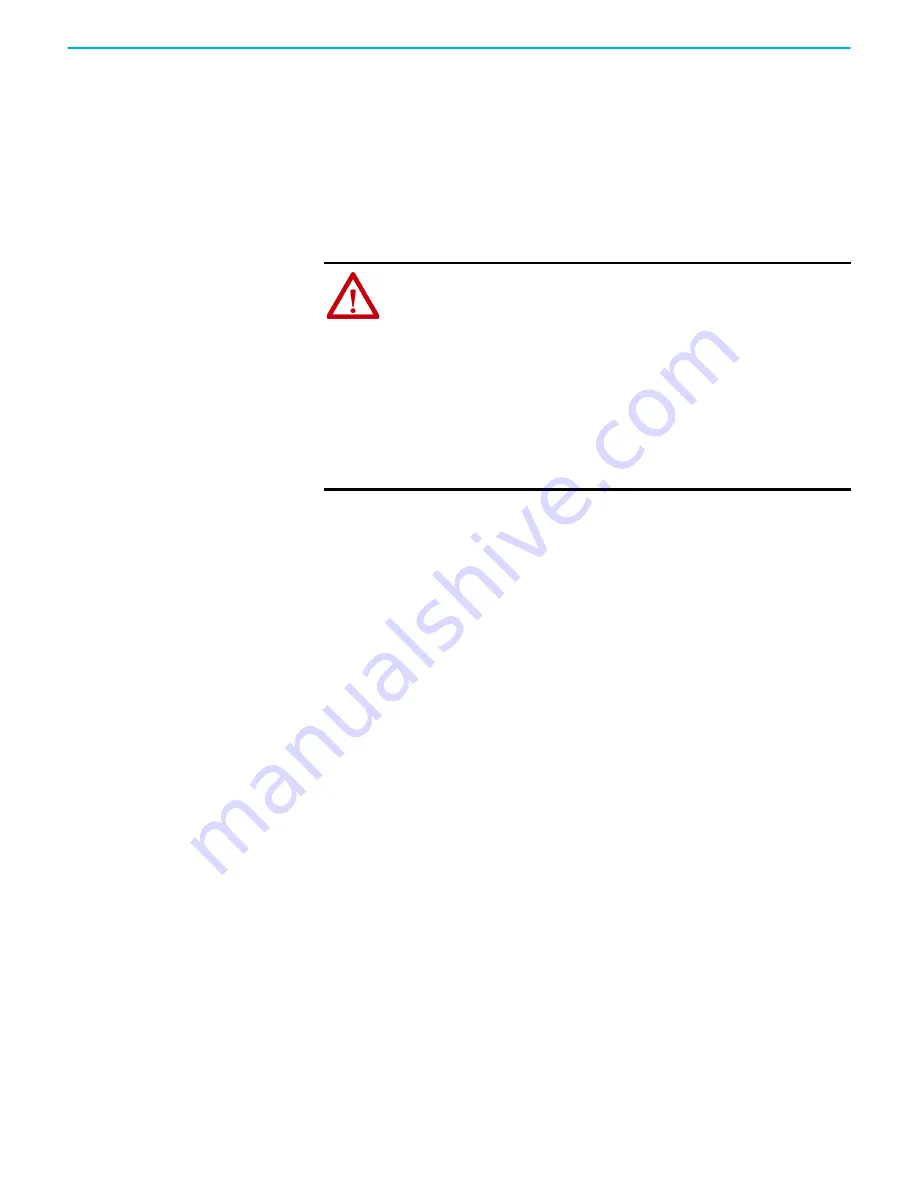
Rockwell Automation Publication 520-UM001K-EN-E - August 2021
239
Appendix G Safe Torque Off Function
Using PowerFlex 525 Safe-
Torque-Off
The PowerFlex 525 Safe-Torque-Off function is intended to be part of the
safety related control system of a machine. Before use, a risk assessment
should be performed that compares the PowerFlex 525 Safe-Torque-Off
function specifications and all foreseeable operational and environmental
characteristics of the machine to which it is to be fitted.
A safety analysis of the machine section controlled by the drive is required to
determine how often the safety function should be tested for proper operation
during the life of the machine.
Safety Concept
The PowerFlex 525 Safe-Torque-Off function is suitable for use in safety
applications up to and including Category 3 / PL(d) according to EN ISO 13849-
1 and SIL 2 according to EN 62061 / EN 61800-5-2 / IEC 61508.
In addition, the PowerFlex 525 STO may be used together with other
components in a safety application to achieve an overall Category 3 / PL(e)
according to EN ISO 13849-1 and SIL 3 according to EN 62061 and IEC 61508.
This is illustrated in Example 3 in this appendix.
Safety requirements are based on the standards current at the time of
certification.
The PowerFlex 525 Safe-Torque-Off function is intended for use in safety-
related applications where the de-energized state is considered to be the safe
state. All of the examples in this manual are based on achieving de-
energization as the safe state for typical Machine Safety and Emergency
Shutdown (ESD) systems.
Important Safety Considerations
The system user is responsible for:
•
the set-up, safety rating, and validation of any sensors or actuators
connected to the system.
•
completing a system-level risk assessment and reassessing the system
any time a change is made.
•
certification of the system to the desired safety performance level.
•
project management and proof testing.
ATTENTION:
The following information is merely a guide for proper
installation. Rockwell Automation cannot assume responsibility for the
compliance or the noncompliance to any code, national, local or otherwise
for the proper installation of this equipment. A hazard of personal injury
and/or equipment damage exists if codes are ignored during installation.
ATTENTION:
In safe-off mode, hazardous voltages may still be present at
the motor. To avoid an electric shock hazard, disconnect power to the
motor and verify that the voltage is zero before performing any work on the
motor.
ATTENTION:
In the event of the failure of two output IGBTs in the drive,
when the PowerFlex 525 Safe-Torque-Off has controlled the drive outputs
to the off state, the drive may provide energy for up to 180° of rotation in a 2-
pole motor before torque production in the motor ceases.
Summary of Contents for Allen-Bradley PowerFlex 520 Series
Page 8: ...8 Rockwell Automation Publication 520 UM001K EN E August 2021 Table of Contents Notes ...
Page 68: ...68 Rockwell Automation Publication 520 UM001K EN E August 2021 Chapter 2 Start Up Notes ...
Page 236: ...236 Rockwell Automation Publication 520 UM001K EN E August 2021 Appendix F PID Set Up Notes ...
Page 270: ...270 Rockwell Automation Publication 520 UM001K EN E August 2021 Index Notes ...