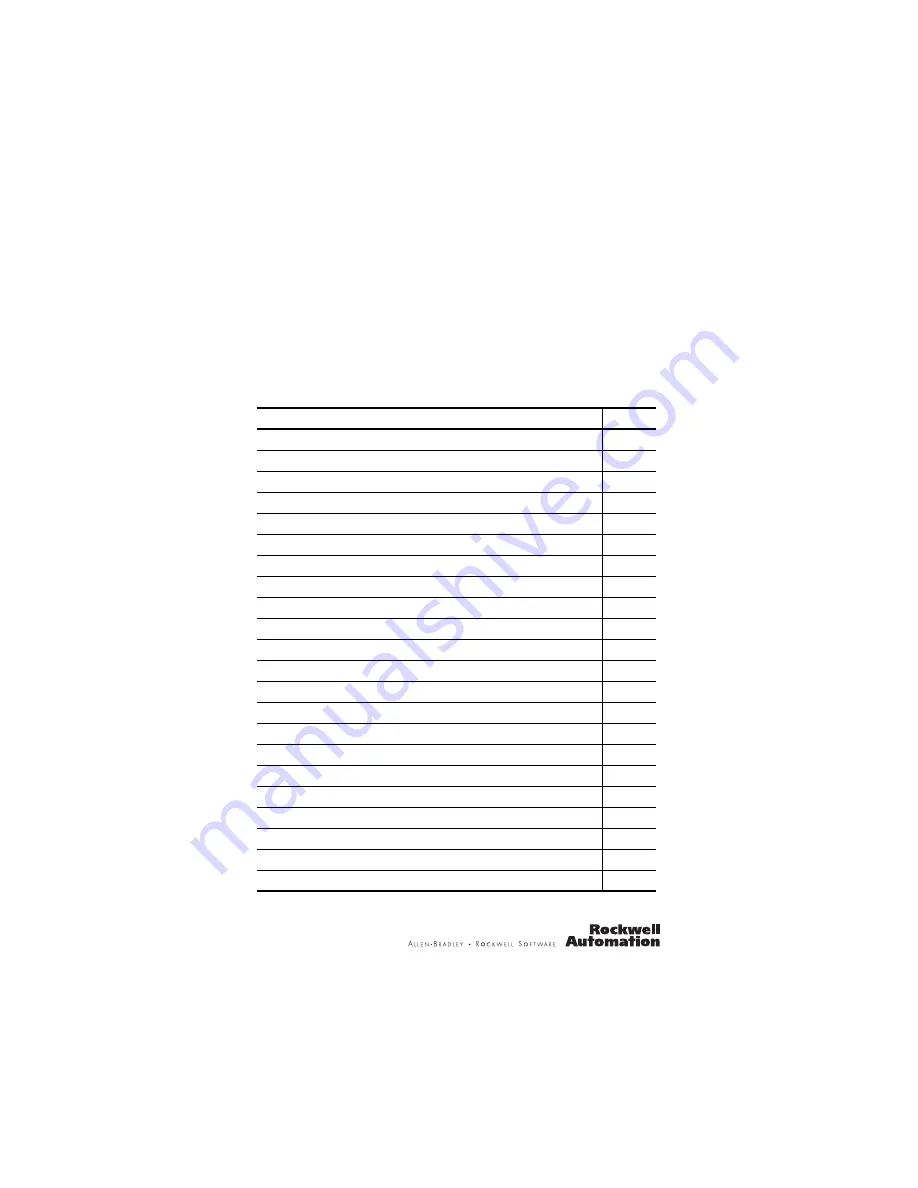
Installation Instructions
CompactLogix Controller
Catalog Numbers 1769-L32E, 1769-L35E
Topic
Page
North American Hazardous Location Approval
European Hazardous Location Approval
Install a 1784-CF64 or 1784-CF128 CompactFlash Card (optional)
Make RS-232 Connections to the Controller
Make Ethernet Connections to the Controller
Select the Controller’s Operating Mode
RS-232 Serial Port Status Indicators (Channel 0)