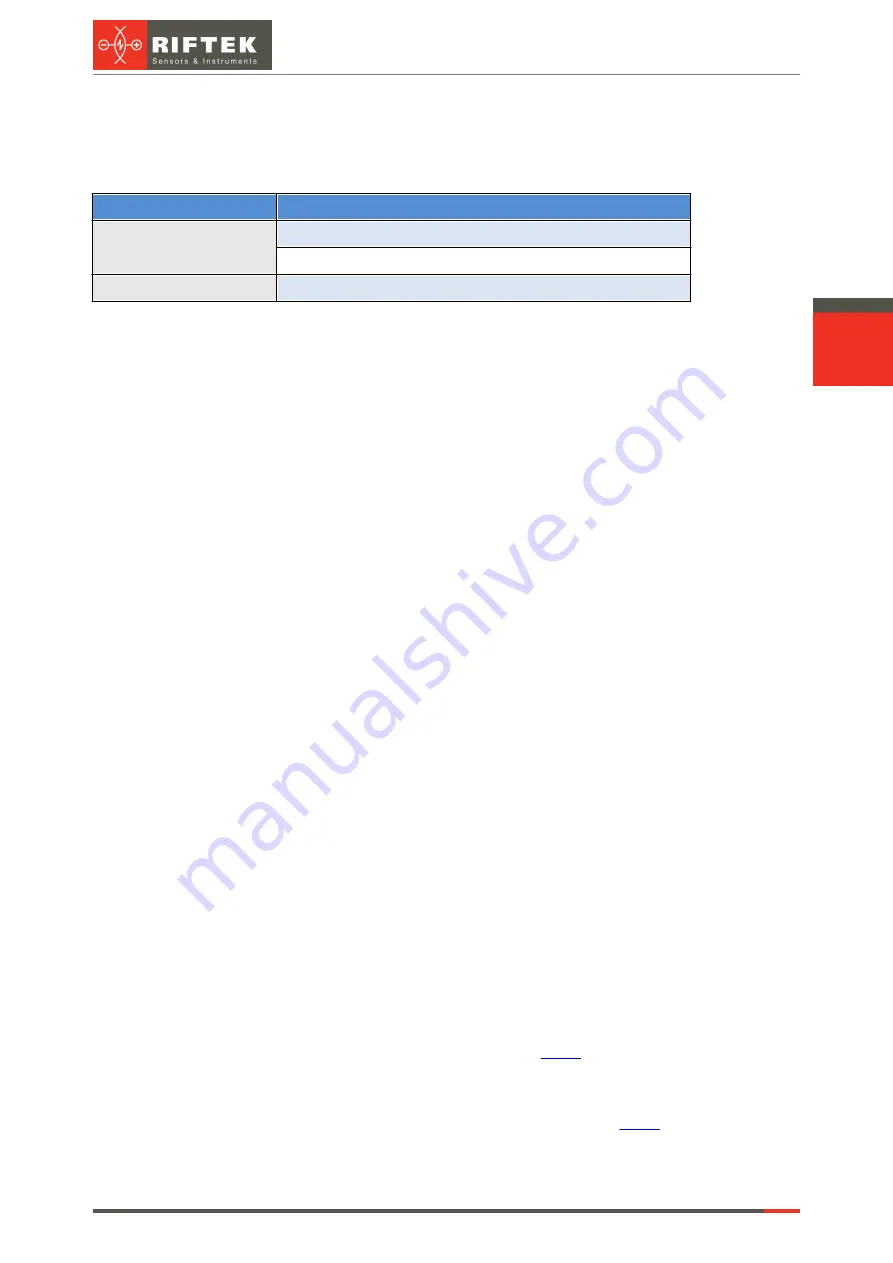
30
Pipe ID Control System. RF096-35/55-100 Series
RF096-35/55-100 [Revision 1.0.0] 12.12.2018
12.6. Diagnostic messages
The I-7580 module has two types of diagnostic messages: "Output Data Error" and
"Input Data Error".
Type
Description
Output Data Error
FIFO overflow.
Data loss.
Input Data Error
FIFO overflow.
12.6.1. Output Data Error
1. When the PROFINET network speed is higher than the serial network speed and
the PROFINET IO controller continuously transmits data to the I-7580 module, the
output buffer of the I-7580 module will overflow, and the I-7580 module will send a
diagnostic message "Output Data Error – FIFO overflow".
2. When the I-7580 module receives the data output command (first byte of the
output data area, please refer to section "PROFINET Output Data Area") from
the PROFINET IO controller and the command is not increased continuously (for
example: 0->1, 1->2 ... 254->255, 255->0), the I-7580 module will send a
diagnostic message "Output Data Error – Data loss" to the PROFINET IO
controller.
12.6.2. Input Data Error
1. When the serial network speed is higher than the PROFINET network speed and
the serial device continuously transmits data to the I-7580 module, the input
buffer of the I-7580 module will overflow, and the I-7580 module will send a
diagnostic message "Input Data Error – FIFO overflow".
2. When the I-7580 module cannot receive data in time from the COM port, it will
send a diagnostic message "Input Data Error – Data loss". Please refer to
section "PROFINET Input Data Area".
3. The maximum input data length for the COM port of the I-7580 module is 506
bytes. When the COM port of the I-7580 module receives data larger than 506
bytes, it will send a diagnostic message "Input Data Error – Data overflow".
13. Intended use
13.1. Preparation for use
·
Check the condition of the output window of a laser sensor and, if necessary, wipe
it with a soft cloth.
·
Rotate a laser sensor by hand and check the smooth progress.
·
Check the cables and power supply.
·
Make sure that the network settings are correct.
·
Switch on the system.
·
Run the test procedures. Please refer to section
13.2. Measurements
Run the sequence of commands described in section
between PLC and system".