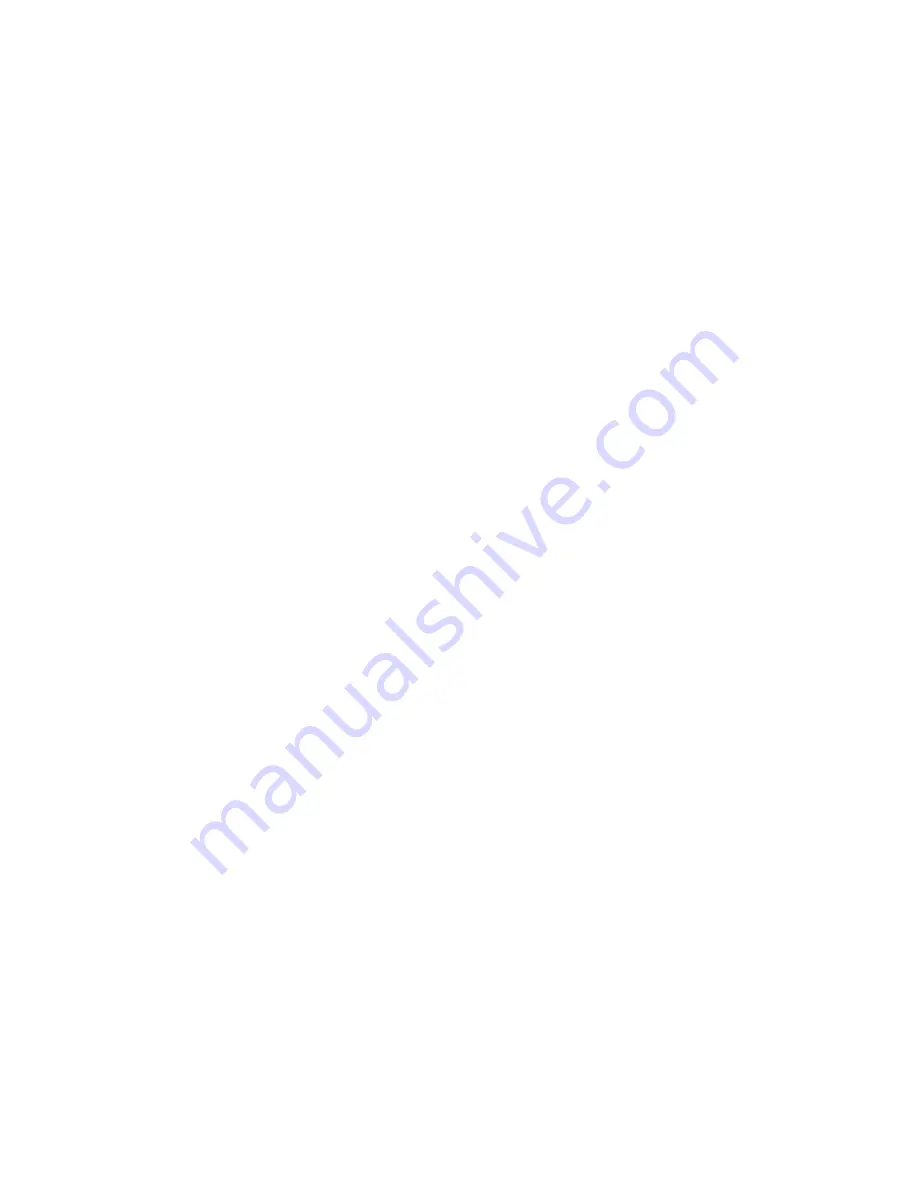
Introduction
1. The boiler and all associated equipment must be installed and used in accordance with the installation design,
all applicable legal regulations and technical standards and with the manufacturer’s instructions. The boiler
may be used only for the purpose for which it is intended
may be used only for the purpose for which it is intended.
2. The boiler may be installed only in an environment which it is designed for.If the boiler is delivered to the client
by the same person who installs it, he must give the user also all accompanying boiler documentation
( in particular User Guide, Service Book, etc. ). Until the boiler is put into service, the original packaging must
be kept in case the boiler has to be transported again.
3. After installation, the boiler must be put into operation by a service organisation authorized by the manufac-
turer.
4. The boiler complies with regulations applicable in the European Union. When used in the conditions of
countries outside at EU, any deviations from local regulations must be identified and rectified.
5. In the event of a defect, call an authorized manufacturer’s service organisation–any unauthorized interference
5 In the event of a defect, call an authorized manufacturer s service organisation any unauthorized interference
may damage the boiler (and possibly also associated equipment!).
6. The service technician putting the boiler into operation for the first time must show the user the various parts
of the boiler and how to control the boiler, with the boiler safety elements, their signals and appropriate user
reaction to them, with fundamental parts of the boiler and their controls. If the boiler is delivered to the client
by the same person who installs it,he must make sure that the original packaging is available in case the
b il
h
t b t
t d
i
boiler has to be transported again.
7. Check the delivery for completeness.
8. Check whether the model and type supplied is suitable for the required use.
9. Whenever you are not certain how to control the boiler, study appropriate instructions in this Operation and
installation Guide carefully and proceed accordingly.
.
10. Never remove or damage any markings and signs on the boiler. Keep the original packaging until the boiler
has been put into service, in case the boiler has to be transported again.
11. When making any repairs , only original parts must always be used. It is forbidden to make any changes
to the boiler’s internal installation or to interfere with it in any way
to the boiler s internal installation, or to interfere with it in any way.
12. At the end of its life cycle, the boiler its package and its parts must be disposed of in a way avoiding harm
to the environment.
13 The manufacturer disclaims any responsibility for damages caused by the failure to abide by:
• The conditions stipulated in this Operation and Installation Guide
5
Summary of Contents for S.MAX Series
Page 1: ...S MAX SERIES SOLID FUEL BOILER S MAX SERIES SOLID FUEL BOILER 0 S MAX REV 01 2010 0036 0036...
Page 4: ...Boiler dimensions Boiler packaging dimensions 3...
Page 5: ...Technical parameters 4...
Page 17: ...fig 12 fig 13 fig 14 fig 15 16...
Page 22: ...SMAX boiler parts fi 18 fig 18 fig 19 21...
Page 23: ...Spare parts list p p fig 20 22...