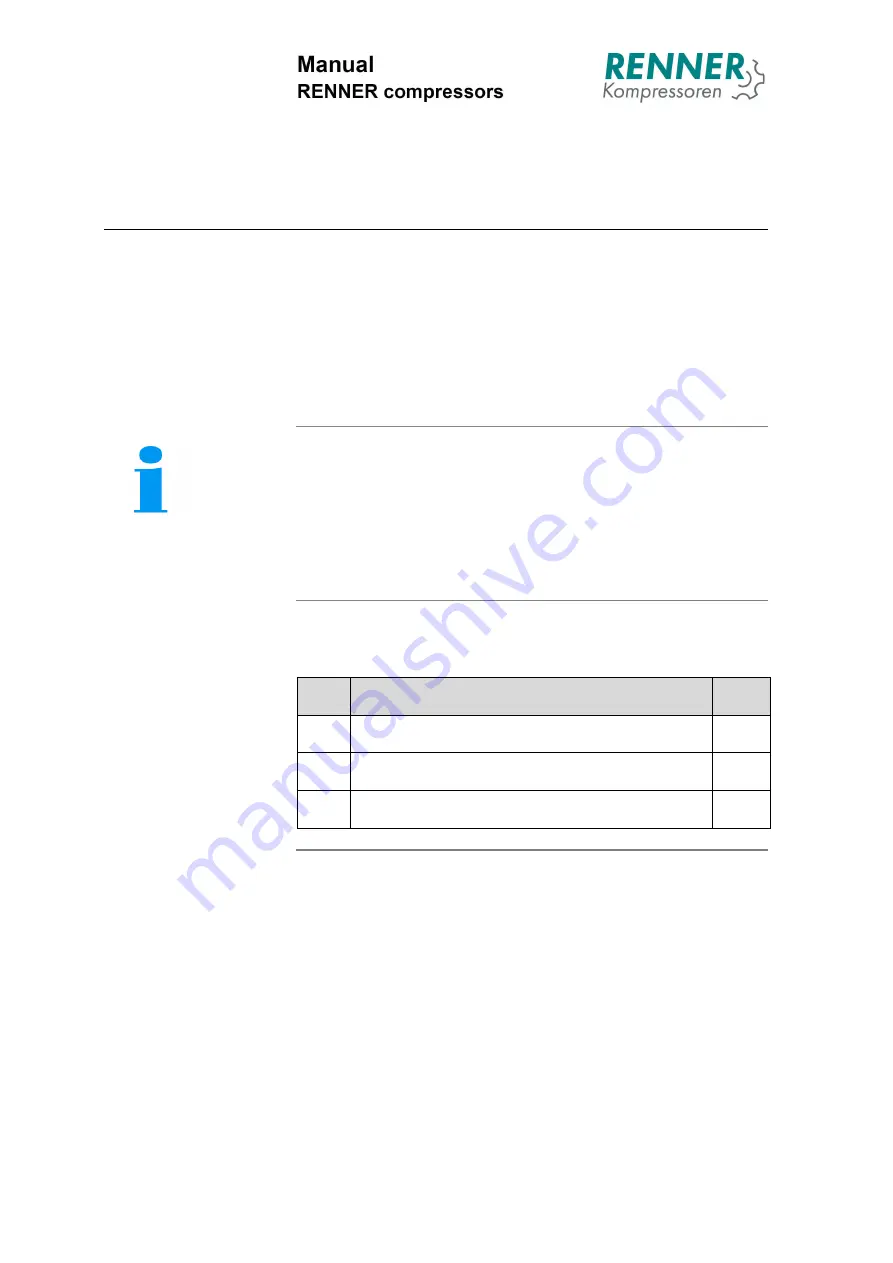
1 Safety
1 - 1
Chapter 1
Safety Instructions
This chapter covers the following:
Explanation of the symbols used
basic instructions for the safe handling of the compressor
as well as
instructions for conduct in the event of accidents.
Important Note!
The following safety instructions are to be regarded as a sup-
plement to the already applicable national accident prevention
regulations and laws.
Any existing accident prevention regulations and laws must in
all cases be adhered to.
This chapter is subdivided into the following sections:
No.
Subject
Page
1.1
Symbols
1-2
1.2
Basic safety instructions
1-3
1.3
Conduct in case of accidents
1-6
Contents
Overview
Summary of Contents for Scroll Line Industry Series
Page 60: ...Appendix T Data sheets 015x765x1462 AT Appendix Data sheets AT...
Page 62: ......
Page 63: ......
Page 64: ......
Page 71: ......
Page 72: ......
Page 73: ......
Page 92: ...A ADS Appendix Pressure Switch AADS 2 Appendix ADS End Pressure Switch...