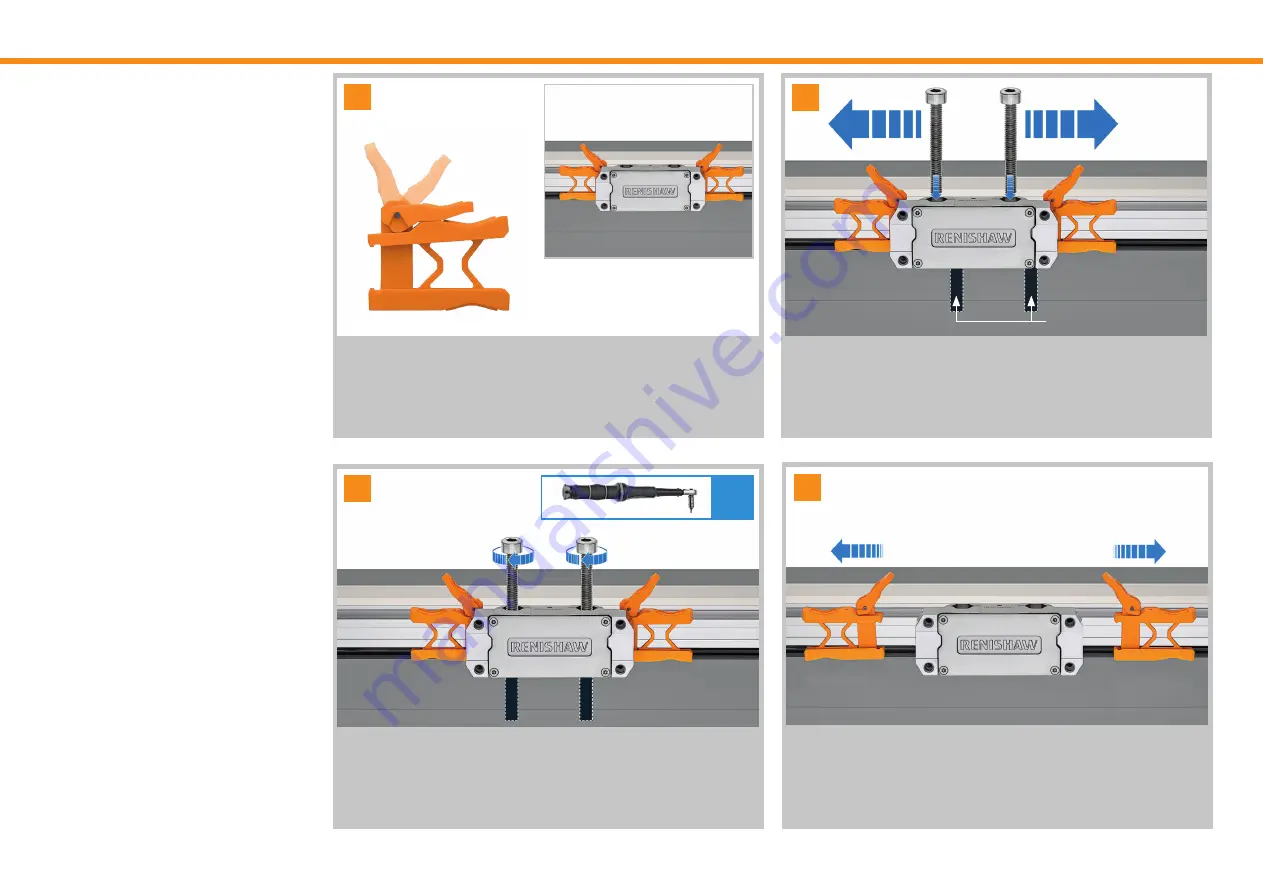
4
3
2
1
17
Original instructions
Set the alignment brackets to position 2.
Slide the readhead to align the readhead mounting holes to the machine
slideway mounting holes.
Secure the readhead using 2 × M6 screws; tighten screws to a torque of
8 Nm.
Pull alignment bracket lever upwards into position 3 to open the alignment
bracket. Slide the alignment brackets away from the readhead and remove
from the extrusion.
NOTE:
The alignment brackets must be removed after installation.
14.3.1 Installation using the alignment
bracket method
2
Machine slideway
mounting holes
3
4
1
8 Nm