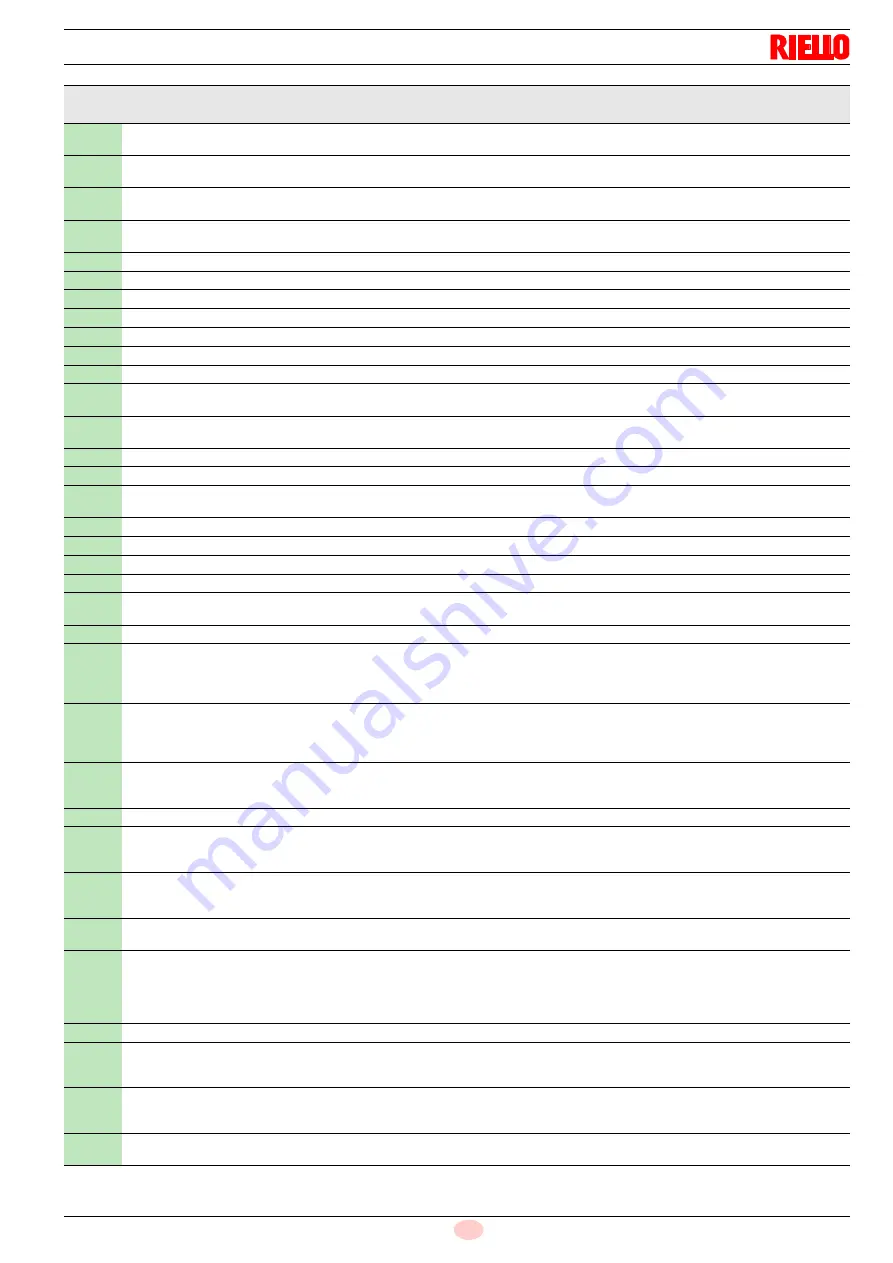
55
20068131
GB
Faults - Probable causes - Solutions
50 ÷ 58
#
Internal error
Carry out a reset; if the error arises repeatedly, replace the
control box
60
0
Internal error: no valid load checking device
Carry out a reset; if the error arises repeatedly, replace the
control box
65 ÷ 67
#
Internal error
Carry out a reset; if the error arises repeatedly, replace the
control box
70
#
Fuel/air checking error: Calculation position in
modulation
23
Invalid load
No valid load
26
Curve points not defined
Adjust the curve points of all the actuators
71
#
Special position not defined
0
Standby position
Set the standby position of all the servomotors used
1
Pre-purging position
Set the pre-purging position of all the servomotors used
2
Post-purging position
Set the post-purging position of all the servomotors used
3
Ignition position
Set the ignition position of all the servomotors used
72
#
Fuel/air internal checking error:
Carry out a reset; if the error arises repeatedly, replace the
control box
73
#
Fuel/air internal checking error: multistep calculation
position
23
Position calculation, invalid stage load
No valid load
26
Position calculation, stage curve points not defined
Adjust the curve points of all the servomotors
75
#
Fuel/air ratio internal checking error: cyclical data
check
1
Check synchronisation data, different current load
2
Check synchronisation data, different target load
4
Check synchronisation data, different target positions
16
Check synchronisation data, different positions reached
76
#
Fuel/air internal checking error:
Carry out a reset; if the error arises repeatedly, replace the
control box
85
#
Reference error of a servomotor
0
Reference error of the fuel servomotor
The reference of the fuel servomotor was not successful.
It was not possible to reach the reference point.
1. Check if the servomotors have been inverted.
2. Check if the servomotor is blocked or overloaded.
1
Reference error of the air servomotor
The reference of the air servomotor was not successful.
It was not possible to reach the reference point.
1. Check if the servomotors have been inverted.
2. Check if the servomotor is blocked or overloaded.
Bit 7
Valence
128
Reference error owing to parameter modification
The parameterisation of an actuator (e.g. the reference
position) has been modified. This error will be visualised to start
up a new reference.
86
#
Fuel servomotor error
0
Position error
It was not possible to reach the target position within the
requested tolerance range.
1. Check if the servomotor is blocked or overloaded.
Bit 0
Valence 1
Circuit open
Circuit open shown on the servomotor connection.
1. Check the wiring (the voltage between pin 5 or 6 and 2 of the
X54 connector must be > 0.5 V).
Bit 3
Valence
8
Curve too steep in terms of train ratio
The slope of the curve can correspond to a maximum position
modification of 31° between 2 points of the modulation curve.
Bit 4
Valence
16
Deviation of section compared with the last reference
Overloading of the servomotor or servomotor subjected to
mechanical torsion.
1. Check if the servomotor is blocked in any point along its
range of action.
2. Check if the torque is sufficient for the application.
87
#
Air servomotor error
0
Position error
It was not possible to reach the target position within the
requested tolerance range.
1. Check if the servomotor is blocked or overloaded.
Bit 0
Valence 1
Circuit open
Circuit open shown on the servomotor connection.
1. Check the wiring (the voltage between pin 5 or 6 and 2 of the
X54 connector must be > 0.5 V).
Bit 3
Valence
8
Curve too steep in terms of train ratio
The slope of the curve can correspond to a maximum position
modification of 31° between 2 points of the modulation curve.
Error
code
Diagnostic code
Meaning of the REC 27.100A2 system
Recommended measures
Summary of Contents for RS 34/E MZ
Page 2: ...Translation of the original instructions ...
Page 65: ...63 20068131 GB Appendix Electrical panel layout RS 34 E MZ ...
Page 66: ...20068131 64 GB Appendix Electrical panel layout RS 44 E MZ ...
Page 67: ...65 20068131 GB Appendix Electrical panel layout RS 44 E MZ 3Ph ...
Page 68: ...20068131 66 GB Appendix Electrical panel layout RS 34 44 E MZ ...
Page 69: ...67 20068131 GB Appendix Electrical panel layout RS 44 E MZ 3Ph ...
Page 70: ...20068131 68 GB Appendix Electrical panel layout ...
Page 71: ...69 20068131 GB Appendix Electrical panel layout ...
Page 72: ...20068131 70 GB Appendix Electrical panel layout ...
Page 73: ...71 20068131 GB Appendix Electrical panel layout ...
Page 75: ......