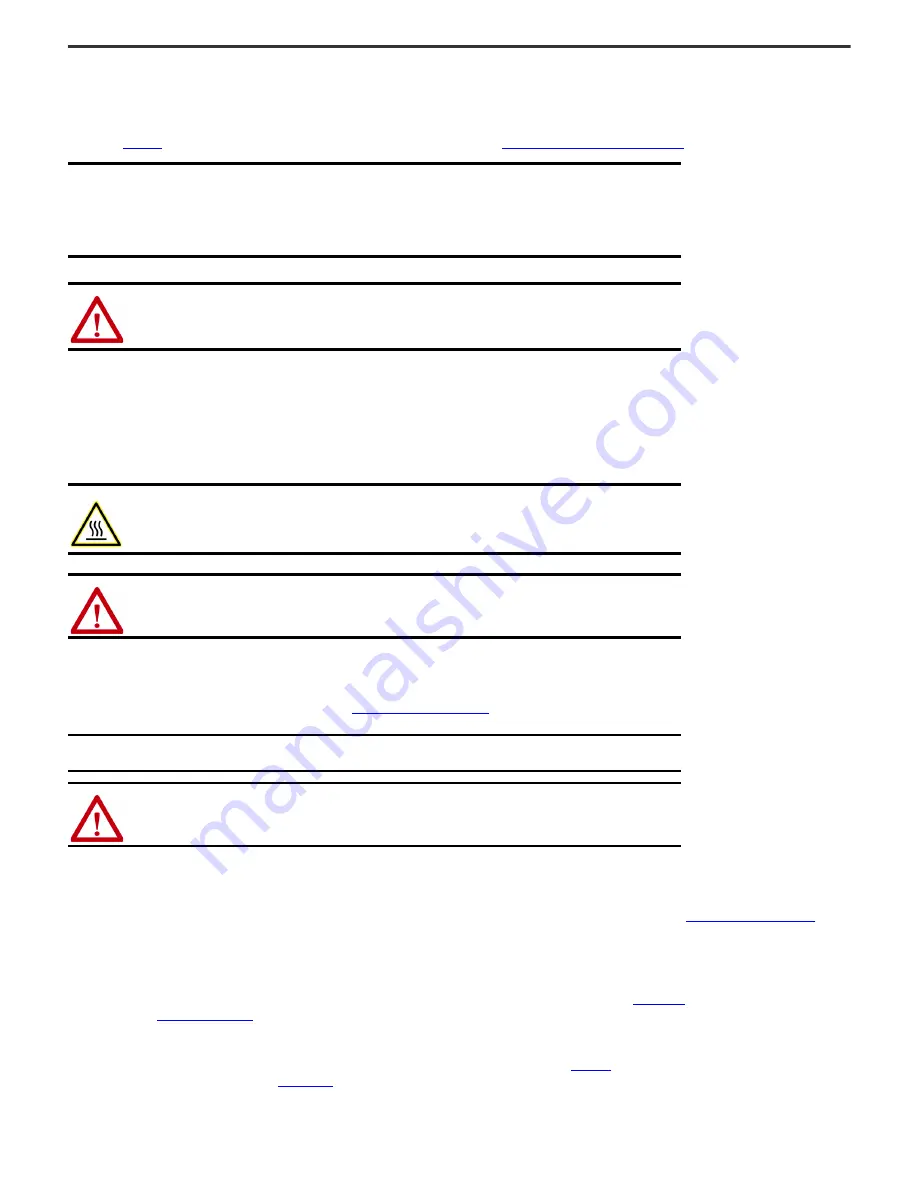
Rockwell Automation Publication MM-IN001B-EN-P - February 2022
13
Kinetix MMA Asynchronous Main Motors Installation Instructions
Cable and Connector Descriptions
Knowledgeable cable routing and careful cable construction improves system electromagnetic compatibility (EMC). Follow local standard cable practices regarding wire
size, technology, bundling, open-tray installation, NEC code, and other guidelines. American Standards, Configurations, and Ratings: Introduction to Motor Circuit Design
publication,
could be used as an additional reference. See the Knowledgebase article:
Kinetix MMA Frequently Asked Questions
, for additional information.
To install the motor and blower power cables, observe these guidelines:
•
Keep the cable lengths as short as possible.
•
Ground the cable shields to help prevent EMI from affecting other equipment.
•
Route signal cables away from motor and power wiring.
•
Separate cables by 0.3 m (1 ft) minimum for every 9 m (30 ft) of parallel run.
•
Ground both ends of the cable shield and twist the signal wire pairs to help prevent electromagnetic interference from other equipment.
Motor Power and Brake Cables
The customer must supply motor power, brake, and accessory cables for the Kinetix MMA Asynchronous Main Motors. It is the responsibility of the customer to properly
ground and terminate all connections in the terminal box. See
for additional information on accessory terminations.
Motor Feedback Connector and Cable
The Kinetix 2090 feedback cables are required with all Kinetix MMA Asynchronous Main Motors. In the catalog description, MMA
-xxxxxxx-
xx
xxxxxxxxxxx
, the
xx
indicates the
feedback type. These designators indicate if the encoder is incremental or absolute, single-turn or multi-turn, or is SIL 2 rated. See the
for
more information.
For Kinetix 5700 and Kinetix 7000 drives, existing 2090-CFBM7DF-C
x
Axxx feedback cables can be used to connect to the Kinetix MMA main motor. The 2090-CFBM7DF-
CDAFxx feedback cable has the extra wire to manage the PT1000 thermistor signal. The 2090-CFBM7DF-CEAxxx feedback cable is also available, but does not support the
PT1000 signal or the L2, S3, S4, M3, or M4 feedback types. See the Kinetix Rotary and Linear Motion Accessories, publication
specifications. See
for publications specific to your drive application.
For PowerFlex 750-series drives, the 2090-CFBM7DF-CFAFxx continuous-flex flying-lead feedback cable is designed to connect directly to the PowerFlex 750-series control
board. See PowerFlex 750-Series I/O, Feedback, and Power Option Module Installation Instructions, publication
and Kinetix 2090 Feedback Cable for Kinetix Motors
with PowerFlex 750-Series Drives, publication
, for additional information.
IMPORTANT
The following factors must be considered when bulk cable is selected:
• Power cables must be rated to voltage higher than the system voltages at all operating conditions.
• Cable conductor current carrying capacity (after all applicable deratings) must be greater than or equal to
the connected motor continuous rated current.
• Cables must meet all local and global regulatory requirements.
• Cable must have an overall shield to meet the applicable electromagnetic radiation/emission requirements.
ATTENTION:
The overall shield on all motor and blower power cables must be properly grounded. The encoder data
signal is transmitted through an impedance-matched twisted-wire pair that requires effective shielding for
optimum performance. Be sure that there is an effective connection between the cable shields and the drive
system ground.
BURN HAZARD:
Outer surfaces of the motor can reach a high temperature during motor operation. Take
precautions to help prevent accidental contact with hot surfaces. Consider motor surface temperature when you
select motor connectors and cables. Failure to observe these safety procedures could result in personal injury or
damage to equipment.
ATTENTION:
High voltage can be present on the shields of the motor cables if the shields are not grounded. Verify
that there is a connection to ground for all shields in the motor cables.
IMPORTANT
The recommended wire size is based on motor current requirements and terminal board sizing. Consult
your local electrical code before you select a wire gauge for your application.
ATTENTION:
Unshielded power connections should not extend beyond the terminal board. Failure to observe these
safety procedures could result in damage to the motor, cables, and connector components.