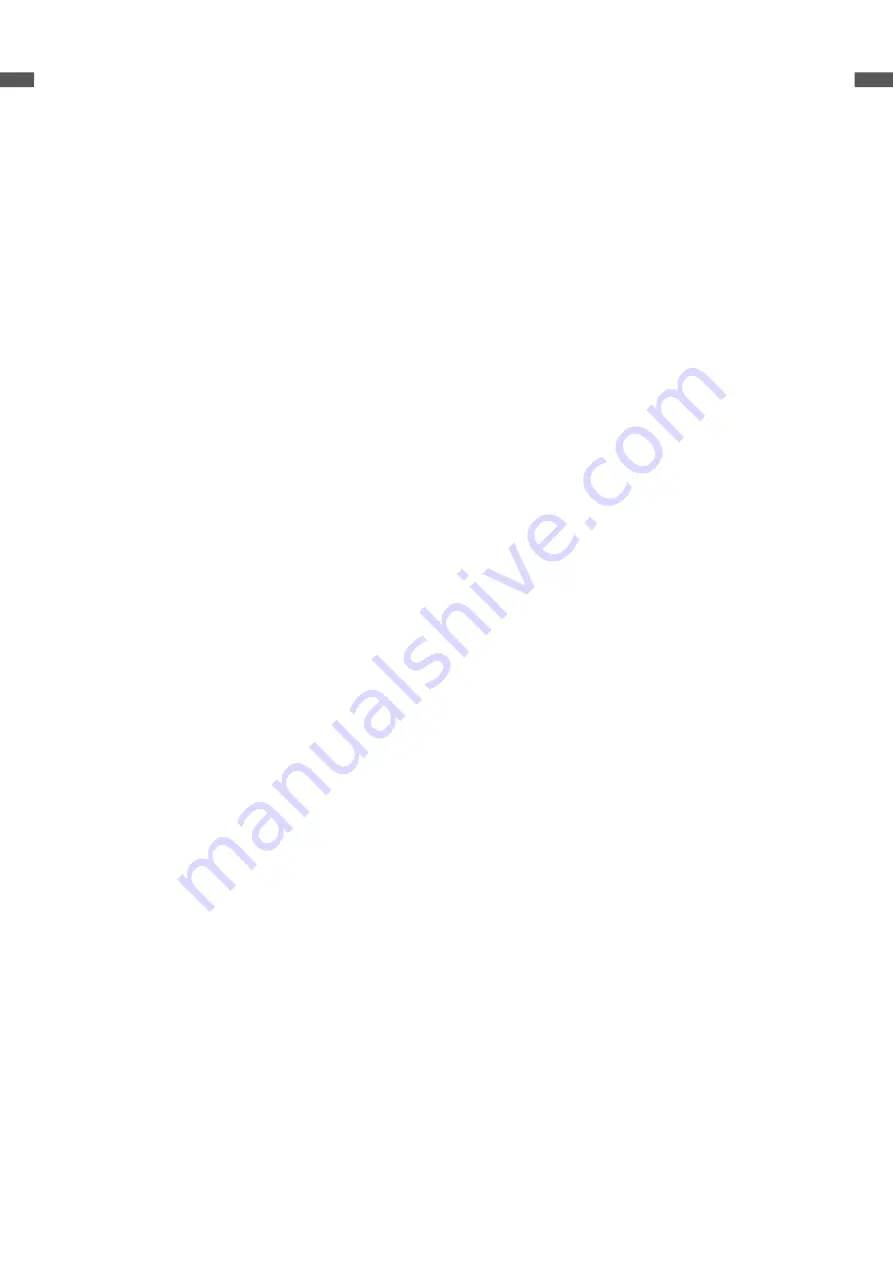
21
Condexa Pro
DESCRIPTION FOR SPECIFICATIONS
Condexa PRO is a pre-mixed condensing thermal module, consisting of a modulating thermal element.
It is available in 3 models, starting from 45 kW up to 97 kW.
The optimal combustion management allows high efficiency up to over 109%, value calculated on the PCI, in the condensation regime,
and low polluting emissions - Class 6 according to UNI EN 15502-1.
Condexa PRO boiler can be connected in cascade up to a maximum power of 970 MW.
The main technical features of the appliance are:
•
Premixing burner with constant air-gas ratio;
•
Heat exchanger with patented geometries, consisting of two smooth concentric stainless steel tubes, each having a pentagonal sec-
tion inside and a circular outside, designed to maximize the exchange surface, offer maximum corrosion resistance and the possibility
of working with high
Δ
T (up to 40°C) reducing set-up times;
•
Module power from 45 up to 97 kW, with possible cascades of modules with the same power
•
Maximum fumes outlet temperature 100°C;
•
Microprocessor management and control with self-diagnosis shown through display and recording of the main errors;
•
Anti-freeze function;
•
External probe that enables climatic operation (accessory);
•
Condensate drain syphon to avoid backflow of exhaust fumes into the environment (supplied with the boiler as standard);
•
Predisposition for room thermostat/heat request on high and low temperature zones;
•
Possibility to manage both a heating circuit and a circuit for the production of domestic hot water with storage;
•
High efficiency and high residual head circulator for each model;
•
IPX4D protection degree (for indoor installation);
•
Sealed chamber as standard.
SAFETY DEVICES
All the functions of the device are electronically controlled by the motherboard approved to perform safety functions by means of a dual
processor technology. Any anomaly causes the appliance stop and the gas valve automatic shutdown.
The following are installed on the water circuit:
•
Safety thermostat;
•
Flowmeter capable of checking continuously the flow rate of the primary circuit and causing the appliance stop in case of insufficient
flow;
•
Temperature probes on the flow and return that continuously measure the temperature difference between the flow and return fluid
and allow the control to intervene;
•
Minimum pressure switch.
The following are installed on the combustion circuit:
•
Gas solenoid valve in class B + C, with pneumatic compensation of the gas flow according to the suction air flow rate;
•
Ionization electrode for detection;
•
Flue temperature probe;
•
Smoke-exhaust flue non-return valve to avoid backflow in central heating (accessory for 50 P model, standard for other models).
The triggering of safety devices indicates the malfunction of a potentially hazardous thermal module. Therefore, contact Technical Assi-
stance Service immediately. After a brief pause, it is possible to try and restart the appliance (see Paragraph "Initial startup").
Safety devices must be replaced by Technical Assistance Service, using only original parts. Refer to the spare parts catalogue supplied
with the appliance. After making the repair, check that the appliance is working properly.
The appliance must not be put in service, even temporarily, when tampered safety devices are not in operation or have been tampered
with.
The Condexa PRO thermal modules comply with:
•
Regulation (EU) 2016/426
•
Directive 92/42/EEC on efficiency requirements and Annex E and Pres. Republic Decree n. 412, 26 August 1993 (****)
•
Electromagnetic Compatibility Directive 2014/30/EU
•
Low Voltage Directive 2014/35/EU
•
Ecodesign Directive 2009/125/CE for energy-related products
•
Regulation (EU) 2017/1369 Energy labelling
•
Delegated Regulation (EU) No. 811/2013;
•
Delegated Regulation (EU) No. 813/2013;
•
Standard for gas-fired heating boilers - General requirements and tests - EN 15502-1
•
Specific standard for type C appliances and type B2, B3 and B5 appliances of nominal heat input not exceeding 1000 kW - EN 15502-2/1
•
SSIGA G1 gas directive
•
AICAA Fire regulations
•
CFST GPL directive part 2;
•
Various cantonal and communal provisions on air quality and energy saving.