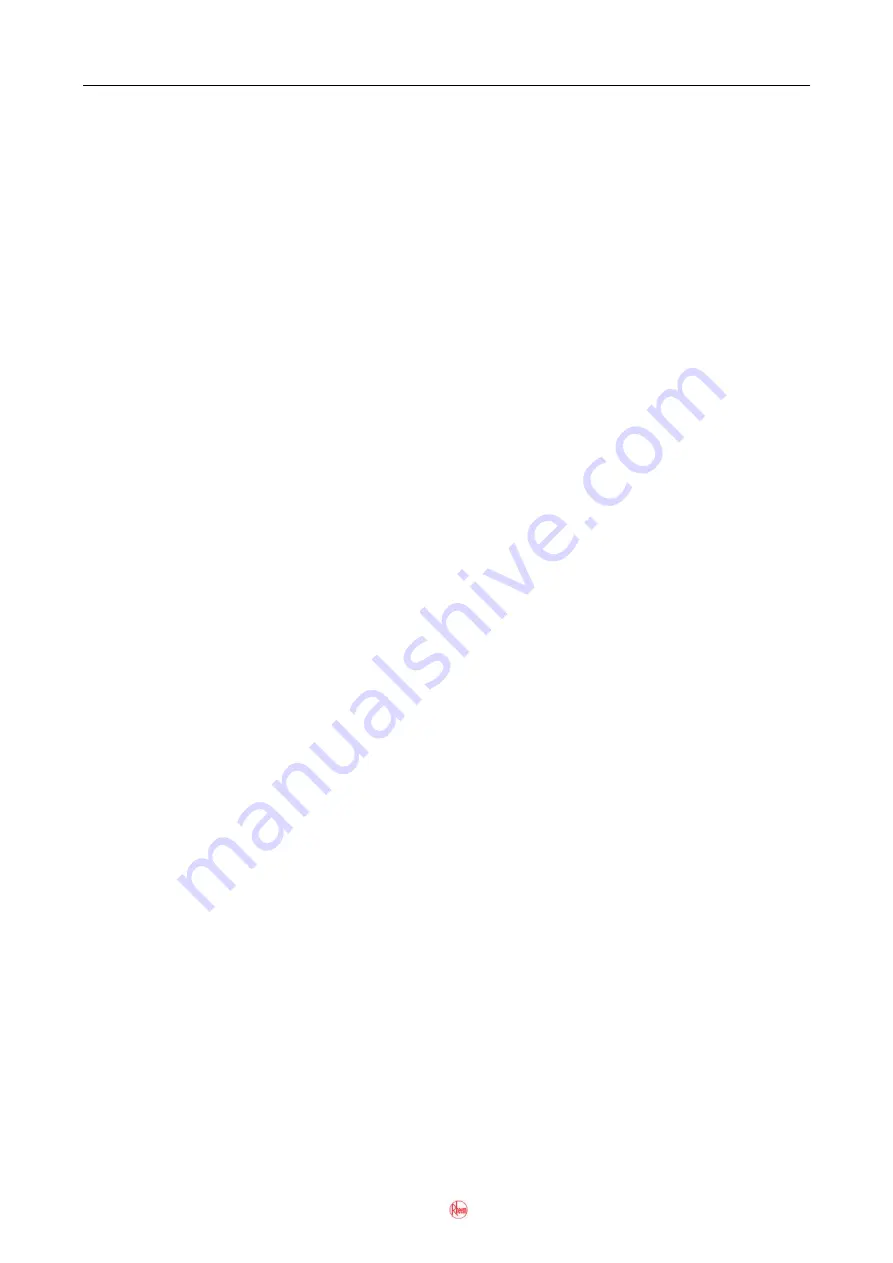
13
This document is stored and maintained electronically by
Service. All printed copies are deemed uncontrolled.
TM077: 325 & 410 Series II Heat Pump Service Instructions
Rev 00: Issued April 2014
OPERATION
The heat pump controller contains a main relay that ensures only the heat pump
or
the
booster element can be operated. The main relay will enable element operation in its un-
powered (off) state. Whenever power is available and element heating is not being used,
the controller energises the main relay to enable heat pump operation.
When heat pump operation is enabled and occurring, power for the compressor is passed
through an electronic switch called a triac, which is downstream of the main relay and
allows the controller to switch the compressor on and off in response to the demand for
heat pump heating.
Downstream of the triac, power for the compressor also passes through the load side of a
compressor switching relay. The compressor switching relay prevents compressor
operation in the event of high refrigerant pressure, via a high pressure switch in the
refrigeration system. The compressor switching relay will enable compressor operation in
its powered (on) state.
The compressor switching relay‟s coil side is fed power from the main relay when the main
relay is in its powered (on) state, via the refrigerant high pressure switch. This way, the
compressor switching relay is energised whenever heat pump heating enabled, and it will
not switch the compressor load unless it is de-energised as a result of the refrigerant high
pressure switch opening.
The 325 & 410 Series II Heat Pump Water Heaters utilise R134a refrigerant to transfer
heat from the atmosphere to the water in the storage tank.
The four main components of the sealed refrigeration system are the compressor,
condenser (heat exchanger), thermostatic expansion (TX) valve and the evaporator.
Refrigerant enters the compressor as a low pressure superheated vapour. The
compressor increases the pressure of the refrigerant vapour by decreasing its volume, as
well as increasing its temperature due to the addition of the heat of compression.
The high pressure, high temperature superheated refrigerant vapour flows to the
condenser (heat exchanger), where it gives off its heat. This heat is absorbed by the water
from the storage tank which is being circulated through a separate chamber in the
condenser. As the refrigerant gives off its heat and becomes cooler, it condenses
(changes state) to a saturated liquid. Cooling of the saturated liquid refrigerant continues
such that it becomes subcooled, meaning it is cooled to a temperature below its saturation
point.
The liquid refrigerant then moves through the thermostatic expansion (TX) valve, where it
is expanded to a lower pressure by moving through the TX valve‟s orifice. The expansion
process also lowers the temperature of the refrigerant, to a point below that of the
surrounding ambient air.
The TX valve has a bulb that senses the temperature of the suction line at the evaporator
outlet. The TX valve thermostatically meters the flow of expanding refrigerant in response
to the temperature of the suction line.
Following expansion, the low pressure, low temperature refrigerant moves into the
evaporator where it absorbs heat from the surrounding ambient air. As the refrigerant
absorbs heat and becomes warmer, it evaporates (changes state) to a saturated vapour.
Heating of the saturated refrigerant vapour continues such that it becomes superheated,
meaning it is heated to a temperature above its saturation point. This low pressure
superheated vapour then returns to the compressor to complete the cycle.