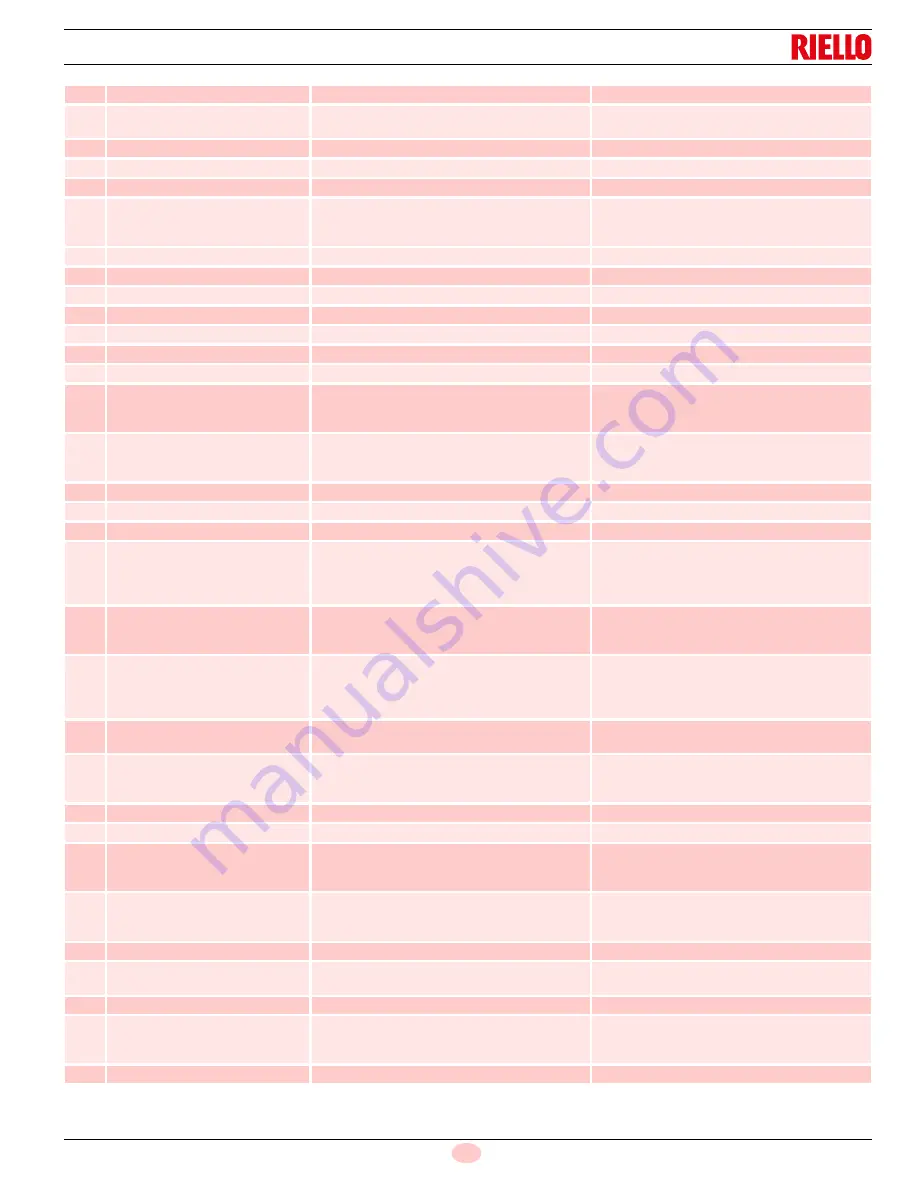
Problems - Causes - Remedies signalled by LED indicators
43
20160742
GB
Tab. K
33
False flame in stand-by mode
Unexpected flame (false or parasitic flame)
detected during the Stand-by status
Check flame sensor or interference
34
Not used
35
Internal processor timeout
Internal fault
Replace the control device
36
Internal processor timeout
Internal fault
Replace the control device
37
Combustion air check timeout
The system could not perform verification
tests of the combustion air during the burner
sequence
Check the wiring or the air pressure switch
38
Internal processor timeout
Internal fault
Replace the control device
39
Internal processor timeout
Internal fault
Replace the control device
40
Internal hardware fault
Internal fault
Replace the control device
41
Internal hardware fault
Internal fault
Replace the control device
42
Main processor fault
Internal fault
Replace the control device
43
Supervisor processor fault
Internal fault
Replace the control device
44
Supervisor processor time-out
Internal fault
Replace the control device
45
Off-specification mains voltage
Off-specification mains voltage/frequency
Check the mains voltage level or the
frequency. Contact the factory if the problem
persists
46
Off-specification mains voltage
Off-specification mains voltage/frequency
Check the mains voltage level or the
frequency.
Contact the factory if the problem persists
47
UV: Internal fault
Internal fault
Replace the control device
48
Supervisor processor fault
Internal fault
Replace the control device
49
Main processor fault
Internal fault
Replace the control device
50
Ignition feedback fault
The system detected the presence of voltage
on T16 at the wrong moment or there is no
voltage when necessary
Check the wiring and make sure that the
earthing is appropriate
If the problem persists, contact the distributor/
factory
51
Pilot feedback fault
The system detected the presence of voltage
on T17 at the wrong moment or there is no
voltage when necessary
Check the wiring and make sure that the
earthing is appropriate. If the problem
persists, contact the distributor/factory
52
Piloted valve feedback fault
The system detected the presence of voltage
on T19 at the wrong moment or there is no
voltage when necessary
Check the wiring and make sure that the
earthing is appropriate
If the problem persists, contact the distributor/
factory
53
Actuator feedback waiting time
expired
No actuator feedback on T8 for more than 10
minutes
Check the wiring
Check the modulation equipment
54
Direct ignition valve feedback
fault
The system detected the presence of voltage
on T18 at the wrong moment or there is no
voltage when necessary
Check the wiring and make sure that the
earthing is appropriate. If the problem
persists, contact the distributor/factory
55
Internal processor fault
Internal fault
Replace the control device
56
UV: false flame during operation False flame detected before ignition
Check the flame sensor
57
FR: false flame during operation False flame detected before ignition
Check the wiring
Check the flame sensor
Make sure that earthing is appropriate
58
T8 inlet fault
The system detected the presence of voltage
on T8 at the wrong moment or there is no
voltage when necessary
Check the wiring
Check the actuator
59
Internal hardware fault
Internal fault
Replace the control device
60
Local reset fault
Local reset button pressed for more than 10
seconds or reset button locked
If the problem persists, replace the control
device
61
Open POC fault
The fuel valve is open at the wrong moment
Check the wiring
62
UV: strong UV flame fault
The flame sensor is too close to the flame
Increase the distance between the sensor
and the flame OR use an orifice to reduce the
view field
63
Internal hardware fault
Internal fault
Replace the control device
No
Faults
Cause
Solution
Summary of Contents for RS 190/M
Page 2: ...Original instructions...
Page 20: ...20160742 18 GB Installation 4 7 1 Electrical connections Fig 15 S9810...
Page 51: ......