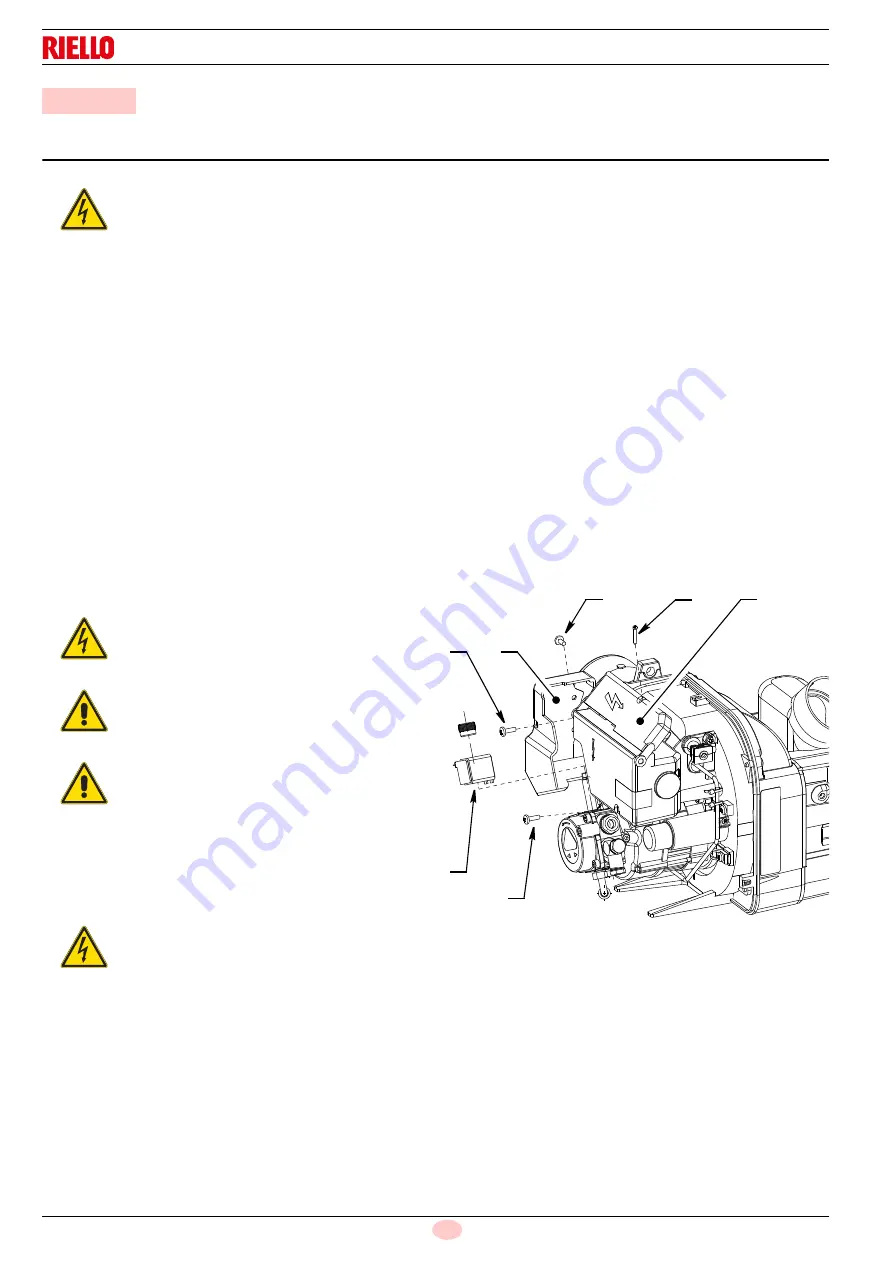
2903266
16
GB
Electrical system
7.1
Notes on safety for the electrical wiring
Before carrying out any maintenance, cleaning or checking oper-
ations:
If the cover is still present, remove it and proceed with the electri-
cal wiring according to the wiring diagrams.
Use flexible cables in compliance with the EN 60 335-1 standard.
7.1.1
Control box
To remove the control box (Fig. 13) from the burner follow of the
istruction:
Loosen the screw 1) and remove protection 6) of the electri-
cal connections and coil.
Loosen the screws 2), open the protection 3) and remove all
components.
Remove the coil 4) and loosen the two screws 5).
Move a little the control box and remove the high voltage
leads.
7
Electrical system
DANGER
The electrical wiring must be carried out with the electrical supply disconnected.
Electrical wiring must be carried out by qualified personnel and in compliance with the regulations currently in
force in the country of destination. Refer to the wiring diagrams.
The manufacturer declines all responsibility for modifications or connections different from those shown in the wir-
ing diagrams.
Do not invert the neutral with the phase in the electrical supply line.
Check that the electrical supply of the burner corresponds to that shown on the identification label and in this man-
ual.
The burners have been set for intermittent operation. This means they should compulsorily be stopped at least
once every 24 hours to enable the control box to perform checks of its own start-up efficiency. Normally the
boiler's thermostat/pressure switch ensures the stopping of the burner.
If this is not the case, it is necessary to apply in series with L-N a timer switch that turns off the burner at least
once every twenty-four hours. Refer to the wiring diagrams.
The electrical safety of the device is obtained only when it is correctly connected to an efficient earthing system,
made according to current standards. It is necessary to check this fundamental safety requirement. In the event of
doubt, have the electrical system checked by qualified personnel.
The electrical system must be suitable for the maximum input power of the device, as indicated in the manual,
checking in particular that the section of the cables is suitable for the input power of the device.
For the main power supply of the device from the electricity mains:
- do not use adapters, multiple sockets or extensions;
- use an omnipolar switch, as indicated by the current safety standards.
Do not touch the device with wet or damp body parts and/or in bare feet.
Do not pull the electric cables.
DANGER
Disconnect the electrical supply from the burner
by means of the main system switch.
DANGER
Turn off the fuel interception tap.
DANGER
Avoid condensate, ice and water leaks from form-
ing.
DANGER
This operation must be performed with the burner
turned off and mains power disconnected.
D7358
5
5
4
1
3
2
6
Fig. 13
Summary of Contents for 20015255
Page 2: ...Original instructions...