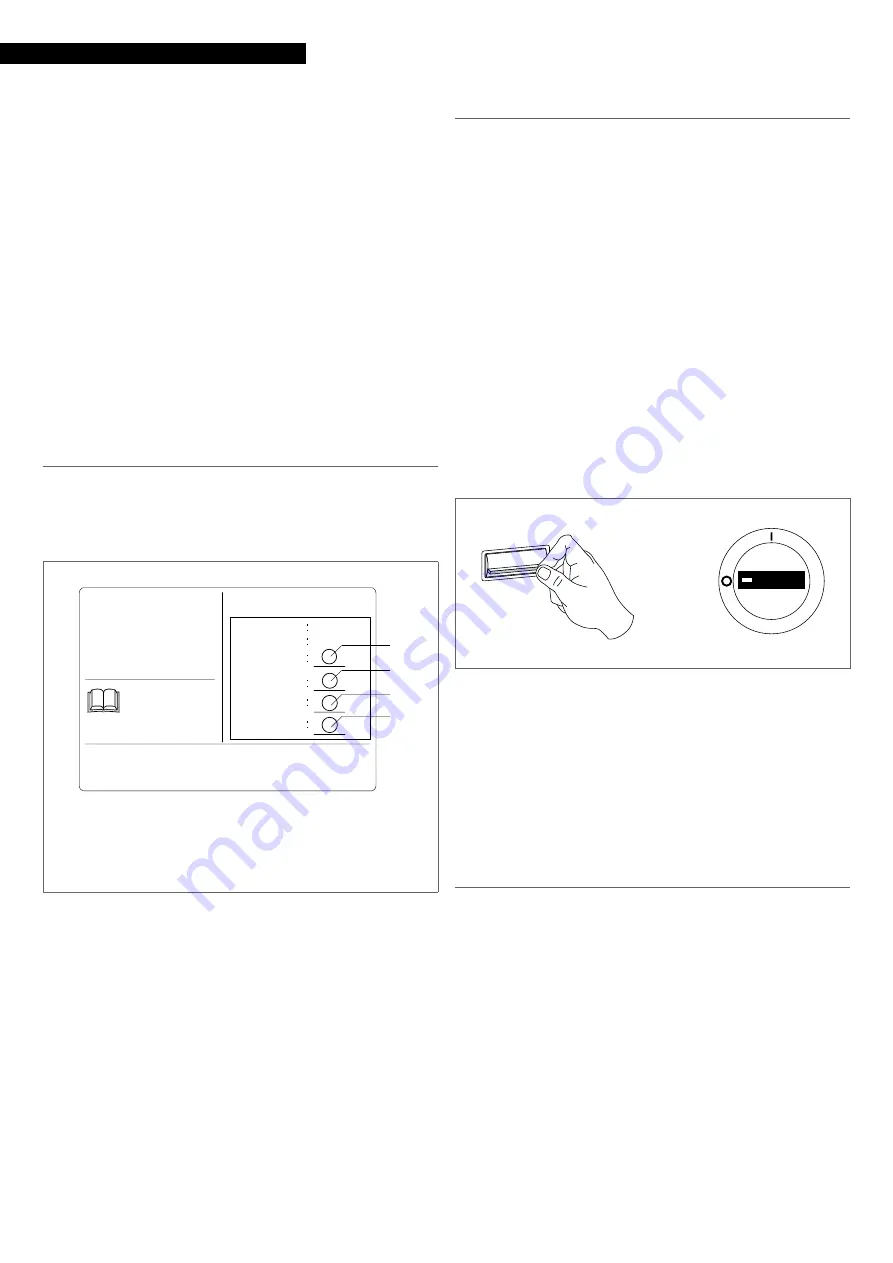
36
COMMISSIONING AND MAINtENANCE
9
Carefully check for absence of leakages from the closing
point of the plug.
9
Do not force beyond the stop point to prevent damaging the
shaft and causing leakage as a consequence.
9
Use equipment suitable for the system refrigerant.
9
Use only the system refrigerant.
9
Any gas leaks indoors can generate toxic gases if they come
into contact with naked flames or high temperature bodies,
in case of leaks, please air the rooms thoroughly.
9
Take anti-static precautions in case of weather conditions
where humidity is less than 40%.
9
Avoid using mobile phones.
9
3.2.1
Refrigerant label
In base alla Normativa CE n. 517/2014 su determinati gas floru-
rati ad effetto serra, è obbligatorio indicare la quantità totale
di refrigerante presente sistema installato. Tale informazione è
presente nella targhetta tecnica presente nell'unità esterna.
A
Standard charge
B
Additional charge
C
Total charge
D
Equivalent total weight of CO2
QUESTO APPARECCHIO CONTIENE
GAS AD EFFETTO SERRA COPERTI
DAL PROTOCOLLO DI KYOTO.
INFORMAZIONI SUL REFRIGERANTE
Refrigerante
Carica addizionale
Carica totale
Carica di fabbrica
(vedi etichetta tecnica)
É VIETATO DISPERDERE
IL GAS R32 DIRETTAMENTE
IN ATMOSFERA
Istruzioni per compilare l’Etichetta “F-Gas Label”:
1 - Annotare le quantità sull’etichetta con inchiostro indelebile
2 - Collocare l’adesivo plastico di protezione (consegnato assieme al manuale)
3 - Peso equivalente CO2 del sistema in tonnellate = Carica totale in kg / 1000 x GWP
GW
P
675
R32
A
B
C
D
Peso equivalente CO2
kg
kg
kg
t
To write the tag:
—
note the quantity onto the label with indelible ink
—
place the refrigerant gas label on the outdoor unit
9
This unit contains fluorinated greenhouse gases covered
by the Kyoto protocol. Maintenance and disposal activities
must be carried out exclusively by skilled personnel.
9
Global warming potential of the R32 refrigerant gas: GWP=675
9
If necessary, the refrigerant must be recovered and not di-
spersed into the environment.
0
It is forbidden to disperse the refrigerant into the environ-
ment.
0
3.3
Ordinary maintenance
Routine maintenance is fundamental for keeping the equip-
ment efficient, safe and reliable. It can be performed periodi-
cally by the Technical Support Service, whose staff is technically
qualified and can use genuine spare parts, if necessary.
9
For units installed in a seaside environment, the mainte-
nance intervals shall be halved.
9
Original conditions must be restored after performing the
required maintenance operations.
9
All described operations MUST be carried out under the fol-
lowing conditions:
—
cold device
—
device NOT supplied with electric power
—
suitable personal protection equipment
0
Do not open the access covers and carry out technical or
cleaning activities before disconnecting the unit from the
power grid by positioning the system's main switch in the
"OFF" position.
ON
OFF
—
position the system's main switch in the "OFF" position.
9
Wait 10 minutes before touching the device electric compo-
nents.
9
Check with a tester that the voltage between the power
supply connectors of the main electronic board is lower
than 10 Vdc.
9
Yearly operations
The annual maintenance plan includes the following checks:
—
power supply voltage
—
electric connection tightening
—
status of cooling and hydraulic joint
—
finned coil cleaning
—
electric absorption
—
fan grille cleaning
—
Cleaning the heat exchanger fins
The thermal exchange bank must be cleaned with compressed
air.
Cleaning must be carried out at least once a year, according to
the location of the unit, as dirt accumulating between the fins
narrows the passage section and reduces the exchange capa-
bility.
—
check the alignment of the bank's aluminium fins and, if
necessary, straighten them with the appropriate comb
Summary of Contents for 20153499
Page 29: ...29 Installation MODEL 1100 M ...
Page 31: ...31 Installation MODEL 1125 T 1140 T ...
Page 42: ......
Page 43: ......