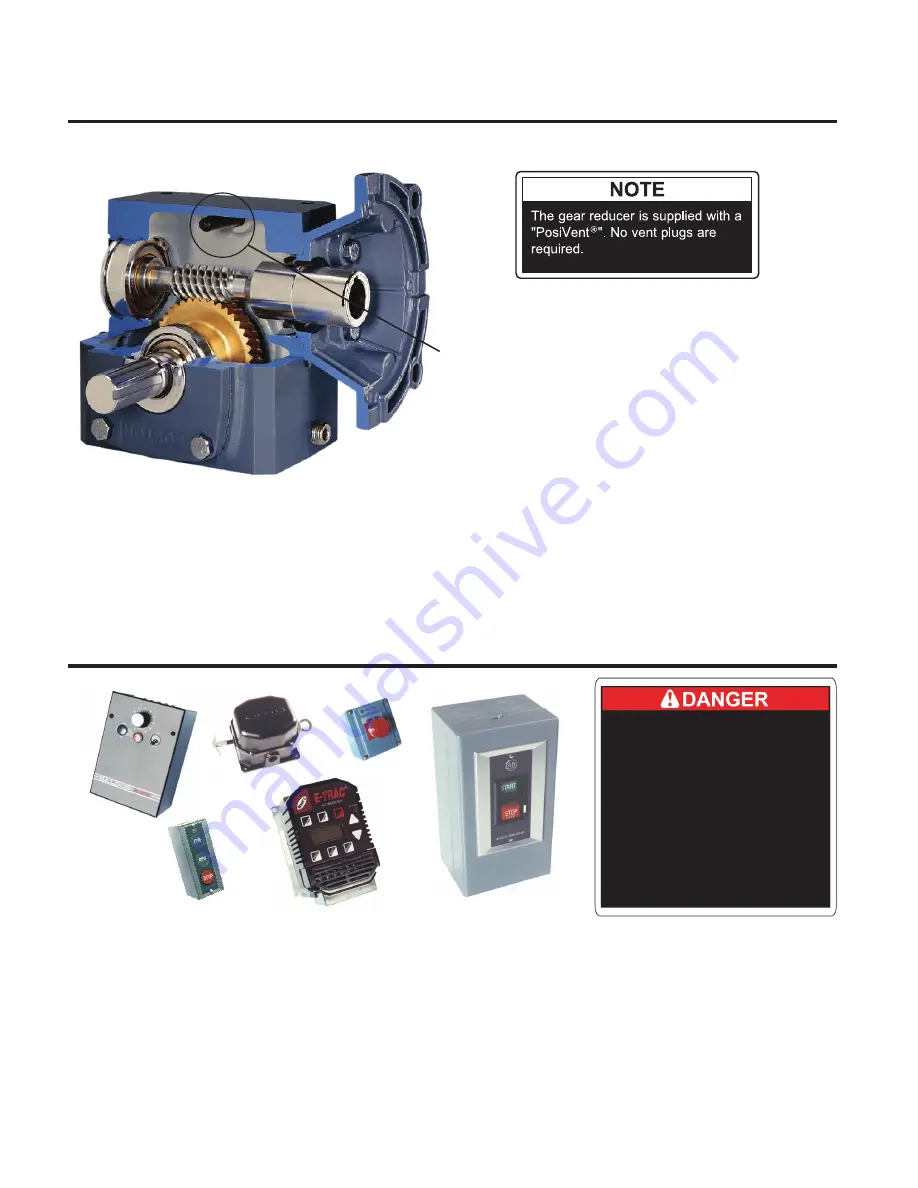
13
START-UP PROCEDURES
®
GEAR REDUCER WITH POSIVENT
PREPARING FOR INITIAL START-UP
Before conveyor start-up, all operators and
other personnel coming in contact with unit
must be properly trained and must have
read accompanying Tech Handbook.
Provisions must be in order to instruct all
personnel coming in contact with conveyor
on the location of emergency stops,
pull cords, etc.
A routine maintenance program should
be implemented before unit is placed into
operation so that fundamental unit compo-
nents are attended to. This maintenance
program should include an inspection to
ensure that any dangerous or hazard-
ous operating conditions are noted and
IMMEDIATELY corrected, as well as
including electrical and mechanical unit
inspections and corrections.
Finally, when conveyor is initially started,
an immediate visual inspection should
include motor, gear reducer, belt track-
ing (discussed in following section under
“Belt Tracking”) and related adjustments
noted in handbook for unit/component
corrections.
WARN ALL PERSONNEL TO KEEP CLEAR
OF CONVEYOR DURING UNIT START-UP
Electrical controls must be designed by a
qualified electrical engineer to ensure that
appropriate safety features (emergency stops,
pull cords, switches, etc.) are installed on unit
for safe operation. Before conveyor start-up,
all operators and other personnel coming in
contact with unit must be properly trained
and must have read accompanying Tech
Handbook.
PosiVent
Unique design incorporates a single
seam construction. Factory filled with
synthetic lubrication for universal mounting. Lubed
for life, no oil changes are required.
To expedite the installation and start-up process, all gear red ucers are shipped filled with oil. The reducers are sealed and
lubed for life and require no oil changes.
Summary of Contents for 251CALR
Page 1: ......