70P200
A70P300
A70P300
Buss
SPP-4F60
SPP-4F100
SPP-4F150
SPP-4F300
SPP-4F300
Brush
XL70F080
XL70F125
XL70F200
XL70F300
XL70F300
NOTES:
1.
Fuse numbers are fuse manufacturers’ catalog number
2.
Fuse size listed is for 230, 460 or 575 volt.
CAUTION:
The fast acting current-limiting fuses specified in the
above table do not provide branch circuit protection. Branch circuit
protection in accordance with applicable electrical codes is required
even though fast acting current-limiting fuses are used.
!
Thermal motor overload protection is not provided unless specified with
non-combination controller. It can be separately provided. The overload trip time
should be greater than the acceleration time to avoid nuisance tripping.
CAUTION:
Overload relays should be properly coordinated with the
motor.
!
A protective module containing metal oxide varistors (MOVs) and capacitors can be
installed to protect the power components from electrical transients and/or high
electrical noise. The protective modules clip transients generated on the lines and
prevent such surges from damaging the SCRs. The capacitors in the protective
modules are used to shunt noise energy away from the controller electronics.
WARNING:
When installing or inspecting the protective module,
make sure the controller has been disconnected from the power source.
The protective module must be checked periodically for damage.
Inspect for damage or discoloration. Replace if necessary.
!
Power Factor
Capacitors
Fast Acting
Current-limiting
Fuses
Motor Overload
Protection
Protective Module
(optional)
Summary of Contents for Allen-Bradley SMC-PLUS Bulletin 150
Page 2: ......