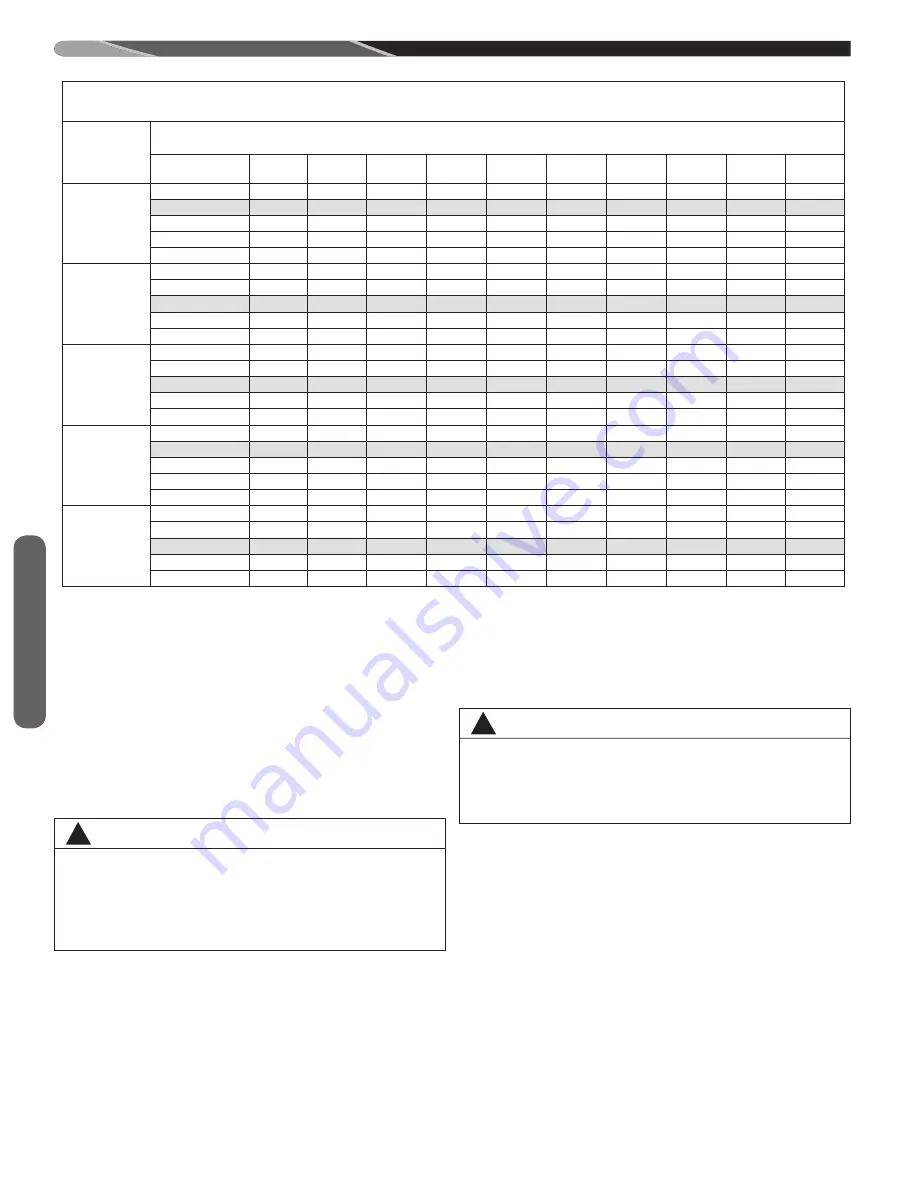
46
BLOWER SPEED SELECTIONS
The UT Electronic Controls control boards have four quick con-
nect terminals for connecting the motor speed leads . These are:
1 . FAN SPEED* — motor runs on this speed when the thermo-
stat is in the “FAN” position .
2 . COOL — connect desired cooling speed .
3 . HEAT — connect desired heating speed .
4 . HEAT/COOL* — connect desired speed when heating and
cooling speed are the same .
See Table 10 for instructions for setting the blower “OFF” timings .
GAS FURNACE (DIRECT DRIVE)
INSTRUCTIONS FOR CHANGING
BLOWER SPEED
The blower motor is wired for blower speeds required for normal
operation as shown .
If additional blower speed taps are available (leads connected
to “M1” and “M2” on the electronic control), speeds may be
changed if necessary to fit requirements of the particular installa-
tion . Reconnect the unused motor leads to “M1” or “M2 .” Check
motor lead color for speed designation .
Heating speeds should not be reduced where it could cause the
furnace air temperature to rise to exceed the maximum outlet air
temperature specified for the unit .
!
CAUTION
DO NOT CONNECT ANY MOTOR SPEEDS TO “HEAT”
OR “COOL” IF YOU USE THE “HEAT/COOL” TERMINAL .
DOING SO WILL DAMAGE THE BLOWER MOTOR . UN-
USED MOTOR WIRE TAPS MUST BE CONNECTED TO
PARKING TERMINALS M1 AND M2 OF THE IFC, OR PROP-
ERLY INSULATED .
!
WARNING
DISCONNECT THE ELECTRICAL SUPPLY TO THE FUR-
NACE BEFORE ATTEMPTING TO CHANGE THE BLOWER
SPEED . FAILURE TO DO SO CAN CAUSE ELECTRICAL
SHOCK RESULTING IN SEVERE PERSONAL INJURY OR
DEATH .
Airflow
NOTE: Shaded data is factory heating tap.
TABLE 12
AIR FLOW PERFORMANCE – (-)801T/(-)801C, (-)80MSX/(-)80MSC, FF(-)TS80(-)/FF(-)CS80(-) - SERIES MODELS
Input (Btu)
Cabinet Width (in)
CFM AIR DELIVERY
EXTERNAL STATIC PRESSURE in INCHES OF W.C.
AIRFLOW CONTROL
SETTINGS
SPEED TAP
0.1
0.2
0.3
0.4
0.5
0.6
0.7
0.8
0.9
50k
14”
CIRC FAN
LOW
894
775
655
595
533
496
462
423
357
HEAT OR HEAT/COOL
MED. LO
971
912
875
839
804
758
713
684
644
COOL
MEDIUM
1117
1081
1051
1024
995
973
938
908
878
COOL
MED. HIGH
1326
1291
1275
1240
1204
1171
1144
1114
1077
COOL
HIGH
1440
1432
1405
1382
1353
1322
1305
1272
1251
75k
17”
CIRC FAN
LOW
1054
1014
964
911
860
797
711
657
606
COOL
MED. LO
1363
1318
1275
1230
1189
1129
1091
1053
1012
HEAT OR HEAT/COOL
MEDIUM
1447
1417
1366
1329
1288
1250
1215
1176
1137
COOL
MED. HIGH
1553
1521
1478
1444
1407
1372
1332
1295
1264
COOL
HIGH
1616
1574
1547
1508
1478
1438
1402
1375
1341
75k
21”
CIRC FAN
LOW
1176
1133
1095
1048
1000
951
908
861
810
COOL
MED. LO
1353
1312
1267
1236
1186
1149
1106
1079
1016
HEAT OR HEAT/COOL
MEDIUM
1400
1346
1307
1276
1225
1181
1145
1103
1069
COOL
MED. HIGH
1568
1537
1498
1468
1433
1399
1353
1320
1287
COOL
HIGH
1785
1775
1736
1704
1673
1629
1608
1573
1550
100k
21”
CIRC FAN
LOW
1277
1211
1164
1103
1035
967
861
800
740
HEAT OR HEAT/COOL
MED. LO
1556
1498
1456
1409
1353
1308
1254
1198
1125
COOL
MEDIUM
1644
1597
1554
1511
1463
1400
1358
1304
1253
COOL
MED. HIGH
1879
1842
1785
1729
1692
1674
1621
1579
1537
COOL
HIGH
2071
2025
1992
1948
1902
1872
1840
1795
1750
125k
24”
CIRC FAN
LOW
1398
1338
1278
1232
1177
1130
1041
975
909
COOL
MED. LO
1593
1546
1495
1454
1414
1342
1304
1251
1190
HEAT OR HEAT/COOL
MEDIUM
1878
1844
1807
1753
1714
1675
1634
1578
1536
COOL
MED. HIGH
2025
1967
1931
1886
1856
1812
1748
1721
1668
COOL
HIGH
2165
2124
2082
2047
2012
1973
1934
1894
1859
Summary of Contents for 801C Series
Page 52: ...52 CM 0917...