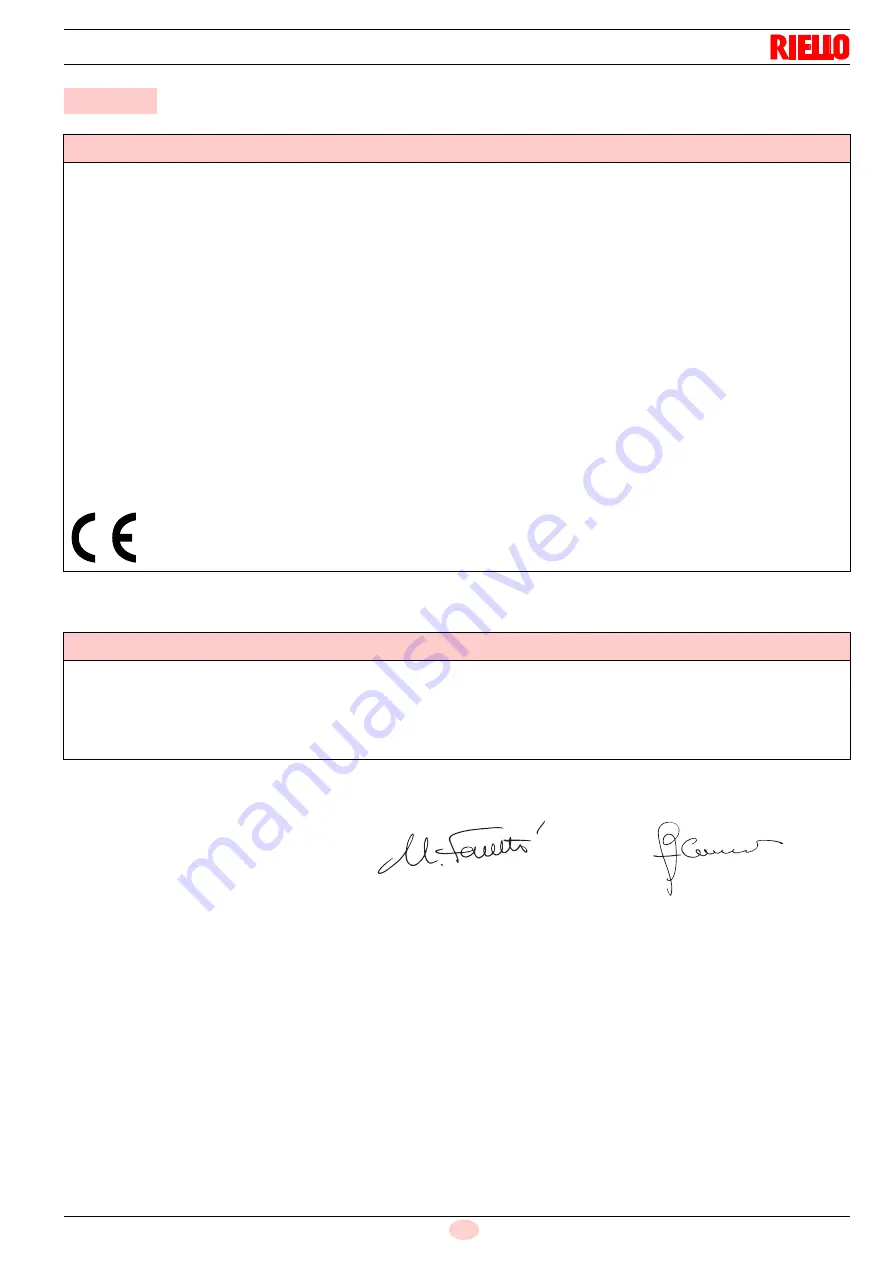
3
20145860
GB
Declarations
1
Declarations
Declaration of conformity in accordance with ISO / IEC 17050-1
Manufacturer:
RIELLO S.p.A.
Address:
Via Pilade Riello, 7
37045 Legnago (VR)
Product:
Forced draught gas burners
Model:
RS 1000/M BLU
RS 1200/M BLU
These products are in compliance with the following Technical Standards:
EN 676
EN 12100
and according to the European Directives:
GAR
2016/426/EU
Gas Appliances Regulation
MD
2006/42/EC
Machine Directive
LVD
2014/35/EU
Low Voltage Directive
EMC
2014/30/EU
Electromagnetic Compatibility
PED
2014/68/EU (
only FS2
)
Pressure Equipment Directive
Such products are marked as follows:
The quality is guaranteed by a quality and management system certified in accordance with ISO 9001:2015.
Manufacturer's Declaration
RIELLO S.p.A.
declares that the following products comply with the NOx emission limits specified by German standard
“
1. BImSchV revision 26.01.2010
”.
Product
Type Model
Output
Forced draught gas burners
1133 T
RS 1000/M BLU
1100 - 10100 kW
1134 T
RS 1200/M BLU
1500 - 11100 kW
Legnago, 21.04.2018
Executive General Manager
RIELLO S.p.A. - Burner Department
Research & Development Director
RIELLO S.p.A. - Burner Department
Mr. U. Ferretti
Mr. F. Comencini
RS 1000/M BLU
CE-0085CN0119
Class 3 (EN 676)
RS 1200/M BLU
CE-0085CN0120
Class 3 (EN 676)
Summary of Contents for RS 1000/M BLU
Page 2: ...Translation of the original instructions ...
Page 45: ...43 20145860 GB Appendix Electrical panel layout ...
Page 46: ...20145860 44 GB Appendix Electrical panel layout 0 0 1 0 0 0 0 0 2 2 2 0 0 0 ...
Page 47: ...45 20145860 GB Appendix Electrical panel layout 0 1 2 2 2 0 ...
Page 52: ...20145860 50 GB Appendix Electrical panel layout 0 12 3 4 5 4 5 6 7 8 9 8 9 0 0 0 0 ...