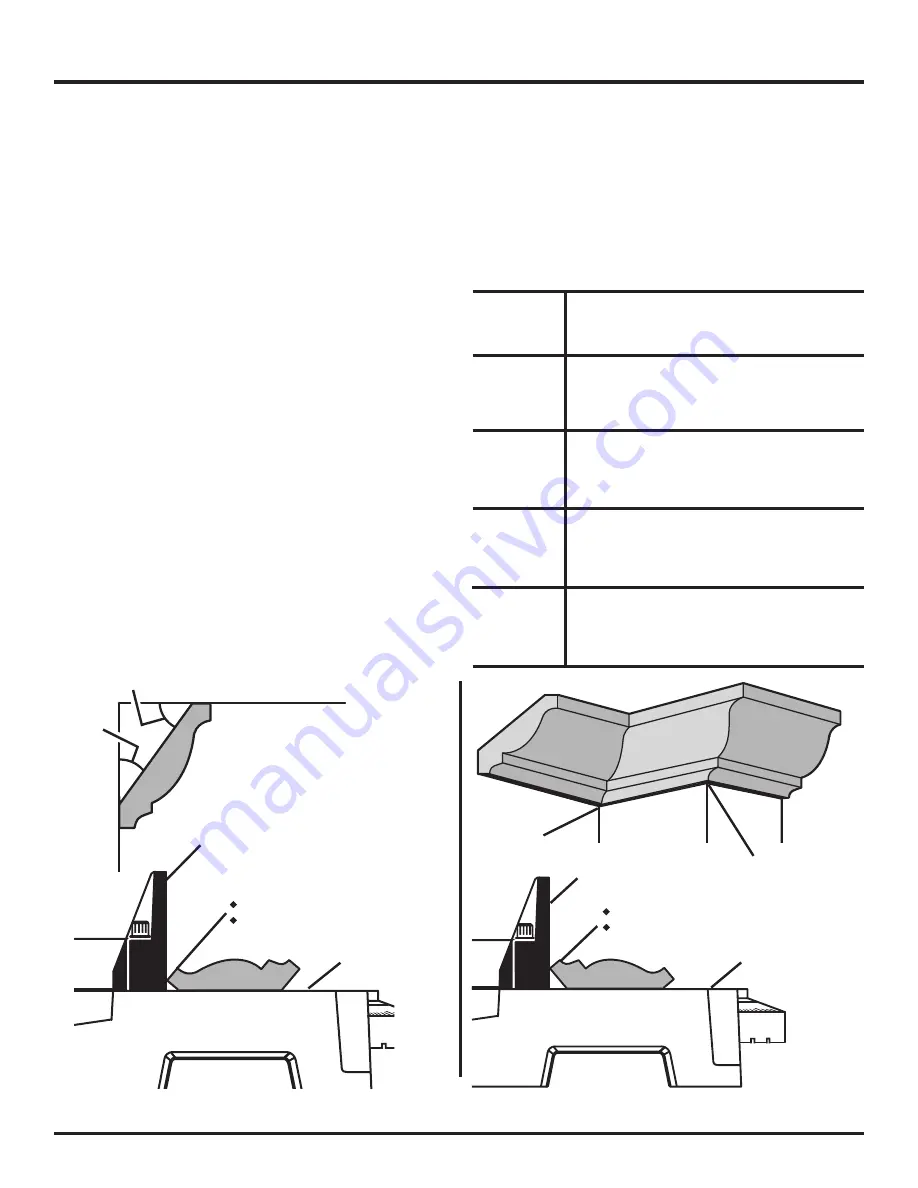
26
When cutting crown molding by this method the bevel angle
should be set at 33.9°. The bevel stop turret can be used to
set the bevel angle to 33.9°. The miter angle should be set
at 31.6° either right or left, depending on the desired cut for
the application. See the chart below for correct angle settings
and correct positioning of crown molding on miter table.
The settings in the chart below can be used for cutting All
Standard (U.S.) crown molding with 52° and 38°
angles. The
crown molding is placed flat on the miter table using the
compound features of your miter saw.
CEILING
W
A
L
L
INSIDE
CORNER
CROWN MOLDING FLAT ON MITER TABLE
38°
52°
MITER TABLE
BOTTOM EDGE AGAINST FENCE =
RIGHT SIDE, INSIDE CORNER
LEFT SIDE, OUTSIDE CORNER
MITER TABLE
Fig. 31
OUTSIDE CORNER
TOP EDGE AGAINST FENCE =
LEFT SIDE, INSIDE CORNER
RIGHT SIDE, OUTSIDE CORNER
CUTTING CROWN MOLDING
Your compound miter saw does an excellent job of cutting
crown molding. In general, compound miter saws do a bet-
ter job of cutting crown molding than any other tool made.
In order to fit properly, crown molding must be compound
mitered with extreme accuracy.
The two contact surfaces on a piece of crown molding that
fit flat against the ceiling and the wall of a room are at angles
that, when added together, equal exactly 90°. Most crown
molding has a top rear angle (the section that fits flat against
the ceiling) of 52° and a bottom rear angle (the section that
fits flat against the wall) of 38°.
LAYING MOLDING FLAT ON THE MITER
TABLE
See Figure 31.
To use this method for accurately cutting crown molding for
a 90° inside or outside corner, lay the molding with its broad
back surface flat on the miter table and against the fence.
When setting the bevel and miter angles for compound mi-
ters, remember that the settings are interdependent; chang-
ing one angle changes the other angle as well.
Keep in mind that the angles for crown moldings are very
precise and difficult to set. Since it is very easy for these
angles to shift, all settings should first be tested on scrap
molding. Also most walls do not have angles of exactly 90°,
therefore, you will need to fine tune your settings.
OPERATION
Bevel
Angle
Type of Cut
Setting
Left side, inside corner
1. Top edge of molding against fence
2. Miter table set right 31.6°
3. Save left end of cut
Right side, inside corner
1. Bottom edge of molding against fence
2. Miter table set left 31.6°
3. Save left end of cut
Left side, outside corner
1. Bottom edge of molding against fence
2. Miter table set left 31.6°
3. Save right end of cut
Right side, outside corner
1. Top edge of molding against fence
2. Miter table set right 31.6°
3. Save right end of cut
33.9°
33.9°
33.9°
33.9°
SLIDING
MITER FENCE
SLIDING
MITER FENCE