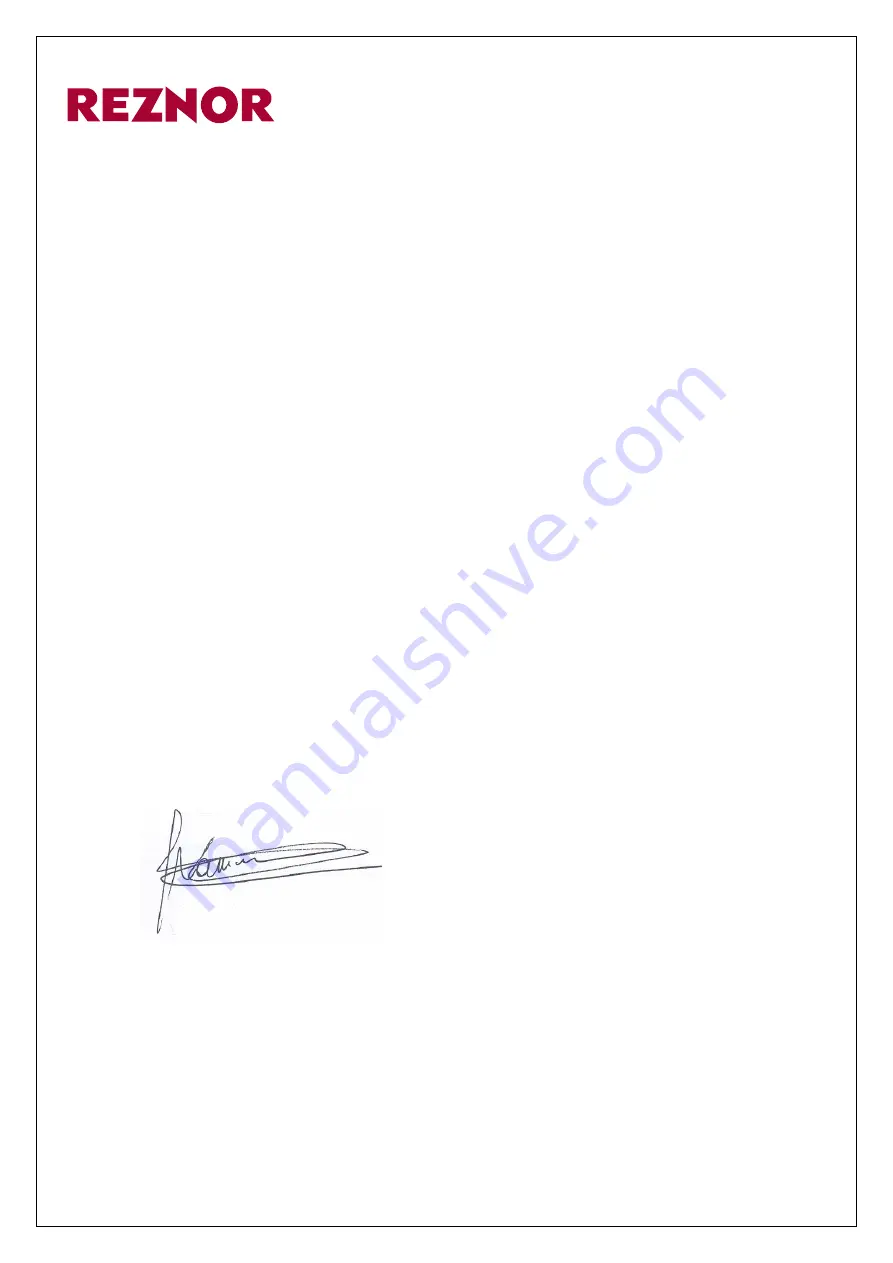
®
REZNOR CERTIFICATE
EC DECLARATION OF CONFORMITY
FOR MACHINERY
(Directive 2006/42/EC, annexe II, sub A
Reznor Europe N.V.
J & M Sabbestraat 130
B 8930 MENEN (Belgium)
Herewith declares that :
The gas-fired air heaters REZNOR, series SDH and RDH
Are in conformity with the provisions of the Machinery
Directive as amended and with national implementing
legislation.
Menen, 4.09.2012
Reznor Europe N.V.
C. Grammens
Engineering & Development Manager Reznor Europe