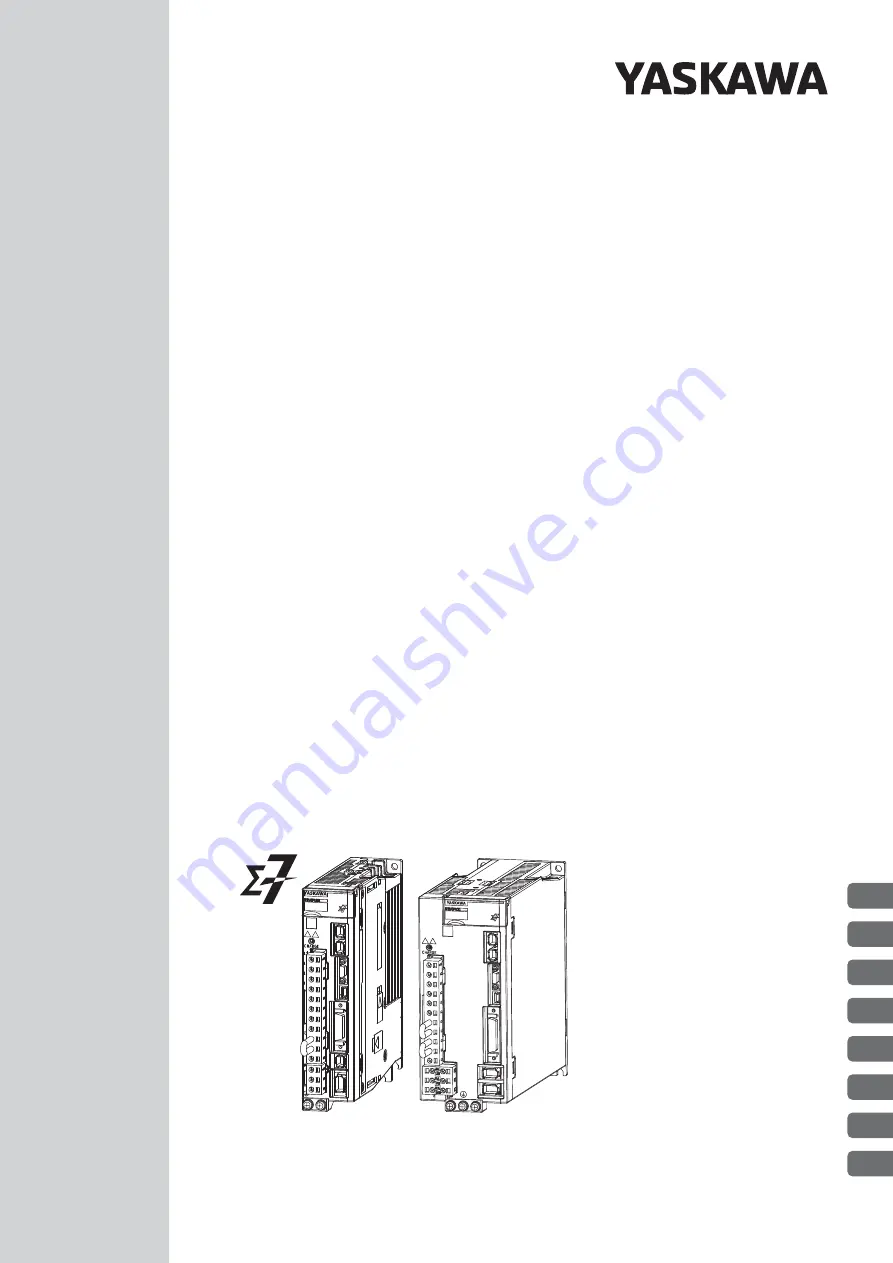
-7S/
-7W SERVOPACK with
Hardware Option Specifications
Dynamic Brake
-7-Series AC Servo Drive
Product Manual
MANUAL NO. SIEP S800001 73E
1
2
3
4
5
6
7
8
Basic Information on SERVOPACKs
Selecting a SERVOPACK
Selecting a Dynamic Brake Resistor
Maintenance
Parameter Lists
Appendices
Basic Functions That Require
Setting before Operation
Wiring and Connecting
a Dynamic Brake Resistor
SGD7S-
020
SGD7W-
020