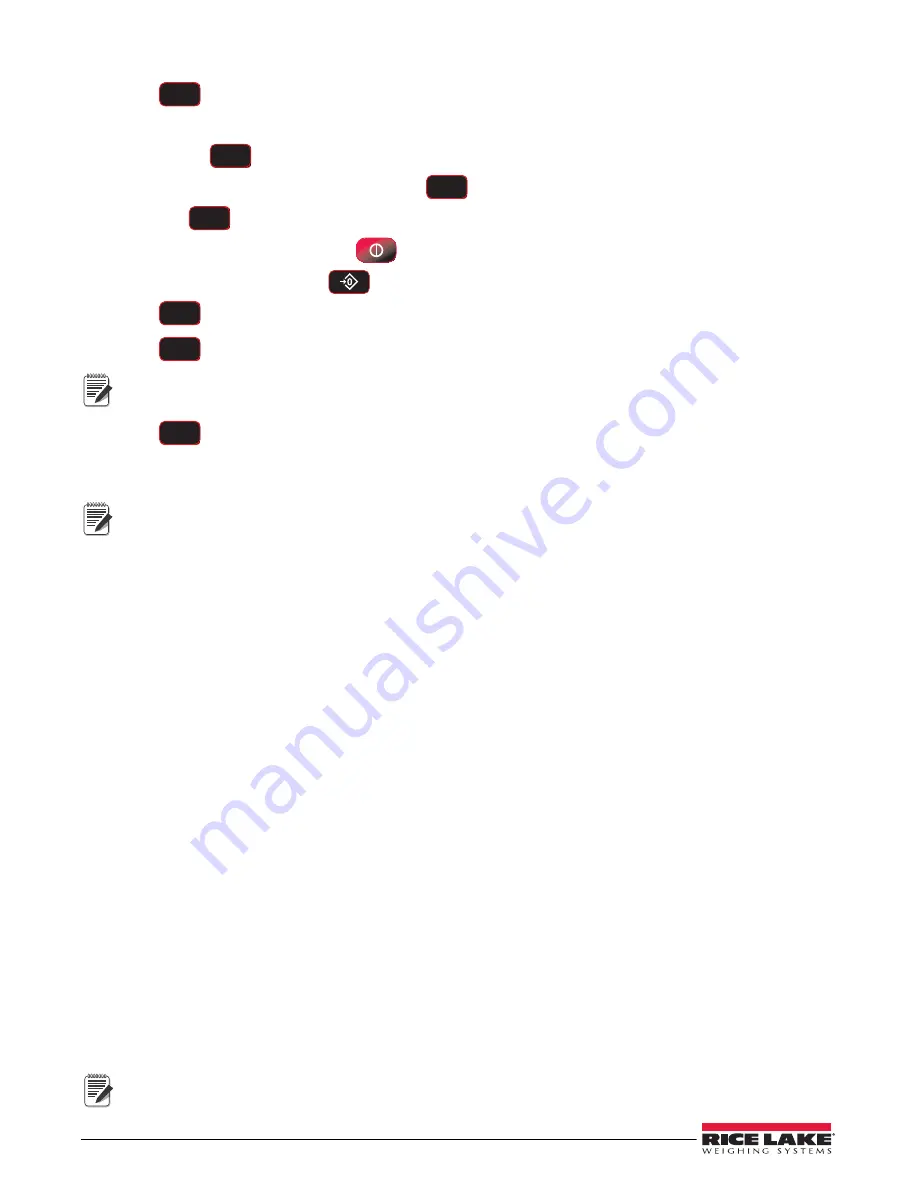
Note
Note
18
MSI-7300 Dyna-Link 2 Technical Manual
7. Press
. The current capacity is displayed.
8. Enter a different capacity by:
• Pressing
to move the cursor position and change the number.
• With the desired number displayed, press
to save the number.
• Press
to move the cursor to the next position.
• To enter a decimal point, press
, the decimal point will be entered after last number displayed.
• To correct a number, press
to go back to the number that needs to be corrected.
9. Press .
displays. The current scale division size is displayed.
10. Press
to scroll through options until the desired division size is displayed.
The first selection is the standard division for the current capacity. Setting the division to a size that results in
a total resolution higher than 1:5000 is not recommended for stability reasons.
11. Press .
displays.
12. Follow the Standard Calibration procedure to complete calibration. See Section 5.1 on page 16 starting at step
2.
For large capacity Dyna-Link 2’s, enter the capacity in weight X1000 and push the POWER key twice. X1000
mode is indicated by the M annunciator during data entry.
For the 100,000 lb unit, enter 100 and press the POWER key twice so the M annunciator is on.
5.2.1
Guidelines for Capacity and Resolution
The
Dyna-Link 2
is subject to forces that static scales do not experience. Many bridge cranes, hoist cranes, and
mobile cranes lack rigidity and tend to bounce or swing when loads are lifted. For this reason, MSI recommends
that resolution is kept in the 1:2000 to 1:3000 range. Some improvement in stability can be achieved by increasing
the filtering. Never program resolution that is far greater than needed. The resolution should never be set higher
than 1:5000 due to temperature and noise considerations common to all strain gage based load cells.
If the
Dyna-Link 2
display doesn’t stabilize, reduce the resolution and increase the filtering.
The tension must be stable for certain features to work:
• ZERO tension must be stable to be zeroed.
• TARE tension must be stable to be tared.
• TOTAL tension must be stable to be added to the total registers.
One way to improve the stability is to increase the filtering, at the risk of increasing settling time.
The other is to increase the ‘d’ (reduce resolution).
The third way is to increase the motion window. The
Dyna-Link 2
defaults to ±1d as a motion window. It can be
changed at MSI to a higher value if desired. Often ±3 d is chosen for bridge cranes as these tend to have a lot of
bounce to them. This of course carries an accuracy penalty adding ±3 d to the total accuracy of the
Dyna-Link 2
if
the zero or tare operation happens to capture the tension in a valley or peak.
Setting capacity is dictated primarily by the capability of the load cell. The
Dyna-Link 2
is available in a variety of
capacities. Never set the capacity of the
Dyna-Link 2
higher than the rating of the load cell. Due to the excellent
linearity of the Link load cell, it is acceptable to set lower capacities to better match the crane the
Dyna-Link 2
is
used on. For example, if the hoist is rated for 9000 lb, a 10000 lb capacity
Dyna-Link 2
can be used and the
capacity reset to 9000 lb so that the
Dyna-Link 2
will indicate overload at 9000 lb instead of 100000 lb. Derating as
much as 50% of the capacity is usually acceptable, but the
Dyna-Link 2
may be less stable if the ‘d’ is decreased
(resolution increased).
Note
The capacity of all the Dyna-Link 2 systems is rated approximately 20% higher than the rated capacity in
pounds. This is to allow the kg capacity to be exactly 1/2 the number of the pounds capacity.
F1
F2
F1
F2
F1
F2
F1