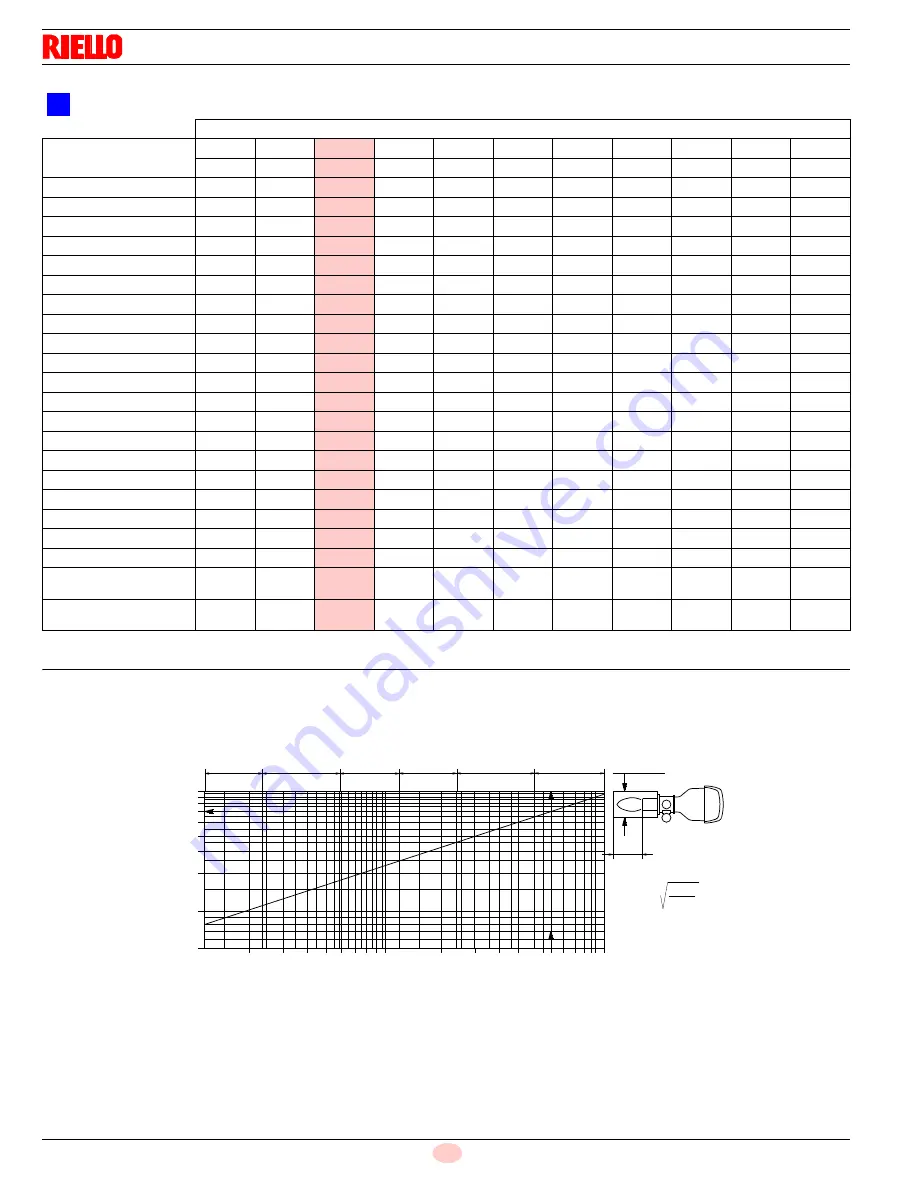
20049577
10
GB
Technical description of the burner
3.7
Minimum furnace dimensions
The firing rate was obtained in special test boilers.
Fig. 4 indicates the diameter and length of the test combustion
chamber.
Example:
Output 26510 Mbtu/hr: - diameter 47.7 inch - length 20 ft.
CORRECTED BURNER AIR PRESSURE ACCORDING TO ALTITUDE
Altitude
Rated Pressure
m a.s.l.
0
100
305
610
915
1220
1525
1830
2135
2440
ft a.s.l
0
328
1000
2000
3000
4000
5000
6000
7000
8000
0.50
0.49
0.50
0.51
0.53
0.55
0.57
0.59
0.62
0.64
0.67
1.00
0.99
1.00
1.02
1.06
1.10
1.14
1.19
1.23
1.28
1.34
1.50
1.48
1.50
1.53
1.59
1.65
1.71
1.78
1.85
1.92
2.01
2.00
1.97
2.00
2.05
2.12
2.20
2.28
2.37
2.46
2.56
2.67
2.50
2.47
2.50
2.56
2.65
2.75
2.85
2.96
3.08
3.21
3.34
3.00
2.96
3.00
3.07
3.18
3.30
3.43
3.56
3.70
3.85
4.01
3.50
3.46
3.50
3.58
3.71
3.85
4.00
4.15
4.31
4.49
4.68
4.00
3.95
4.00
4.09
4.24
4.40
4.57
4.74
4.93
5.13
5.35
4.50
4.44
4.50
4.60
4.77
4.95
5.14
5.33
5.54
5.77
6.02
5.00
4.94
5.00
5.12
5.30
5.51
5.71
5.93
6.16
6.41
6.69
5.50
5.43
5.50
5.63
5.83
6.06
6.28
6.52
6.77
7.05
7.35
6.00
5.92
6.00
6.14
6.36
6.61
6.85
7.11
7.39
7.69
8.02
6.50
6.42
6.50
6.65
6.89
7.16
7.42
7.71
8.01
8.34
8.69
7.00
6.91
7.00
7.16
7.42
7.71
7.99
8.30
8.62
8.98
9.36
7.50
7.40
7.50
7.67
7.96
8.26
8.56
8.89
9.24
9.62
10.03
8.00
7.90
8.00
8.18
8.49
8.81
9.13
9.48
9.85
10.26
10.70
8.50
8.39
8.50
8.70
9.02
9.36
9.71
10.08
10.47
10.90
11.37
9.00
8.88
9.00
9.21
9.55
9.91
10.28
10.67
11.09
11.54
12.04
9.50
9.38
9.50
9.72
10.08
10.46
10.85
11.26
11.70
12.18
12.70
10.00
9.87
10.00
10.23
10.61
11.01
11.42
11.86
12.32
12.82
13.37
Average barometric
pressure (20°C)
mbar
1013
1000
977.4
942.8
908.2
875.8
843.5
811.85
779.8
747.8
Average barometric
pressure (68°F)
"w.c.
399
394
385
371
358
345
332
320
307
294
2
Fig. 4
1000
MBtu/hr760
1.5
7.5 11.3 18.9
37870
1.6
3.3
6.6
9.9
13.2
16.5
29.6
23.0
1 5 . 7
1 9 . 7
2 3 . 6
3 1 . 5
3 9 . 4
4 7 . 2
i n c h es
f t
ft= 0,12 MBtu
hr
22.7
D9084
Summary of Contents for RS 1200/E BIOGAS/GPL C01 FS2
Page 2: ......