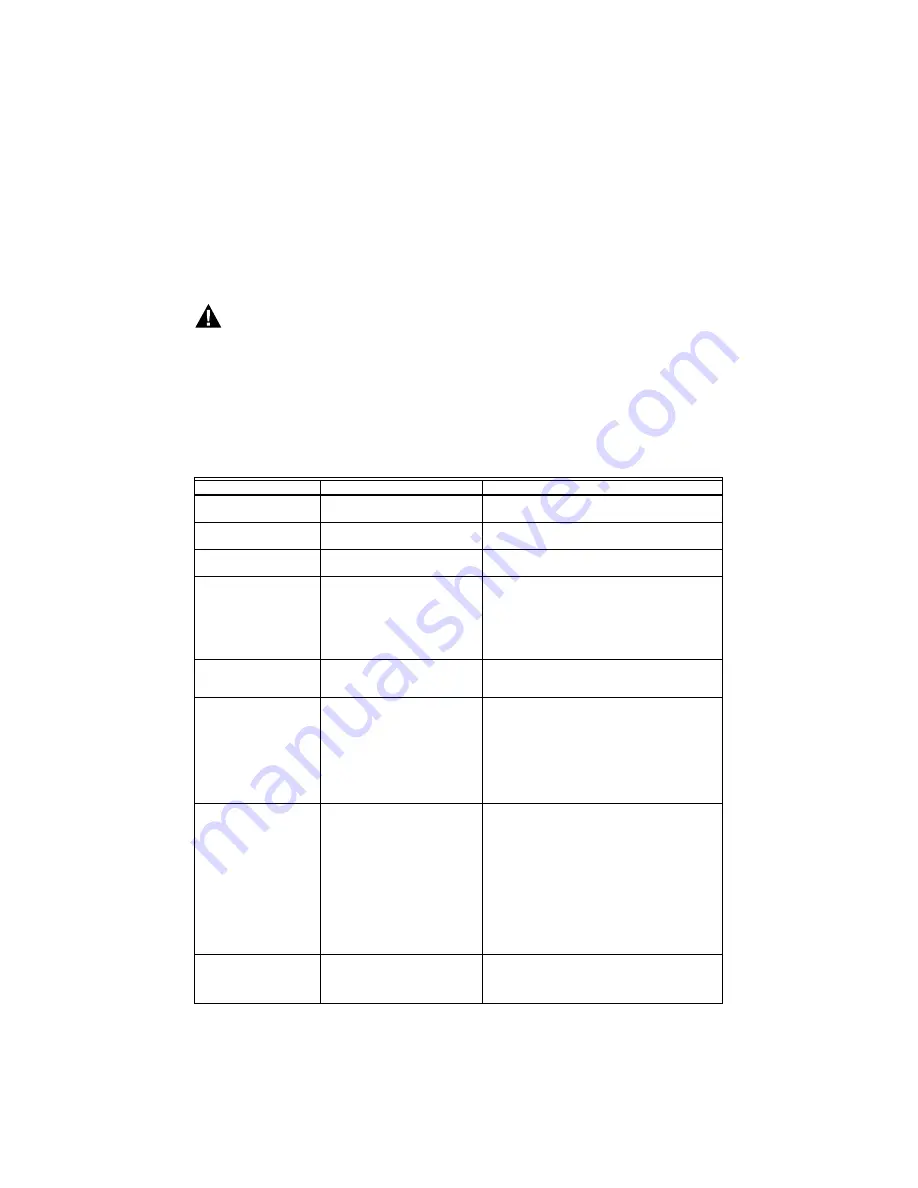
SMARTVALVE™ SYSTEM CONTROLS
69-1059—01
14
4.
After LED flash code analysis and appliance repair are complete, turn the thermostat below room temperature
for 10 seconds; turn the thermostat above room temperature to initiate a new call for heat.
5.
Observe the ignition sequence, comparing it to the Sequence of Operation shown in Fig. 12. Allow the new igni-
tion sequence to proceed until appliance lights or an abnormal or unexpected event is observed. See next sec-
tion.
Troubleshooting Without LED Indicator Assistance
Appliance power or thermostat call for heat has cycled since appliance failure occurred.
WARNING
LINE VOLTAGE POWER CAN CAUSE PRODUCT DAMAGE, SEVERE INJURY OR DEATH
Only a trained, experienced service technician should perform this troubleshooting.
1.
Make sure the appliance power is on and any manually operated gas cock on the appliance is open.
2.
Remove appliance burner compartment door. Confirm that SV9540; SV9640 LED indicator is flashing in a
“bright -dim” sequence.
3.
Make sure the ignition system control switch is in the ON position.
4.
Disconnect the system thermostat leadwires at the ST9160 EFT or the 208907 Terminal Board.
5.
Using alligator clips on a short jumper wire, jumper the R and W terminals on the EFT or Terminal Board.
6.
Observe the appliance operation, comparing it to the Sequence of Operation shown in Fig. 12 . Allow the ignition
sequence to proceed until the appliance lights or an abnormal or unexpected event is observed.
7.
Check the appliance as shown in the following table:
If
And
Check/Repair
Combustion air blower
does not energize.
2 Flash code does not come on 30
seconds after call for heat starts.
1. Combustion air blower wiring
2. Combustion air blower
Combustion air blower
does not energize.
2 Flash code does come on 30
seconds after call for heat starts.
1. Airflow proving switch stuck closed.
2. Airflow proving switch miswired or jumpered.
Combustion air blower is
energized.
3 Flash code does not come on
after 30 seconds.
Wait for the prepurge time to expire
3 Flash code comes on 30
seconds after combustion
air blower is energized.
Combustion air blower turns off.
1. Ignition system control switch must be in the ON
position.
2. Airflow proving switch stuck in open position.
3. Airflow proving switch tubing and wiring
4. Obstructions or restrictions in appliance air intake
or exhaust flue system that prevent proper
combustion air flow.
Prepurge time has expired. HSI element does not glow red
within 5 seconds.
1. Broken or damaged HSI element
2. Broken or damaged HSI element leadwires
3. SV9540; SV9640 failure to power HSI element.
HSI element is glowing
red.
Pilot does not light during the 90
second trial for ignition.
NOTE: HSI element will turn off for
approximately 25 seconds during
the 90 second trial for ignition.
1. Pilot tubing not purged of air [Intiate another
ignition sequence with the R-W jumper to clear pilot
tubing more quickly]
2. Inlet gas pressure too low for proper appliance
operation.
3. Pilot burner improperly positioned in airflow
4. Clogged or incorrect pilot orifice.
5. Combustion air blower moving pilot gas away
from HSI element.
Pilot lights during trial for
ignition.
Main gas does not flow.
If pilot flame is not sensed during
trial for ignition, main valve will not
open. System will shut off HSI
element and pilot gas flow, go
through a 5 minute delay period,
then initiate another ignition trial.
1. Line voltage to L1 terminal of ST9160 or Terminal
Board must be 120 volts with reference to appliance
chassis.
2. Appliance must be reliably connected to earth
ground.
3. Combustion air blower moving pilot flame away
from pilot burner flame rod.
4. Inlet gas pressure too low for proper flame
sensing.
5. Flame sense rod contaminated or in incorrect
location.
6. Wiring between SV9540; SV9640 and pilot burner
must be in good condition and properly connected.
Main burner lights.
Circulating air fan is not turned on
after appropriate delay time
(systems with ST9160 Electronic
Fan Timer only).
1. Wiring between SV9540; SV9640 and ST9160 EFT.
2. Proper operation of ST9160 EFT.