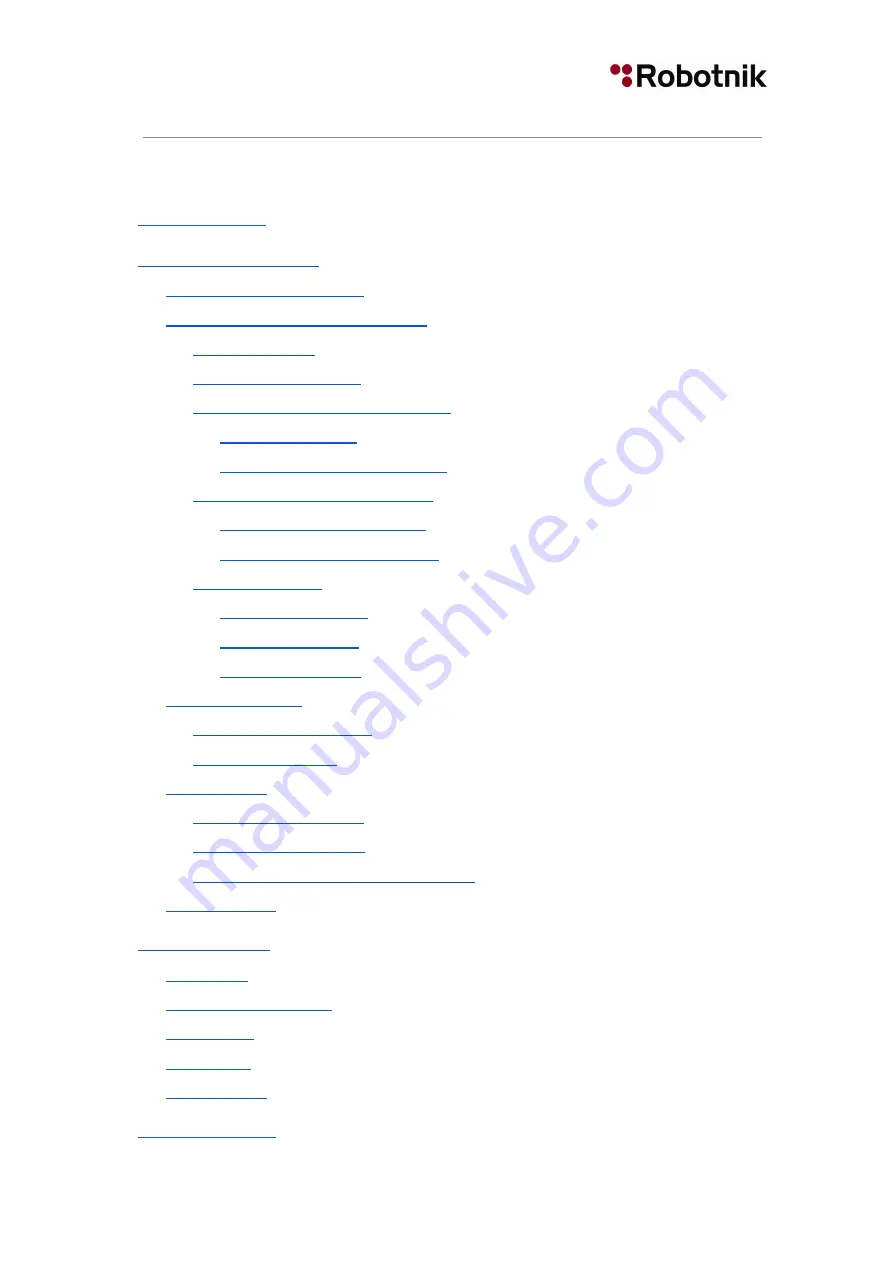
RBTNK-DOC-
161020
Hardware Manual.
RB-1 Modular Mobile Manipulator
INDEX
2.1 General overview
2.2 Components description
2.2.1 Wheels
2.2.2 Motor Driver
2.2.3 Electrical components
2.2.3.1 DC-DC
2.2.3.2 Fuses & terminal
2.2.4.1 Embbeded PC
2.2.4.2 Wireless Router
2.2.5.1 Pixhawk
2.2.5.2 Orbbec
2.2.5.3 Hokuyo
2.3.1 Control Panel
2.3.2 Gamepad
2.4.1 Battery Pack
2.4.2 LiFePo4 Cell
2.4.3 Protection circuit module
3.1 Base
3.2 Electronic box
3.3 Torso
3.4 Head
3.5 Battery
2