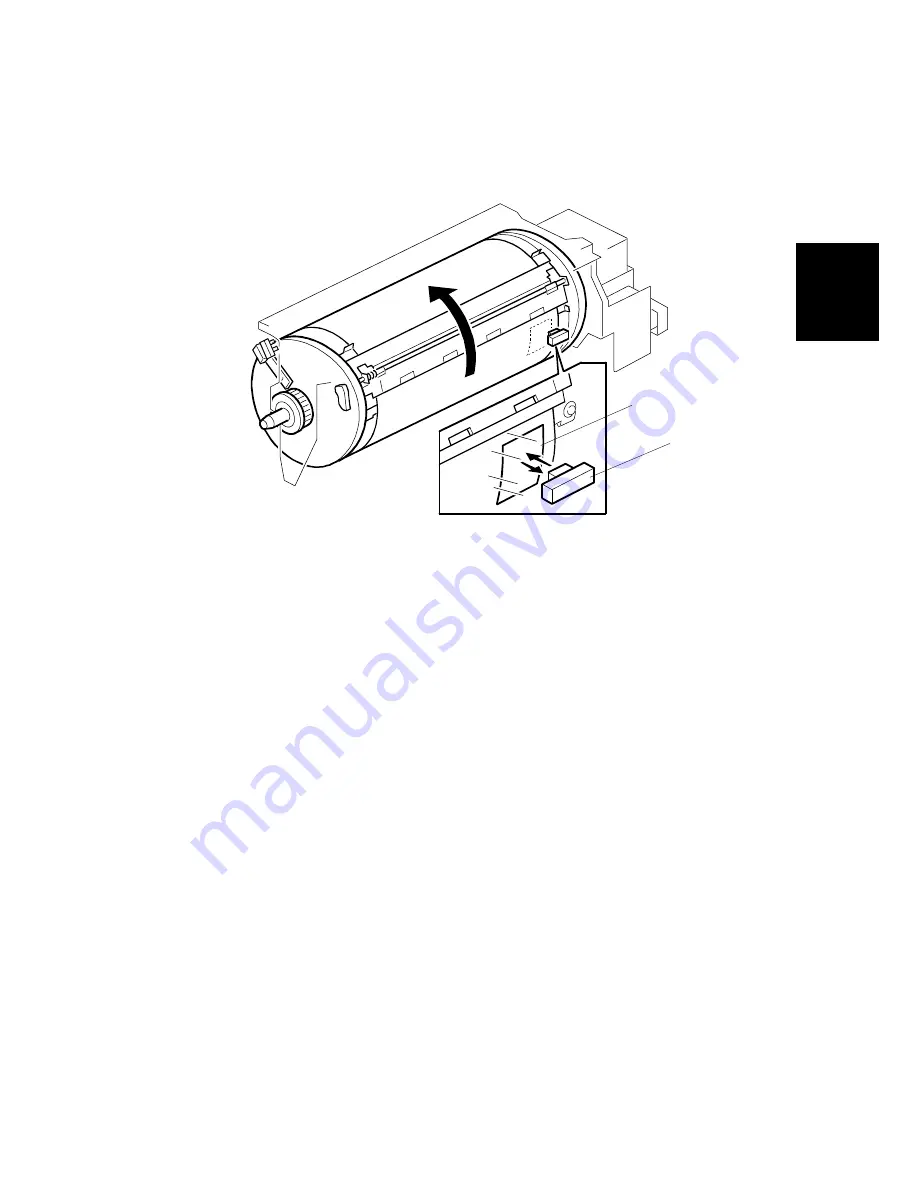
DRUM
2-33
SM
C231
Det
a
iled
Sect
io
n
De
s
c
ri
ptions
2.5.6 DETECTION OF MASTERS ON THE DRUM
The drum master sensor [B] detects whether a master is on the drum.
When there is a master on the drum, the black patch [A] is covered and the sensor
detects the light reflected from the master. Printing starts when the start key is
pressed. (If a new original is set, the master ejecting cycle is performed before
making a new master.)
When there is no master on the drum, the black patch [A] is exposed. The black
patch does not reflect light back to the sensor. Because of this, the master eject
process is skipped when a new master is made.
C231D571.WMF
[A]
[B]
Summary of Contents for Aficio SP C231
Page 1: ...SERVICE MANUAL PN RCSMC231 C231 RICOH GROUP COMPANIES...
Page 2: ......
Page 3: ...SERVICE MANUAL C231 RICOH GROUP COMPANIES...
Page 4: ......
Page 5: ...C231 SERVICE MANUAL PN RCSMC231...
Page 6: ......
Page 8: ......
Page 10: ......
Page 20: ......
Page 21: ...OVERALL INFORMATION...
Page 39: ......
Page 40: ...DETAILED SECTION DESCRIPTIONS...
Page 91: ...INSTALLATION...
Page 92: ......
Page 111: ...SERVICE TABLES...
Page 112: ......
Page 142: ......
Page 143: ...PREVENTIVE MAINTENANCE...
Page 146: ...REPLACEMENT AND ADJUSTMENT...
Page 147: ......
Page 165: ...MASTER FEED SECTION 6 18 C231 SM A Master making unit 2 screws C231R522 WMF A...
Page 202: ...TAPE MARKER C532...
Page 203: ......
Page 211: ......
Page 212: ...PCRIP EZ1 GDI QuickDraw Priport Controller User s Guide...
Page 213: ......
Page 215: ......
Page 217: ......
Page 244: ......
Page 245: ...TECHNICAL SERVICE BULLETINS...