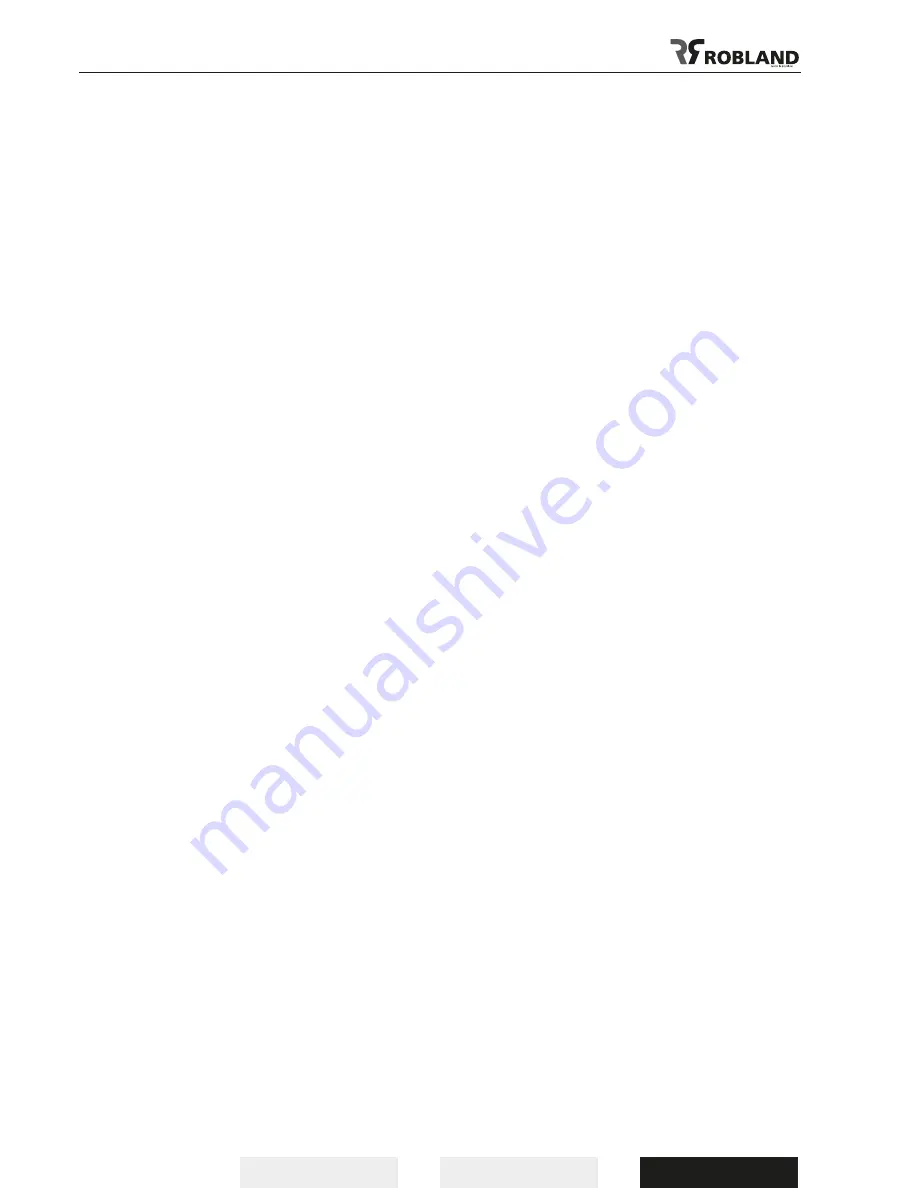
HX SERIES
V0212
5
–
English
–
Deutsch
8 Functioning of the machine, choice of safety equipment and adjustment
Because of the various tasks that can be carried out with the various types of spindle shafts, spindle
holders and cutter blocks, different types of safety equipment must be used. Every operation must be
examined separately and then the correct guarding must be chosen. The minimal opening in the table
also depends on the type of cutter block, diameter of the knives and height in which the cutter block is
adjusted. This can be done by using the able insert rings which are delivered with the machine. In that
way, the opening is as small as possible and the piece can no longer flip over and hit the knives.
Using a power feeder can prevent most serious accidents involving the hands. Such feeders can easily
be adjusted and adapted to the size of the pieces.
When no power feeder is used, the wood pushers must be used, the horizontal and vertical springs
making a tunnel in which the piece can be slid. This pusher, together with other safety equipment,
reduces the gap between the cutting tool and the guide fences.
9 Working with the spindle fence when the total length of the piece has to be machined
In most cases a straight guard fence is used. The pieces can therefore be guided in the angle made
by the table and the fence. The vertical and horizontal pushers can be placed in such way that they
make a tunnel in which the first piece can be pushed. The second piece is then used to push the first
one, the last piece is pushed forward with a wood pusher. Special blocks must be used relative to the
dimensions of the piece. When working panels of small thickness, only the top of the spring may be
used, on condition that the thickness matches.
On a spindle-moulder, the distance between the 2 extremities of the spindle guard fence must be large
enough to leave enough space for the cutter block. Thus the knives, the cutter block and the spindle
shaft may be exposed and extremity of the piece may come in contact with nose of the exit spindle
guard fence. There risks can be avoided by using a false fence between the 2 spindle guard fences
thus limiting the opening between them.
10 Working with the spindle fence when only a part of the piece is machined
When working with the spindle fence and this between 2 stops fixed onto the machine table or fences,
only a part of the work piece is machined. By doing so, the cutting tool starts to machine the wood in
the full section of the wood and does not start at the front, where the cutting action is more gradual
and less severe. The cutting action is stopped before the work piece end is reached. This action is
very dangerous and needs special care and attention. A stop solidly fixed at the front and back, must
be used (see the example further in this manual)! A piece may only be guided by hand when it is
sufficiently large, in all other cases a gauge or a support with protection must be used in order to avoid
serious accidents. By means of the gauge, the piece can be quickly and precisely be put into place
and firmly held there. A quick clamping system, working with tumblers or with cams, is most practical
system to hold the piece. When the front and backstops are fixed to the spindle guard fence or to the
table, a better control of the gauge is possible.
11 Working with the ring guard
When working with the ring guard, a support must be used, except when a certain process does not
allow this, i.e. when the piece is too large to make the use of the support practical, or when the piece is
so small or so difficult to machine that it cannot be held in the support without danger. The final shape
is obtained by holding the gauge against a guidance bearing which is fixed to the spindle while the
piece is held against the tool. The gauge can be part of the support.
12 Chamfering
When chamfering a solid support or a tilt able adjustable spindle guard fence must be used. A wood
pusher must be used for the final part of the machining.
13 Working in the same direction as the tools
It is extremely dangerous to work in the same direction as the tools, as the operator cannot exert force
to resist the strong movement of the piece as the tool comes into contact with it. Working in the same
direction as the tools as absolutely forbidden, even when a support is used.
Summary of Contents for HX TZ
Page 1: ...HX SERIE Manual Betriebsanleitung...
Page 37: ...36 V0212 HX SERIES English Deutsch...
Page 70: ...HX SERIES V0212 69 English Deutsch...
Page 71: ...70 V0212 HX SERIES English Deutsch...
Page 72: ...HX SERIES V0212 71 English Deutsch...
Page 73: ...72 V0212 HX SERIES English Deutsch...
Page 74: ...HX SERIES V0212 73 English Deutsch...
Page 75: ...74 V0212 HX SERIES English Deutsch...
Page 76: ...HX SERIES V0212 75 English Deutsch...
Page 77: ...76 V0212 HX SERIES English Deutsch...
Page 78: ...HX SERIES V0212 77 English Deutsch...
Page 79: ...78 V0212 HX SERIES English Deutsch...
Page 80: ...HX SERIES V0212 79 English Deutsch...
Page 81: ...80 V0212 HX SERIES English Deutsch...
Page 82: ...HX SERIES V0212 81 English Deutsch...
Page 83: ...82 V0212 HX SERIES English Deutsch...
Page 84: ...HX SERIES V0212 83 English Deutsch...
Page 85: ...84 V0212 HX SERIES English Deutsch...
Page 86: ...HX SERIES V0212 85 English Deutsch...
Page 87: ...86 V0212 HX SERIES English Deutsch...
Page 88: ...HX SERIES V0212 87 English Deutsch...
Page 89: ...88 V0212 HX SERIES English Deutsch...
Page 90: ...HX SERIES V0212 89 English Deutsch...
Page 91: ...90 V0212 HX SERIES English Deutsch...
Page 92: ...HX SERIES V0212 91 English Deutsch...
Page 93: ...92 V0212 HX SERIES English Deutsch...
Page 94: ...HX SERIES V0212 93 English Deutsch...
Page 95: ...94 V0212 HX SERIES English Deutsch...
Page 96: ...HX SERIES V0212 95 English Deutsch...