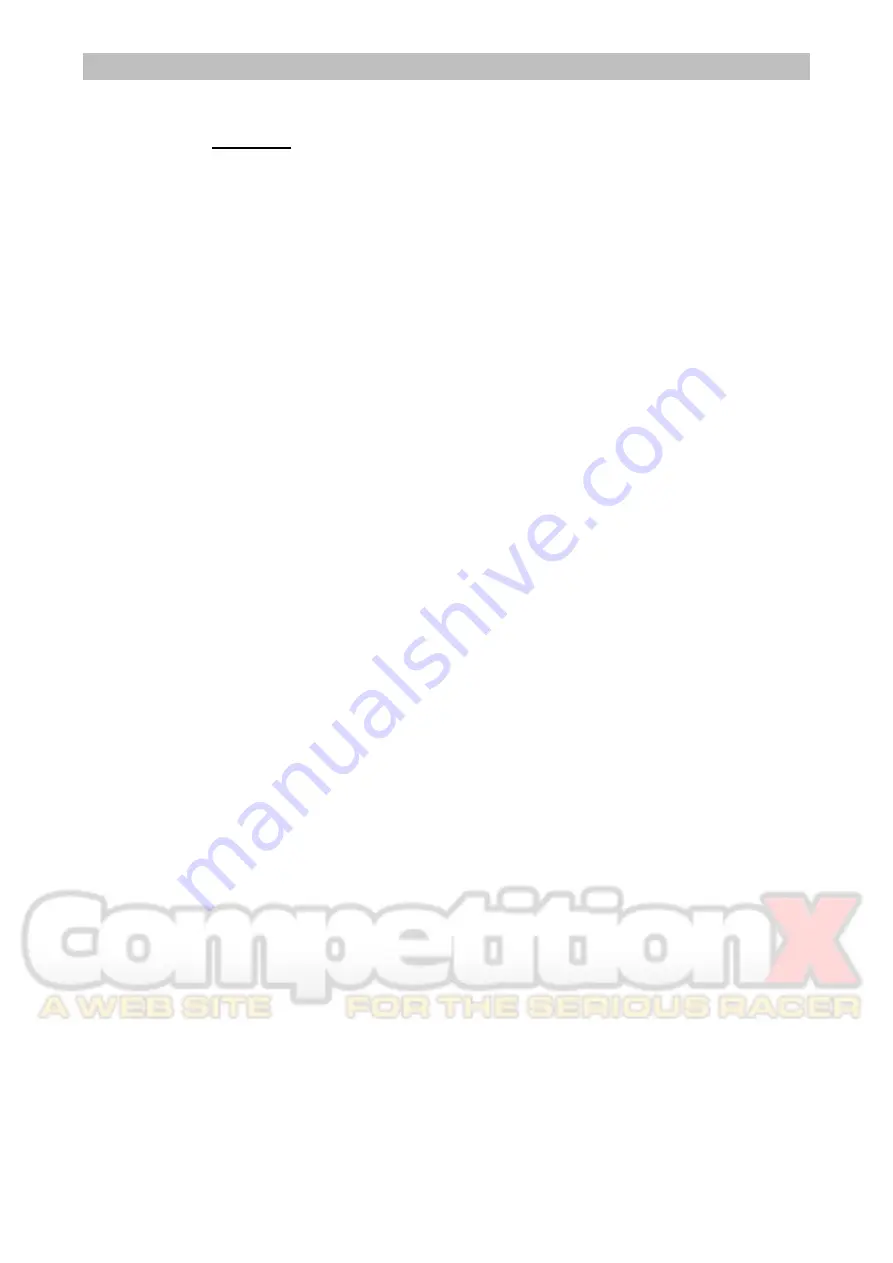
Robitronic
Pro-Master Manual
General Information
1
Contents
General information
Introduction ...................................................................2
Scope of delivery ...........................................................2
Safety precautions..........................................................3
Pro-Master operating instructions
Setup .............................................................................4
Pro-Master keys and operation.......................................4
Selecting a function........................................................5
Preparing for the motor check ........................................6
Checking the RPM sensor ..............................................7
Starting the measurement ...............................................8
Displaying motor data ..................................................10
Printing on the protocol printer ....................................11
Setting parameters for a motor check ...........................12
Ending the motor check ...............................................14
Charging battery packs.................................................15
Function diagrams........................................................18
PC Software
System requirements ....................................................20
Keyboard layout...........................................................20
Key to symbols ............................................................20
Installing the PC software ............................................21
Connecting Pro-Master to a PC....................................21
Selecting a function......................................................22
Loading motor data......................................................23
Display modes for motor data ......................................24
Meaning of motor data.................................................25
Loading benchmark data ..............................................26
Motor data in table view ..............................................27
Printing motor data ......................................................28
Program settings ..........................................................28
Motor check ................................................................30
Saving motor data ........................................................31
Example of setting motor timing...................................32
Overview of function keys............................................34
Test results ..................................................................35