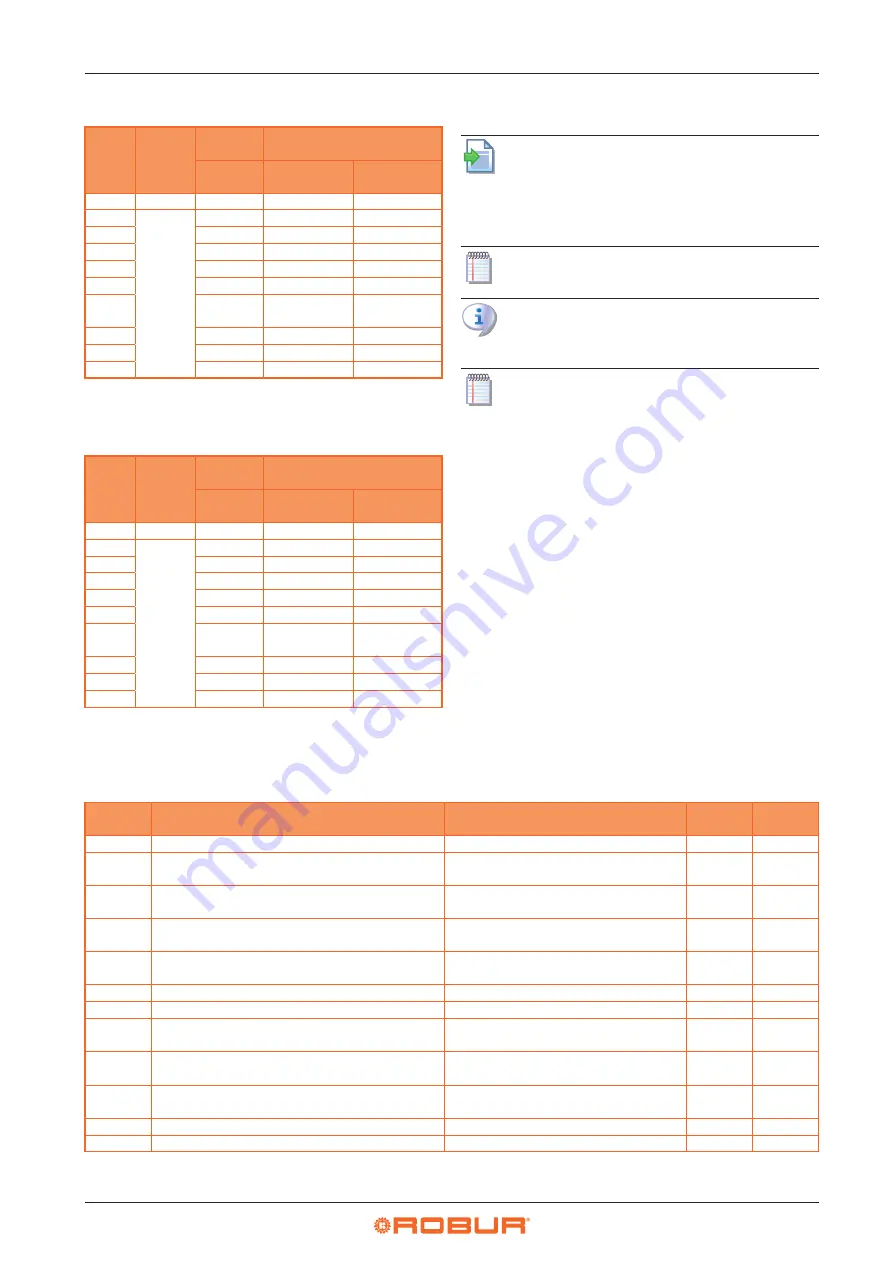
First start-up
48
5
Table 5.7
Next-G 75 gas valve setting table
Gas
Gas
network
pressure
Offset
pressure
CO
2
percentage in fumes
nominal
Minimal heat
input
Nominal heat
input
Type
mbar
Pa
%
%
G20
See Table
-5
8,5
9,2
G25
-5
8,1
8,8
G25.1
-5
9,0
9,8
G25.3
-5
8,0
8,7
G27
-5
8,2
9,0
G2.350
(1)
- (1)
- (1)
- (1)
G30
-5
9,8
10,4
G31
-5
9,7
10,2
LPG
-5
9,6
10,1
1
The gas unit heater cannot operate with this type of gas.
A tolerance of ±0,3% is applied to all values of CO
2
percentage in fumes.
Table 5.8
Next-G 90 gas valve setting table
Gas
Gas
network
pressure
Offset
pressure
CO
2
percentage in fumes
nominal
Minimal heat
input
Nominal heat
input
Type
mbar
Pa
%
%
G20
See Table
-5
8,5
9,3
G25
-5
8,1
9,3
G25.1
-5
9,3
10,4
G25.3
-5
8,2
9,3
G27
-5
8,2
9,0
G2.350
(1)
- (1)
- (1)
- (1)
G30
-5
10,2
10,7
G31
-5
9,6
10,5
LPG
-5
9,8
10,5
1
The gas unit heater cannot operate with this type of gas.
A tolerance of ±0,3% is applied to all values of CO
2
percentage in fumes.
5.3
GAS CHANGEOVER
For gas change instructions, refer to the rele-
vant documentation.
5.4
SETTING THE PARAMETERS
Paragraph dedicated to TACs and installers.
The instructions on the use of the GEN10 electronic
board concern the firmware version 1.002.
To access the installer menu (4), the password 1111
must be entered when accessing the first param-
eter in the menu. To access the menus and param-
eters Paragraph 6.4.2
Table 5.9
Next-G gas unit heaters parameters
Parameter Description of parameter
Setting
Measure-
ment unit Default
40
Modbus address
1 ÷ 128
-
1
42
Modbus remote control installed
0. No
1. Yes
-
0
45
Room temperature probe installed
0. No
1. Yes
-
1
46
Destratification temperature probe installed
0. No
1. Yes
-
0
47
Outdoor temperature probe installed
0. No
1. Yes
-
0
51
Room temperature setpoint differential
0,5 ÷ 3,0 K
K/10
10
53
Room temperature setpoint
0,0 ÷ 40,0 °C
°C/10
180
54
Fan speed in summer ventilation mode with standalone
operation
1 ÷ 4
-
4
55
Fan mode in heating mode
0. at discrete speed levels
1. fixed maximum speed
-
0
56
Standalone heating mode
0. at discrete power levels
1. power modulation (PID)
-
1
80
Destratification differential threshold
3,0 ÷ 8,0 K
K/10
70
81
Maximum destratification time
1 ÷ 15 minutes
min
10