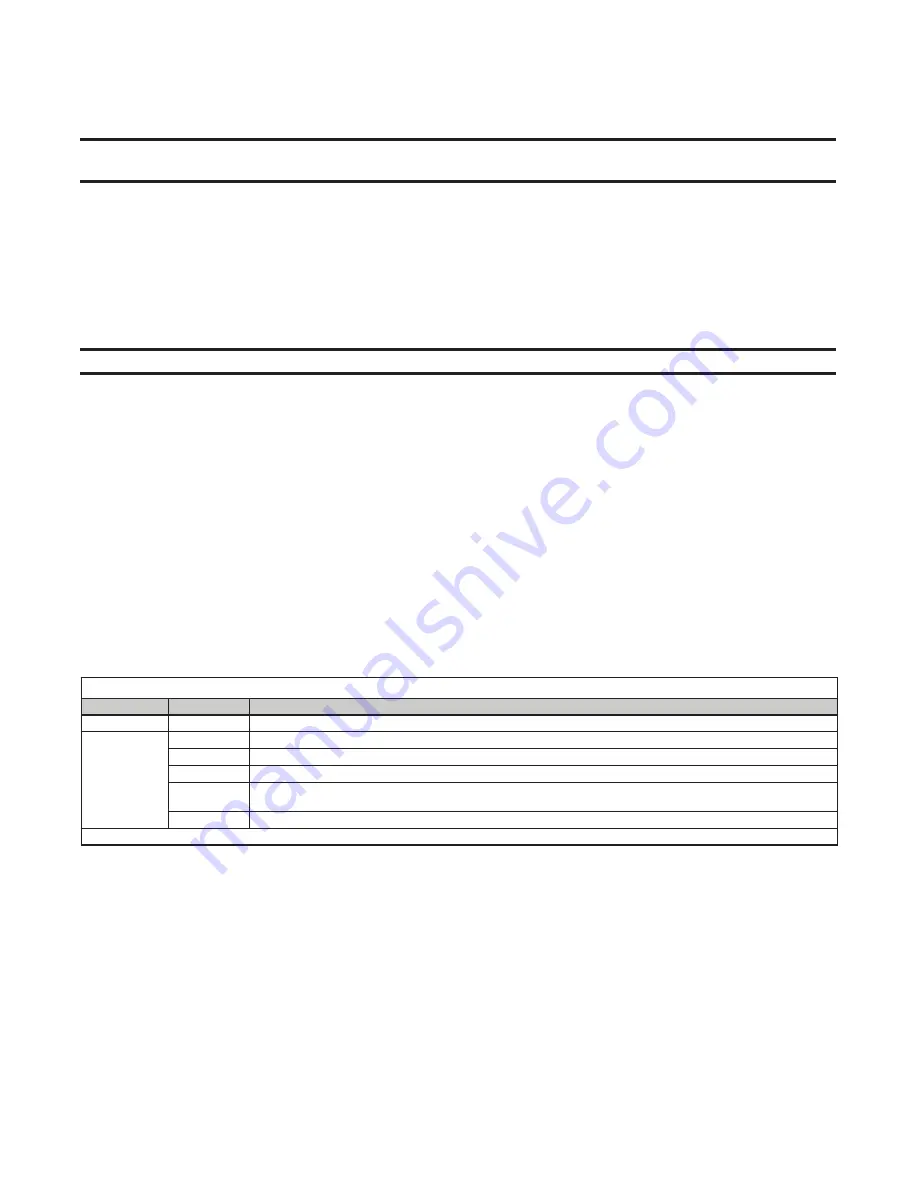
8
RP-HRPD-IOM (07-22) 132210-B
GENERAL INFORMATION—CONTINUED
Hazards of Chlorine
NOTE: Remember, chlorine is heavier than air. This fact should be kept in mind when determining
the installation location of heaters and building exhaust systems.
The presence of chlorine vapors in the combustion air of heating equipment presents a potential corrosion hazard .
Chlorine, found usually in the form of Freon or degreaser vapors, when exposed to flame will precipitate from the
compound and form a solution with any condensation present in the heat exchanger or associated parts . The result
is hydrochloric acid, which readily attacks all metals, including 300 grade stainless steel . Care should be taken to
separate these vapors from the combustion process . This may be done by wise location of the unit with regard to
exhausters or prevailing wind directions .
INSTALLATION
NOTE: Before installation, make preparations for necessary supplies, tools, and manpower.
Uncrating/Unpacking
•
This furnace was test-operated and inspected at the factory prior to crating and was in operating condition . If
the furnace has incurred any damage in shipment, document the damage with the transporting agency and
immediately contact an authorized Reznor
®
distributor . If you are an authorized Distributor, follow the FOB freight
policy procedures .
•
Check the rating plate for the gas specifications and electrical characteristics of the furnace to ensure that they
are compatible with the gas and electric supplies at the installation site .
Shipped-Separate Parts
•
Check to see if there are any field-installed options that need to be connected to the furnace prior to installation .
•
Shipped-separate options could include a gas shutoff valve, a vertical vent terminal, a thermostat, an optional
control, and disconnect switch .
•
Some gas control options will have parts either shipped loose with the heater or shipped separately . If the unit is
equipped with any of the gas control options listed in
, ensure that these parts are available at the job site .
Table 6. Shipped-Separate Parts for Gas Control Options
Application
Option
Part(s)
Heating
AG7
Thermostat (PN 48033)
Makeup air
AG3, AG4
Control switch (PN 29054)
AG8
Control switch (PN 29054); sensor and mixing tube (PN 48041)
AG9
Control switch (PN 29054); remote temperature selector (PN 48042); sensor and mixing tube (PN 48041)
AG15, AG17 Control switch (PN 29054); remote temperature selector (PN 115848); stage adder module (PN 115849);
discharge air sensor holder (PN 115850); discharge air sensor holder bracket (PN 213612)
AG39, AG41 Remote temperature selector (PN 174849); temperature sensor (PN 133228); mixing tube (PN 90323)
NOTE: If an optional remote console is ordered, the control switch and temperature selector may be mounted on the console .
Pre-Installation Modifications
High CFM Conversion
This unit was factory assembled with the air throughput range listed on the rating plate . If the application requires
a higher CFM than listed on the rating plate, the unit may be converted for lower temperature rise and higher CFM .
The conversion will change the air throughput range as specified in
. Verify the unit size on the heater rating
plate and, after confirming that this conversion is correct for the unit, perform the following procedure: