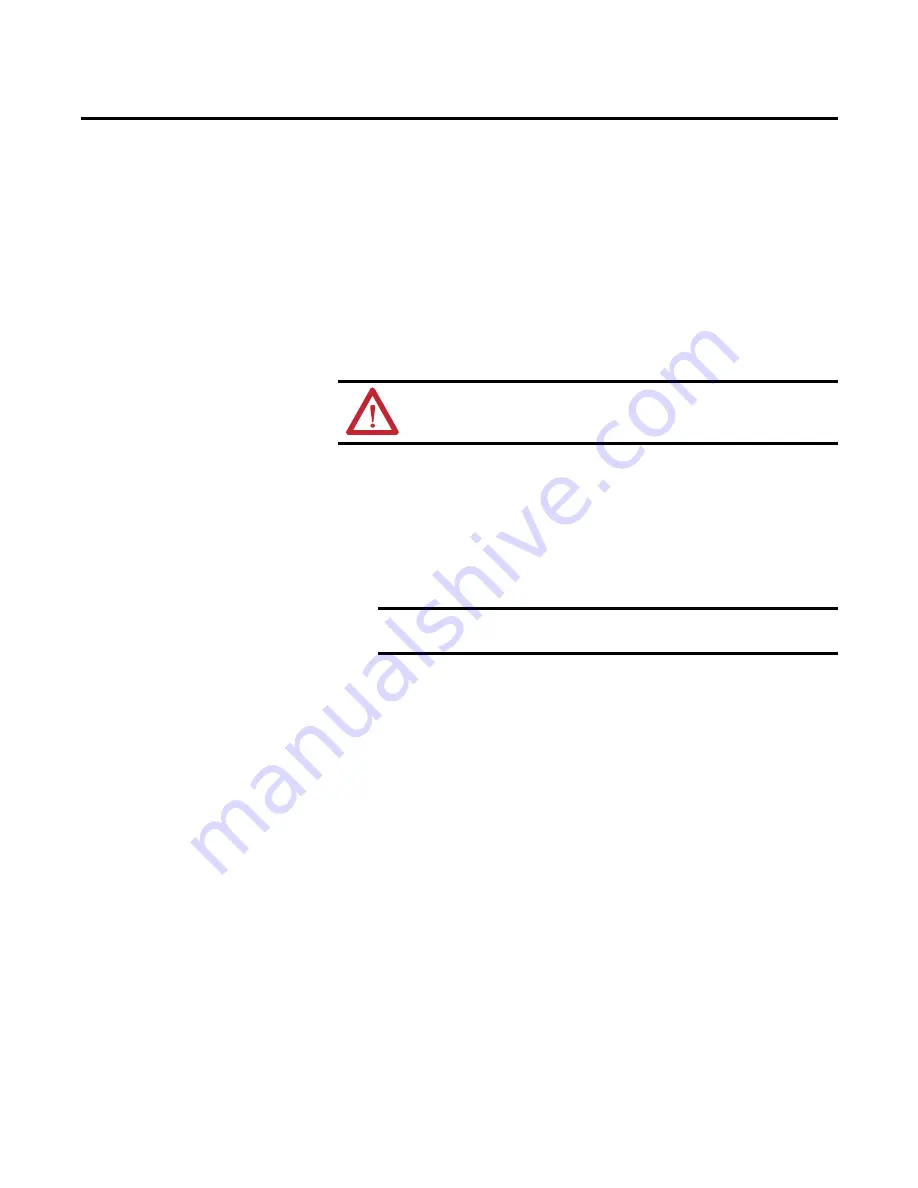
Rockwell Automation Publication 2100-IN012D-EN-P - September 2010
89
Chapter
9
Maintenance
Establish a periodic maintenance program for MCCs to avoid unnecessary
downtime. The frequency of service to the MCC will depend upon the
equipment usage and the environment in which it operates. The following is a
suggested checklist and can be used to establish a maintenance program.
Maintain the MCC
1.
Inspect the MCCs once per year or per established maintenance program.
2.
Carefully inspect doors and enclosure sides for evidence of excessive heat.
3.
Check for moisture or any signs of dampness or drippings inside the
MCC.
a. Seal off conduit, cracks, and openings that have allowed and/or could
allow moisture to enter the MCC enclosure.
b. Dry or replace and clean insulating material that is damp or wet or
shows signs of moisture.
c. Check devices such as contactors, circuit breakers, disconnect switches,
relays, and push buttons for wetness or signs of moisture, corrosion, or
contamination.
d. Replace damaged or malfunctioning parts.
4.
Check the integrity of bus splice connections.
Bus splices can be easily identified by the label on the interior of the vertical
wireway door or on the interior right-hand side plate of frame mounted
units. Recommended torque values can be found on the information label
on the interior of the vertical wireway door or on the interior right-hand
side plate of frame mounted units.
The factory-made power bus connections are tightened by a computer-
controlled torquing system. The following connections do not require re-
torquing, vertical to horizontal bus connections and power conductor to
horizontal bus connections. These factory-made connections do not
require servicing for the life of the MCC.
ATTENTION:
De-energize the MCC before servicing.
IMPORTANT
Condensation in conduit or dripping from an outside source is a
common cause of MCC failure. Eliminate any source of moisture.