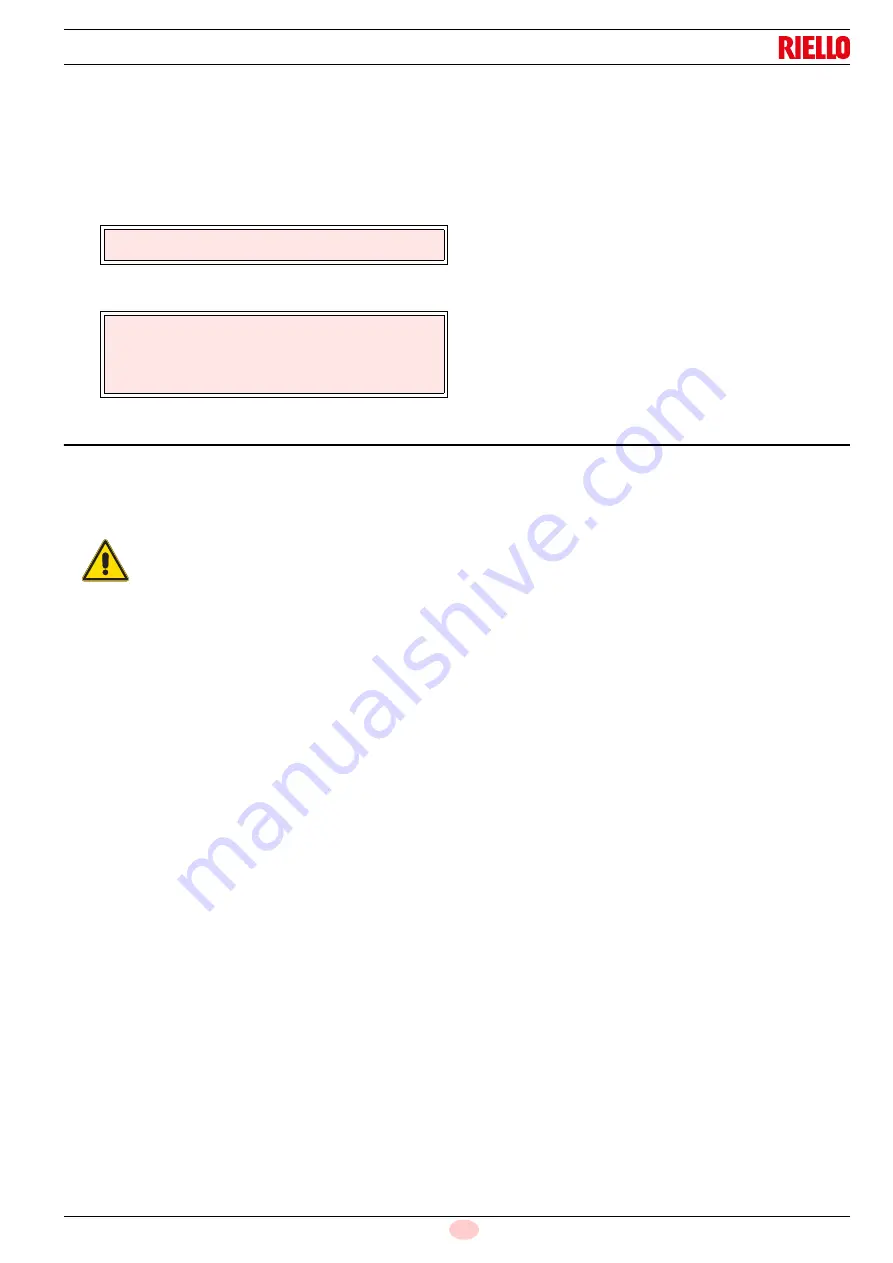
5
2903266
GB
Information and general warnings
2.1.4
Delivery of the system and the instruction
manual
When the system is delivered, it is important that:
the instruction manual is delivered to the user by the system
manufacturer, with the recommendation to keep it in the
room where the heat generator is to be installed.
The instruction manual shows:
– the serial number of the burner;
– the address and telephone number of the nearest Assis-
tance Centre
The system supplier must carefully inform the user about:
– the use of the system;
– any further tests that may be required before activating the
system;
– maintenance, and the need to have the system checked at
least once a year by a representative of the manufacturer
or another specialised technician.
To ensure a periodic check, the manufacturer recom-
mends the drawing up of a Maintenance Contract.
2.2
Guarantee and responsibility
The manufacturer guarantees its new products from the installa-
tion date, in accordance with the regulations in force and/or the
sales contract. At the moment of the first start-up, check that the
burner is integral and complete.
In particular, the rights to the guarantee and the responsibility will
no longer be valid, in the event of damage to things or injury to
people, if such damage/injury was due to any of the following
causes:
incorrect installation, start-up, use and maintenance of the
burner;
improper, incorrect or unreasonable use of the burner;
intervention of unqualified personnel;
carrying out of unauthorised modifications on the equipment;
use of the burner with safety devices that are faulty, incor-
rectly applied and/or not working;
installation of untested supplementary components on the
burner;
powering of the burner with unsuitable fuels;
faults in the fuel supply system;
continuation of use of the burner when a fault has occured;
repairs and/or overhauls incorrectly carried out;
modification of the combustion chamber with inserts that
prevent the regular development of the structurally estab-
lished flame;
insufficient and inappropriate surveillance and care of those
burner components most likely to be subject to wear and
tear;
the use of non-original components, including spare parts,
kits, accessories and optional;
force majeure.
The manufacturer furthermore declines any and every re-
sponsibility for the failure to observe the contents of this
manual.
Riello warranty is subject to correct burner, appliance and appli-
cation matching, and set up in line with Riello's instructions and
guidelines. All components within the hydraulic circuit suitable for
bio fuel use and supplied by Riello will be identified as Bio com-
patible. No warranty is given in relation to the use of components
which are not so identified with bio fuel blends. If in any doubt
please contact Riello for further advice.
If any Riello burners are used with fuel with a bio content >10%
then the components within the hydraulic circuit maybe affected
and are not covered under warranty.
The hydraulic circuit consists of:
– Pump
– Hydraulic ram (where applicable)
– Valve block
– Flexible oil lines (considered as a consumable component)
1
Irrespective of any warranty given by Riello in relation to
normal use and manufacturing defects, when fuels not
meeting the relevant standards are used, or where fuel
storage issues have not been addressed correctly, or the
equipment used is not compatible, if failures occur which
are directly or indirectly attributed to such issues and/or to
the non-observance of this guidance, then no warranty or
liability is implied or accepted by Riello.
2
Riello have carefully chosen the specification of the bio
compatible components including the flexible oil lines to
protect the pump, safety value and nozzle. The Riello war-
ranty is dependent upon the use of Riello genuine compo-
nents including the oil lines, being used.
3
Riello warranty does not cover defects arising from incor-
rect commissioning or servicing by non Riello employed
service engineers, and any issues impacting the burner
arising from external site related issues.
.........................................................................................
.........................................................................................
.........................................................................................
.........................................................................................
WARNING
Failure to observe the information given in this
manual, operating negligence, incorrect installa-
tion and carrying out of non authorised modifica-
tions will result in the annulment by the
manufacturer of the guarantee that it supplies with
the burner.
Summary of Contents for 20015255
Page 2: ...Original instructions...