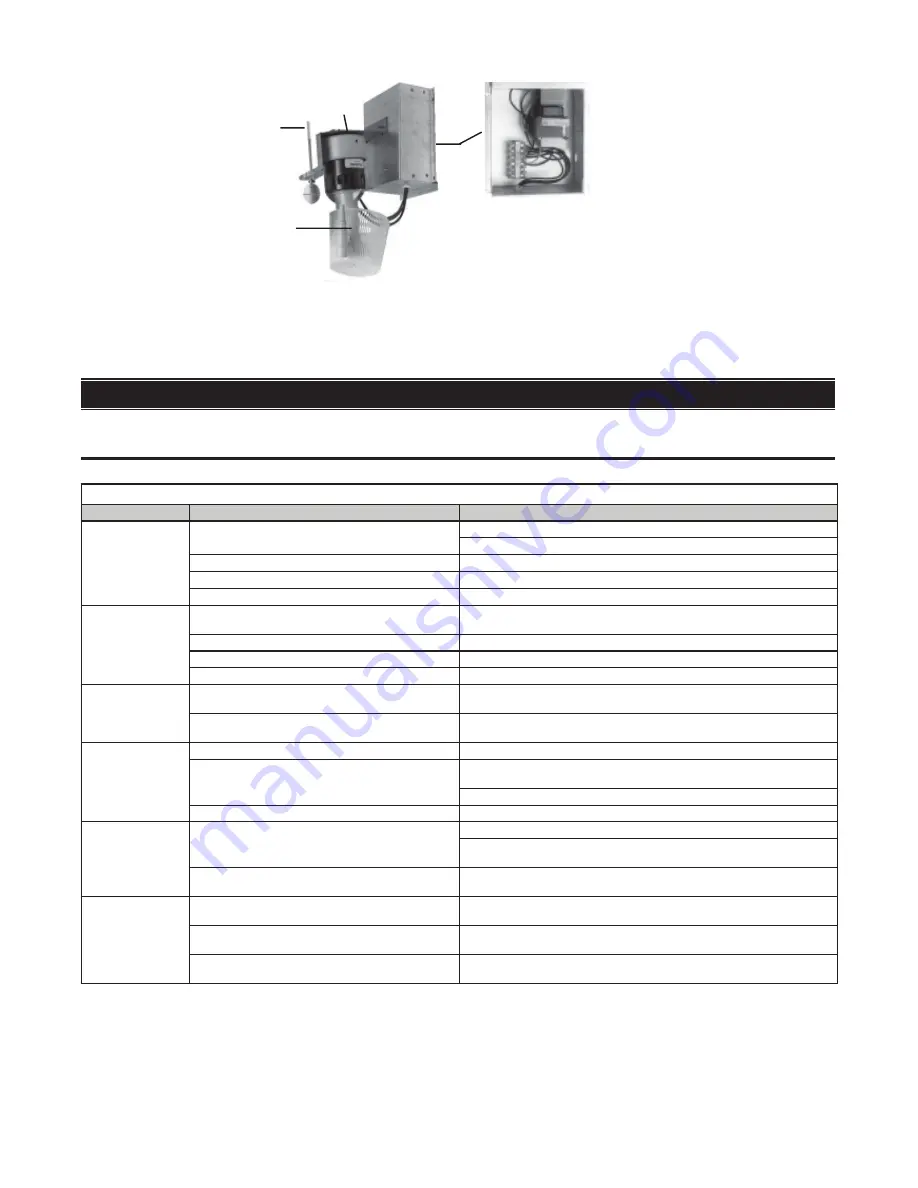
15
OPT-AS3,4,5,8 (07-22) 160202-B
Figure 16. Water Pump
TROUBLESHOOTING
⚠ DANGER ⚠
Disconnect the power before servicing the cooling module. Failure to do so can cause electrical
shock, personal injury, or death.
Float
Switch
Pump
Motor
Pump
Junction Box
NOTE: Only 208V unit has
transformer in junction box.
Table 5. Troubleshooting
Symptom
Probable Cause
Remedy
A. Pump doesn’t
run (pump and
float system)—unit
calling for cooling
and reservoir
1. Electrical connections (low voltage)
Verify all electrical connections
Verify correct voltage at pump terminal H
2. Electric float switch
Check position of actuators on electric float switch
3. Dirty pump
section)
4. Defective pump
Replace pump
B. Required water
level (3 inches) not
being maintained
(pump and float
control system)
1. Float valve
Filling and Adjusting Water Level in
section)
2. Drain and fill valves not working properly
Check valves for proper operation
3. Incorrect overflow pipe nipple
Replace pipe nipple with 3-1/2-inch nipple
4. Drain leaking
Tighten drain fittings
C. Water running
off media pads
1. Excessive water flow
Adjust ball valve in distribution line (refer to
section)
2. Dirty media pads
Clean or replace media pads (refer to
D. Water not
distributing evenly
1. Distribution line clogged
Flush distribution line (refer to
2. Holes in distribution line turned
Check position of distribution line—holes should be spraying upward
toward diffuser
Adjust position of line if not positioned with holes toward top
3. Pump not running on correct voltage
Check voltage at pump terminal in cooling module junction box
E. Media pads
becoming clogged
and discolored
(scale and salt
deposits) quickly
1. Bleed line clogged or inadequate bleed-off
(pump and float control system)
Clean bleed line (refer to
section)
Uniform buildup of minerals on entering air face of media indicates
insufficient bleed-off—increase rate until mineral deposits dissipate
2. Excessive water flow
Adjust ball valve in distribution line (refer to
section)
F. Water blow-
off from media
pads or water
being pulled from
reservoir
1. Media pads installed incorrectly
Install media pads correctly (refer to
2. Requires moisture elimination pad
Install moisture elimination (over 600 FPM) pad (refer to
3. Water level not 3 inches
(pump and float control system)
Refer to probable causes and remedies for symptom B above