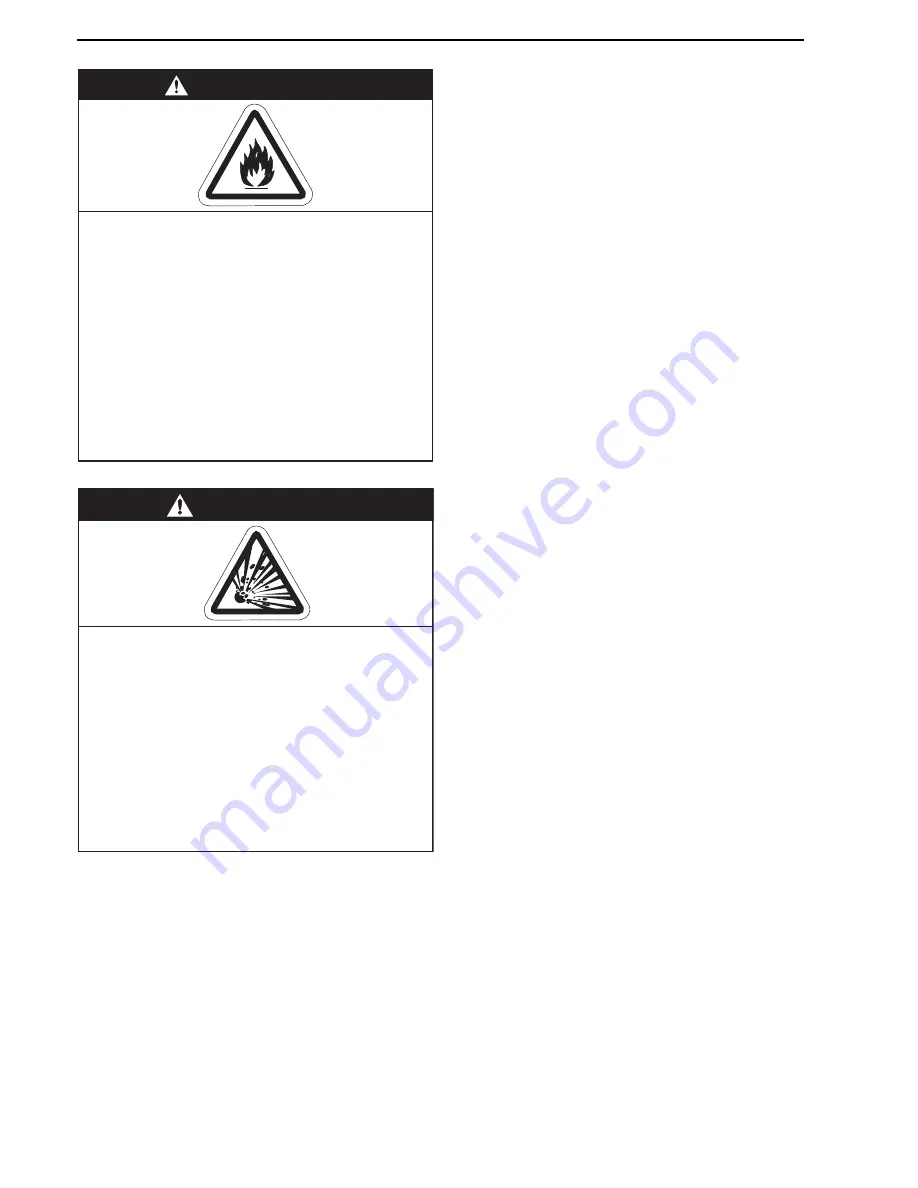
CORAYVAC
®
I
NSTALLATION
O
PERATION
AND
S
ERVICE
M
ANUAL
36 of 54
SECTION 10: GAS PIPING
It is important that the gas s
u
pply pipe and electrical
connections do not s
u
pport any of the heater’s
w
eight.
Installation pipes sho
u
ld be fitted in accordance
w
ith
N
ational Standards. Pipe
w
ork from the meter to the
heater(s) m
u
st be of adeq
u
ate size. Pipes of smaller
size than the heater inlet gas connection sho
u
ld not
be
u
sed.
Install the gas hose as sho
w
n
on Page 37, Figure 26
.
The gas hose accommodates expansion of the
heating system and allo
w
s for easy installation and
ser
v
ice of the b
u
rner. Before connecting the b
u
rners
to the s
u
pply system,
v
erify that all high press
u
re
testing of the gas piping has been completed.
There is an expansion of the t
u
be
w
ith each firing
cycle. This
w
ill ca
u
se the b
u
rner to mo
v
e
w
ith
respect to the gas hose. This can ca
u
se a gas leak
res
u
lting in an
u
nsafe condition if the gas connection
is not made in strict accordance
w
ith
Figure 26
.
Meter and ser
v
ice m
u
st be large eno
u
gh to handle
all the b
u
rners being installed pl
u
s any other con-
nected load. The gas hose
w
hich feeds the system
m
u
st be large eno
u
gh to s
u
pply the req
u
ired gas
w
ith a maxim
u
m press
u
re drop of 1.5 mbar. When
gas piping is not incl
u
ded in the layo
u
t dra
w
ing, the
local gas s
u
pplier
w
ill
u
s
u
ally help in planning the
gas piping.
IMPORTA
N
T - the complete installation m
u
st be
tested for gas so
u
ndness and be p
u
rged in accor-
dance
w
ith local and national codes.
• Check the pipe and tubin
g
ends for leaks
before placin
g
heatin
g
e
q
uipment into
service. When checkin
g
for
g
as leaks, use a
soap and water solution; never use an open
flame.
WARNING
Fire Hazard
Tighten gas line fittings to connect gas supply
according to Figure 26.
Flex gas line can crack when twisted.
Gas line moves during normal operation.
Use only 1000 mm long connector of 1/2" or
3/4" nominal ID.
Failure to follow these instructions can result
in death, injury or property damage.
WARNING
Explosion Hazard
Leak test all components of gas piping
before operation.
Gas can leak if piping is not installed
properly.
Do not high pressure test gas piping with
heater connected.
Failure to follow these instructions can result
in death, injury or property damage.
Summary of Contents for CoRayVac CRT-10
Page 2: ......
Page 4: ......
Page 6: ......
Page 53: ...SECTION 14 TROUBLESHOOTING 47 of 54 14 1 Troubleshooting Flow Chart ...
Page 61: ......