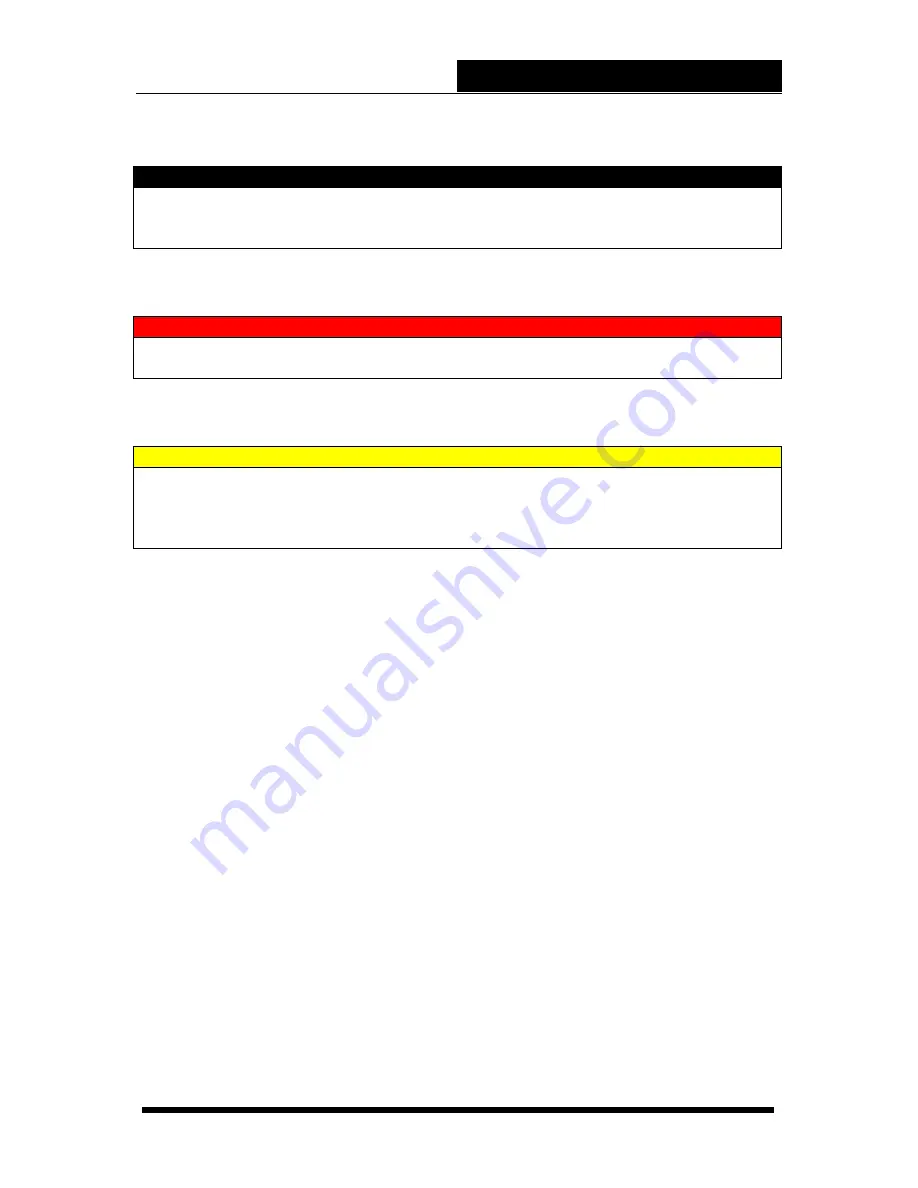
LG200 Owner's Manual
Safety
Page 6
MTS-T4-LG200-Owners-Manual-052815
4. Engine Hoist Points
NOTE: ENGINE HOIST POINTS
The Kohler engine has hoist points that are useful for removal and reinstallation
of the engine. It is advised that these hoist points should only be used if no other
means of lifting the unit are available.
5. Starting Aids
WARNING!
Do not use any type of starting aids such as ether. Such use could result in an
explosion and personal injury, and will render the APU warranty null and void.
6. Starting with the Cover Off
CAUTION
Some installation or repair/diagnostic procedures require that the APU is started
with the engine cover off. Do not deactivate or bypass the safety cover switch.
Instead, have another individual assist by manually holding the safety cover
switch down in the closed position for the duration of the procedure.
7. Inspection of the Safety Systems
The safety systems on the RigMaster APU should be examined and tested prior
to performing any service work and at 50 hour intervals to ensure that they are in
good condition and proper working order.
8. Safe Working Practices
Safe working practices are your responsibility. The use of protective safety
equipment is mandatory when performing inspections, service, diagnostics and
repairs on the RigMaster APU. Follow your local regulations and guidelines
regarding occupational health and safety.
9. Contact Us
If you do not fully understand this safety information contact RigMaster’s
Technical Support Department toll free at (888) 208
– 3101 before proceeding
with the operation or service of this APU.