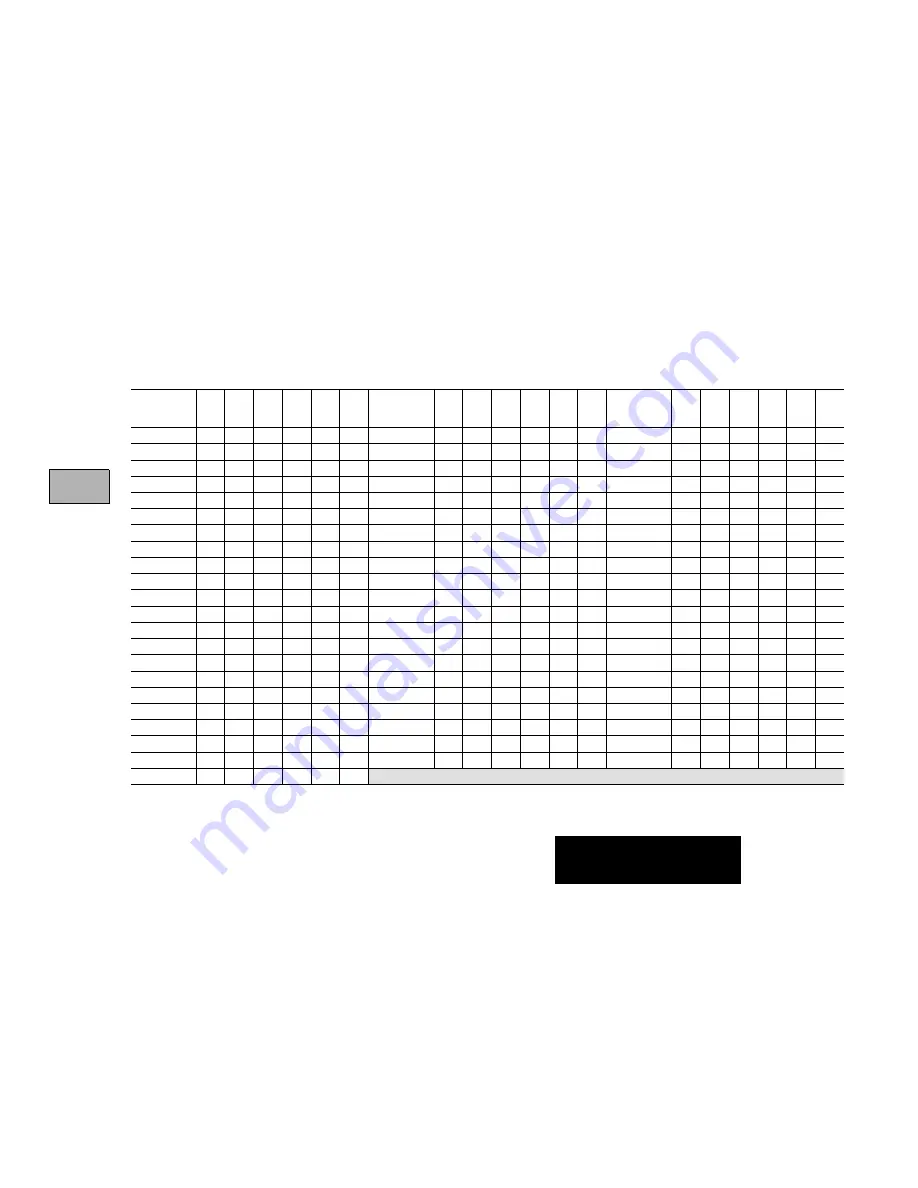
Switch Settings
4-13
Classic PLC-5
processors only
Station
Number
1
2
3
4
5
6
Station
Number
1
2
3
4
5
6
Station
Number
1
2
3
4
5
6
0
on
on
on
on
on
on
26
on
off
off
on
off
on
53
off
off
on
off
on
off
1
off
on
on
on
on
on
27
off
off
off
on
off
on
54
on
on
off
off
on
off
2
on
off
on
on
on
on
30
on
on
on
off
off
on
55
off
on
off
off
on
off
3
off
off
on
on
on
on
31
off
on
on
off
off
on
56
on
off
off
off
on
off
4
on
on
off
on
on
on
32
on
off
on
off
off
on
57
off
off
off
off
on
off
5
off
on
off
on
on
on
33
off
off
on
off
off
on
60
on
on
on
on
off
off
6
on
off
off
on
on
on
34
on
on
off
off
off
on
61
off
on
on
on
off
off
7
off
off
off
on
on
on
35
off
on
off
off
off
on
62
on
off
on
on
off
off
10
on
on
on
off
on
on
36
on
off
off
off
off
on
63
off
off
on
on
off
off
11
off
on
on
off
on
on
37
off
off
off
off
off
on
64
on
on
off
on
off
off
12
on
off
on
off
on
on
40
on
on
on
on
on
off
65
off
on
off
on
off
off
13
off
off
on
off
on
on
41
off
on
on
on
on
off
66
on
off
off
on
off
off
14
on
on
off
off
on
on
42
on
off
on
on
on
off
67
off
off
off
on
off
off
15
off
on
off
off
on
on
43
off
off
on
on
on
off
70
on
on
on
off
off
off
16
on
off
off
off
on
on
44
on
on
off
on
on
off
71
off
on
on
off
off
off
17
off
off
off
off
on
on
45
off
on
off
on
on
off
72
on
off
on
off
off
off
20
on
on
on
on
off
on
46
on
off
off
on
on
off
73
off
off
on
off
off
off
21
off
on
on
on
off
on
47
off
off
off
on
on
off
74
on
on
off
off
off
off
22
on
off
on
on
off
on
50
on
on
on
off
on
off
75
off
on
off
off
off
off
23
off
off
on
on
off
on
51
off
on
on
off
on
off
76
on
off
off
off
off
off
24
on
on
off
on
off
on
52
on
off
on
off
on
off
77
off
off
off
off
off
off
25
off
on
off
on
off
on
on = closed
off = open