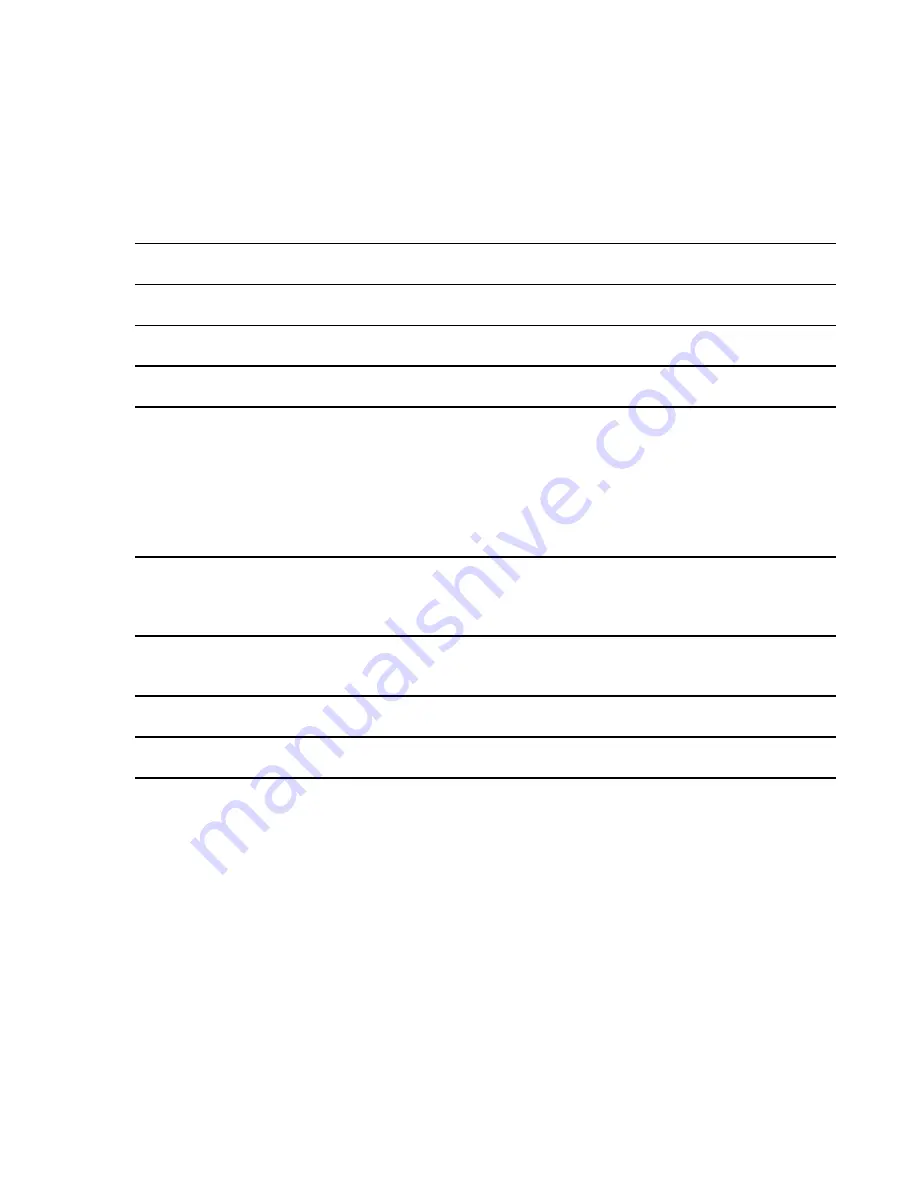
R325P User Manual
Page
4
of
20
1/31/2013 Version 1.0
Table
of
Contents
1.
FEATURES
........................................................................................... 5
2.
ELECTRICAL
SPECIFICATIONS
...................................................................... 5
3.
OPERATING
SPECIFICATIONS
...................................................................... 6
4.
MECHANICAL
SPECIFICATIONS
.................................................................... 6
6.
CONNECTION
SPECIFICATIONS
.................................................................... 8
Connecting
the
Power
................................................................................................ 9
Connecting
the
Motor
................................................................................................ 9
Configure
the
R325
using
the
DIP
Switch
.......................................................................... 10
DIP
Switch
Run
Current
Settings
.............................................................................................. 10
DIP
Switch
Hold
Current
Settings
............................................................................................. 11
DIP
Switch
Step
Resolution
Settings
.......................................................................................... 11
8.
COMMAND
TABLES
.............................................................................. 11
Axis
Configuration
Commands
..................................................................................... 11
General
Operation
Commands
..................................................................................... 11
9.
COMMANDS
...................................................................................... 13
Protocol
Syntax
..................................................................................................... 13
10.
Troubleshooting
................................................................................. 14
11.
Appendix
A
...................................................................................... 15
11.
Appendix
B
...................................................................................... 19