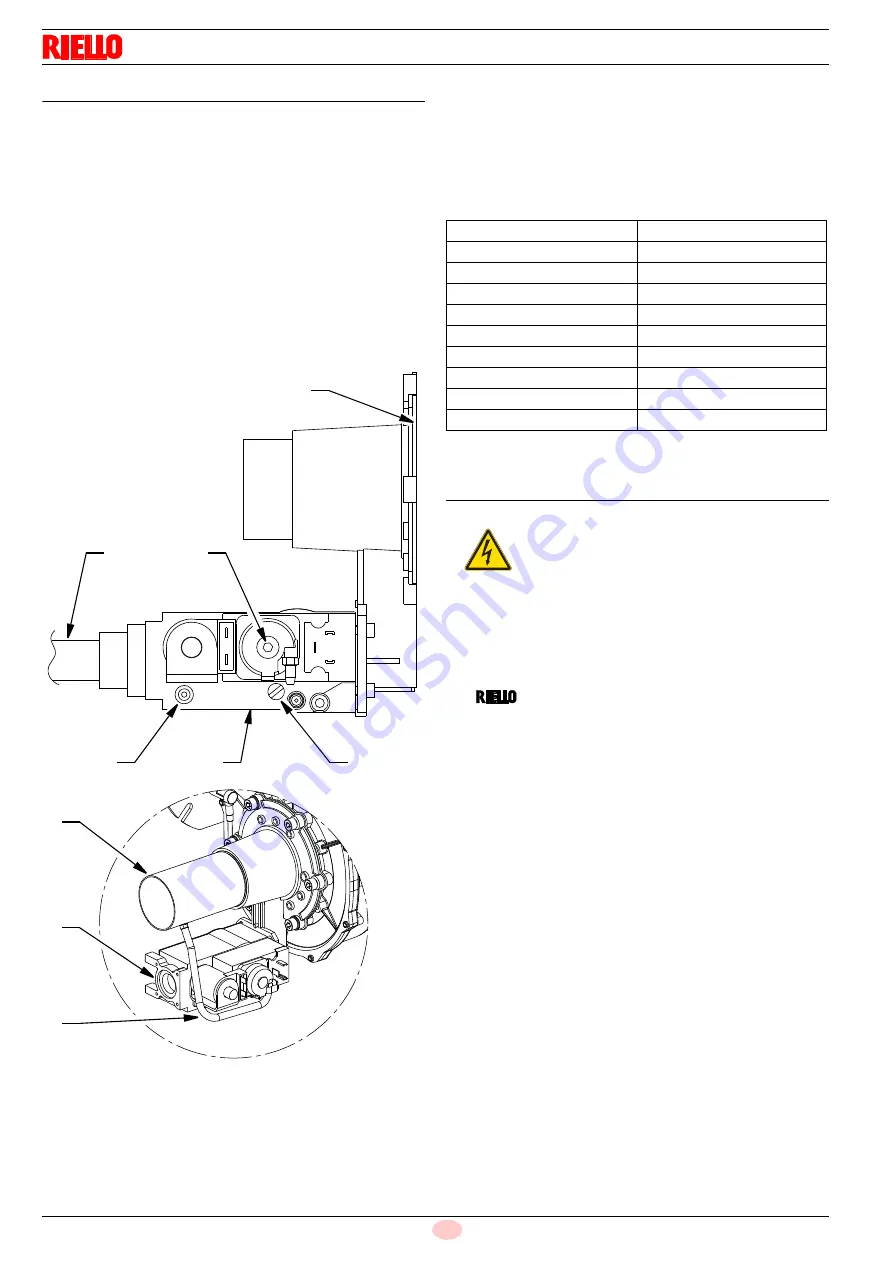
20017376
10
GB
Installation
5.7
Fuel supply
The burners are teamed with one-piece pneumatic proportioning
gas valves, via which the amount of gas delivered, and hence the
output produced, can be modulated.
A signal reporting pressure detected in the air circuit is carried to
the pneumatic gas valve, which delivers an amount of gas in pro-
portion to the airflow produced by the fan.
The gas train, in order to render the dimensions efficent is assem-
bledd directly onto the burner body.
5.7.1
Gas train assembly
With the valve/manifold connection, accidental blocking of the in-
take can be compensated by reducing the amount of gas deliv-
ered.
1
Gas supply
2
Gas pressure test point upline (P1)
3
Gas valve
4
Maximum flow adjustment (V1)
5
Air/gas mixer in intake circuit
6
Minimum gas flow adjustment on the stabiliser (V2)
7
Manifold
8
Gas compensation pipe
Air/gas mixer
Gas and combustive air are mixed inside the purging circuit (mix-
er), starting from the intake inlet.
Through the gas train, fuel is introduced into the intake air current
and optimal mixing commences with the aid of a mixer.
5.7.2
Gas valve
Tab. A
5.8
Electrical wiring
The electrical wiring must be carried out with the electrical
supply disconnected.
Electrical wiring must be carried out by qualified personnel
and in compliance with the regulations currently in force in
the country of destination. Refer to the wiring diagrams.
declines all responsibility for modifications or con-
nections different from those shown in the electrical layouts.
Do not invert the neutral with the phase in the electrical sup-
ply line. Any inversion would cause a lockout due to firing
failure.
The electrical safety of the device is obtained only when it is
correctly connected to an efficient earthing system, made
according to current standards. It is necessary to check this
fundamental safety requirement. In the event of doubt, have
the electrical system checked by qualified personnel.
The electrical system must be suitable for the maximum
input power of the device, as indicated on the label and in
the manual, checking in particular that the section of the
cables is suitable for the input power of the device.
For the main power supply of the device from the electricity
mains:
- do not use adapters, multiple sockets or extensions;
- use an omnipolar switch with an opening of at least 3 mm
(overvoltage category) between the contacts, as indi-
cated by the current safety standards.
Do not touch the device with wet or damp body parts and/or
in bare feet.
Do not pull the electric cables.
Fig. 7
D7452
D7453
1
5
6
2
4
3
7
1
8
Valve model
Honeywell VR4615VB1006
Mixer model
Honeywell 45900450-0301
Gas line connection
3/4" inlet
Working temperature
-15°C/70°C
Max. working pressure
30 mbar
Min. working pressure
15 mbar
Max. inlet pressure
60 mbar
Valve class
B + C
Electrical supply
220-240 V
IP
IP 40 according to IEC 529
DANGER
Notes on safety for the electrical wiring