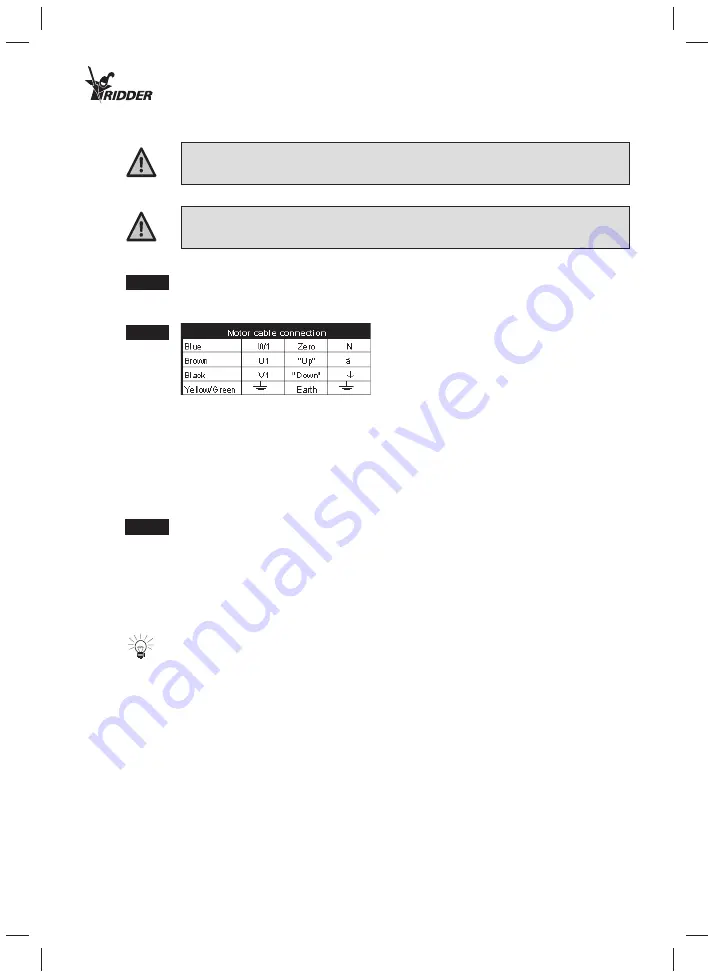
Ridder Drive Systems BV HARDERWIJK NEDERLAND Tel.: +31 (0)341-416 854
Fax: +31 (0)341 416 611
RB50
/ 0505
19
Tube motor: electrical installation.
Motor cable connection.
The connection cable is a 4-core cable belonging to the 2-pole asynchronous (condensor) motor.
This allows the motor to rotate to both the left and the right.
Run-time protection.
When the tube motor is used in an automatic system it needs a run-time protection safety. This
ensures that the motor will switch off after a specific time in the event of it not being stopped
by its limit switches. The purpose of the run-time protection is to stop the tube motor from over-
heating which could be possibly result in its burning out. The theoretical maximum running time
of a tube motor is indicated in KB.
Parallel connection of the tube motor.
Tube motors must never be connected directly in parallel. If this were to happen then the motor
that first reached its end switch would be powered into reverse by inductive and capacitive
charge that would come from the tube motor that is still running. This charge, that can run as
high as 1000 volts, re-starts the motor that had already stopped, by moving in the opposite posi-
tion until the motor receives mains supply from the now re-connected end switch. In this way a
pendulum action builds up with the tube motor that had already stalled, which would continue
until the end switch was damaged by the enormous load.
The tube motor can only be installed in parallel when the power supply is separate to the mains
supply.
THE CONNECTION OR INSTALLATION OF ELECTRONIC COMPONENTS MAY ONLY BE
MADE BY A QUALIFIED ELECTRO-TECHNICIAN!
TUBE MOTORS MUST NEVER BE CONNECTED IN PARALLEL!
Fig. 9
Fig. 9
Fig. 8
Fig. 8
Fig. 10
Fig. 10