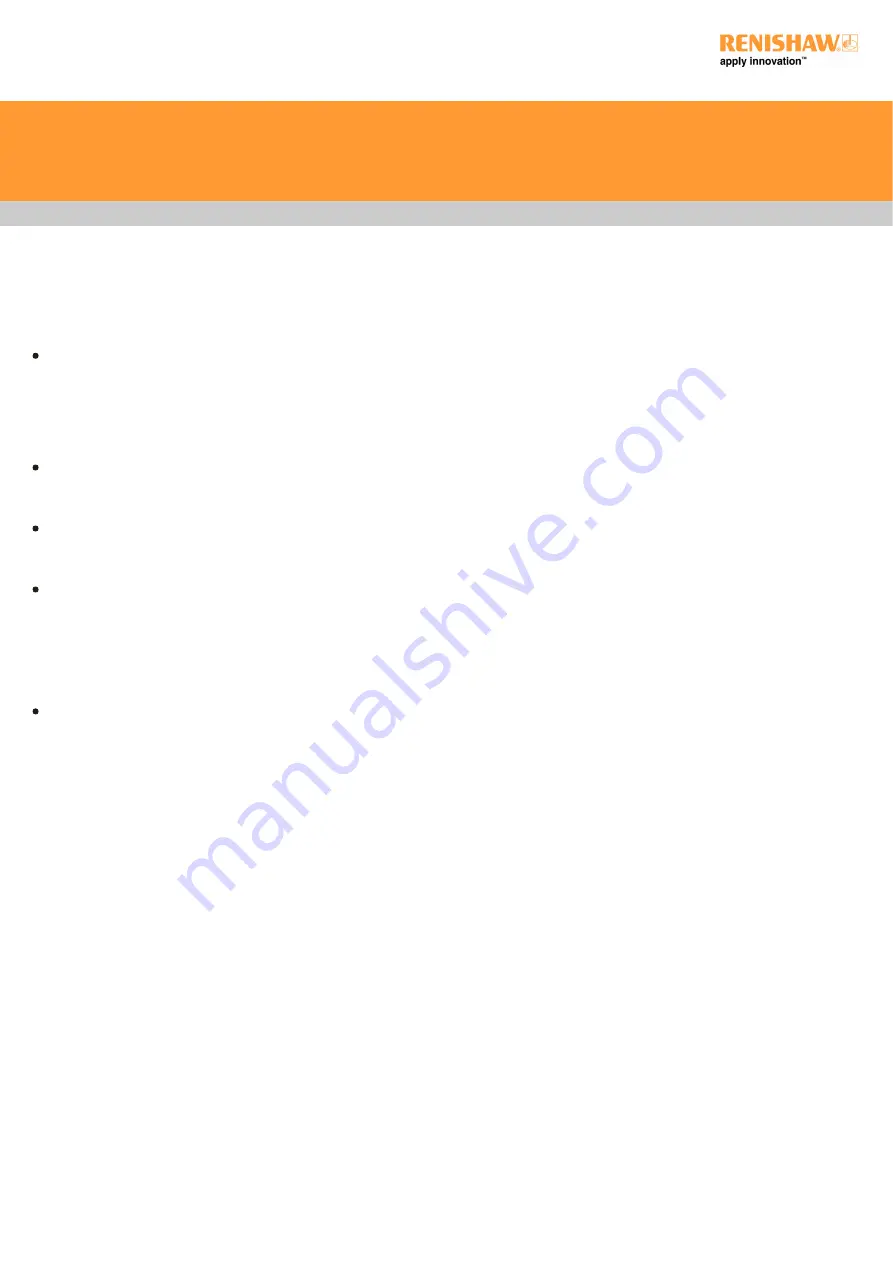
Calibrating an RFP1
1. At the start of the qualification process, the RFP1 will move from its current position to the safe position values defined in the FA10
dialogue box.
User must take care to ensure that there is a clear line of sight from the current position to the FA10 safe position before requesting a
qualification
2. Images will be taken on the P2H disk to normalise the illumination levels and set the triangulation spot position.
3. RFP1 will take images of the pillar to determine the properties of the camera lens.
This aligns the RFP1 camera position to the REVO-2 reference frame, providing the link to RSP2 calibration
4. RFP1 will then take images of the P2H ceramic disc surface to calibrate the fringe pattern.
The triangulation spot is also calibrated during this stage
5. A verification routine is performed automatically at the end of a qualification routine.
RFP1 takes images of the pillar at different head angles to verify the lens parameters
Verification of an RFP1
1. At the start of the verification process, the RFP1 will move from its current position to the safe position values defined in the FA10 dialog
box.
User must take care to ensure that there is a clear line of sight from the current position to the FA10 safe position before requesting a
verification
2. RFP1 takes images of the pillar at different head angles to verify the lens parameters.
Using FA10 for vision calibration
FA10 can also be used to calibrate RVP, instead of using the VA11 calibration artefact.
RFP1 user's guide
www.renishaw.com
Issued 06 2022
19