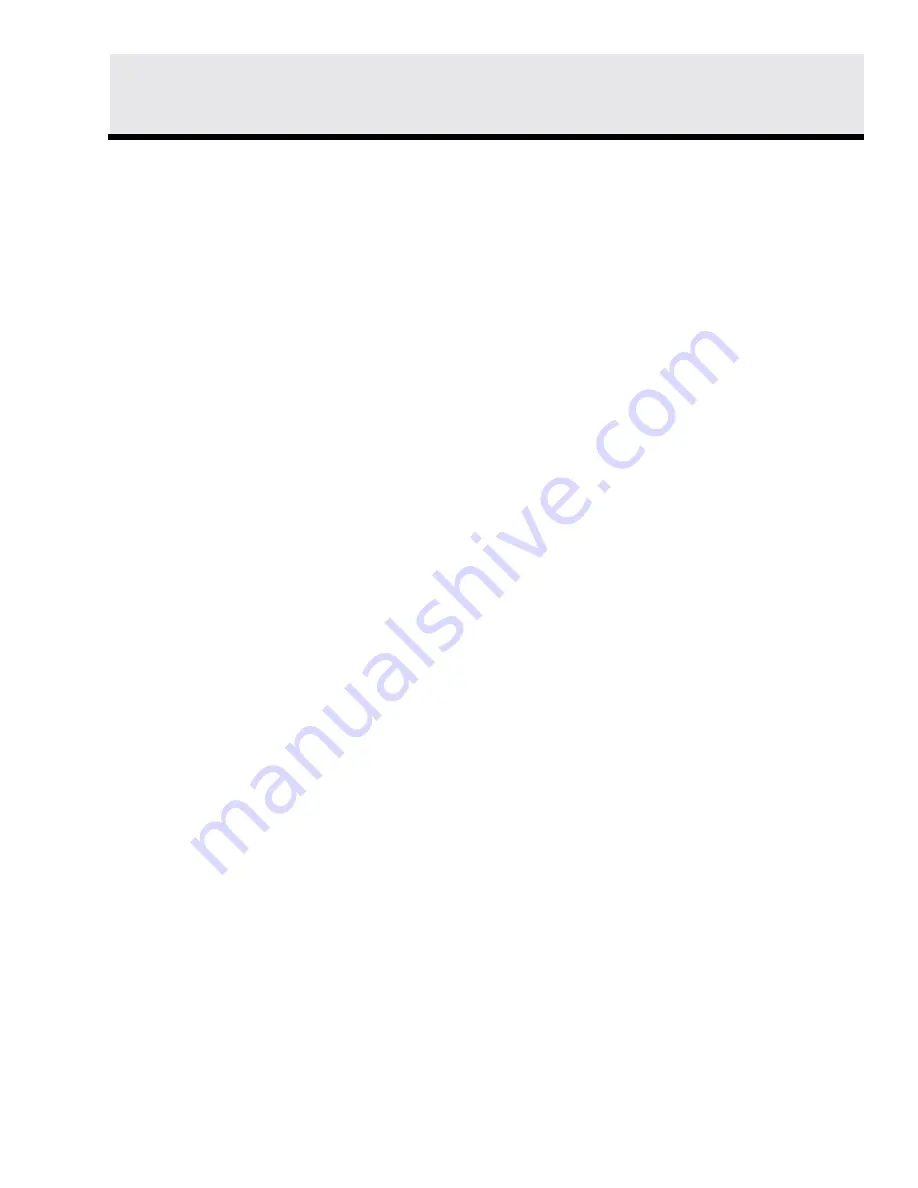
Form I-RA/D 140/235 (Version A), Mfg No. 110318 Rev 4, Page 19
Priming and
Leak Check
For control locations,
refer to illustration on
page 38
Priming and Checking the System
The oil supply line to the heater must be full of oil and free of air for
proper heater operation.
NOTE:
Priming the oil line could take up to 30 minutes depending
on the length of the line.
Follow the procedure below to fill the oil line.
1. Be sure the oil tank is filled to at least six inches above the
top of the foot valve.
Burner
Start-Up
System Check
Check Test - Prior to Start-Up
You should check your system completely before operating it.
Check clearances from combustibles. Be certain that the
clearances are in compliance with the appropriate Codes.
Check hangers and supports. Be certain that all hangers,
supports, and arms are adequately anchored and that all
unions or threaded fittings are snug and do not rotate. Heat
-
er must be level.
Check to make sure all shipping supports have been re-
moved.
Check the electrical supply. Be sure that all wire gauges are
as recommended and that the supply voltage is as stated
on the heater. Determine that fusing or circuit breakers are
adequate for the load.
Check vents. Be sure that vent pipe and chimney meet the
requirements and appropriate codes. A UL or CSA/UL listed
draft regulator is required. A Reznor
®
(Option CC1) or Type
L Breidert Air-X-hauster
®
vent cap is recommended. (Type
L Air-X-hauster
®
is a trademark of The G. C. Breidert Com-
pany.)
Check the oil supply. Fill the supply tank to at least six inches
from the top of the foot valve.
NOTE:
Always screen used oil
with a 70-80 mesh strainer when filling the supply tank.
Canadian RAD (blower model) installation only -- Be sure an
inlet air duct is installed in compliance with Codes.
Heater Start-Up